A family-owned Norwegian company with their own sawmill recently approached Stronga with the intention of investing in a reliable batch woodchip drying station. Their goal was to optimise revenue income from wet residual woodchip which accounts for up to 40% of each roundwood tree. The client wanted to take advantage of strong local market demand for dry woodchip as a boiler fuel at circa 25% moisture.
Stronga advised on technical sizing of the heat source and airflow and offered a suitably-scaled container drying solution for the customer’s needs. Our team enabled the client to calculate costs per m³ to dry and the financial viability of the project; this allowed them to envisage the potential of generating tonnes of dry woodchip from spare resources.
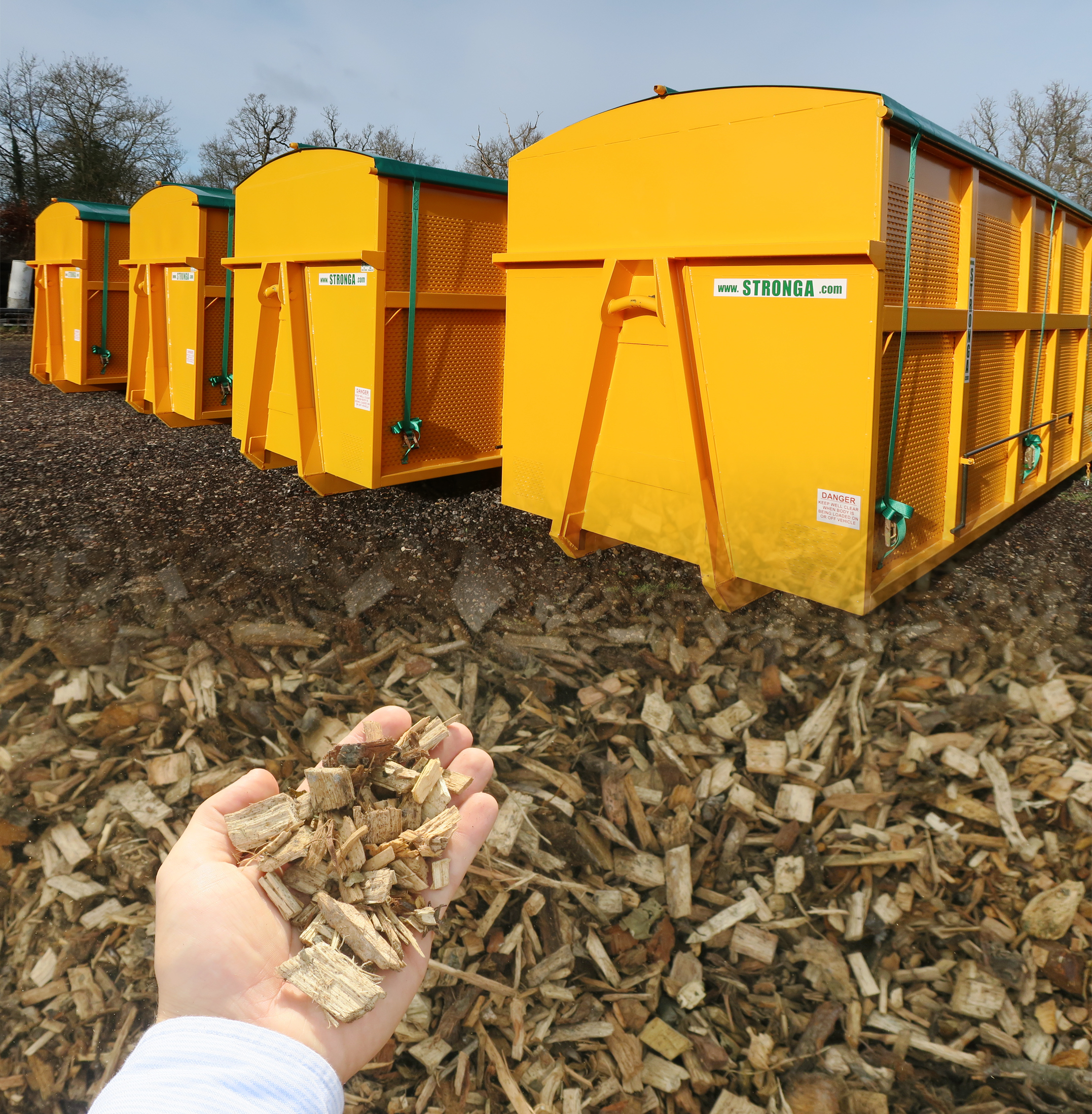
Woodchip & Wood Products Are in High Demand
Manufacturing wood products create large volumes of off-cuts while increasing demand for wood creates higher quantities of woodchip. The outcome is a situation where woodchip is becoming more abundant in markets across the globe.
In Norway, wood is the dominant material used for residential housing construction. Famed for its aesthetic (see below) and breathable qualities; wood cladding is a popular choice for Norwegian home owners. However, despite forestry being one of the higher contributors to bioenergy production, Norway’s current production rate is comparably low on a global scale. Stronga’s drying systems allow this particular client to contribute positively to increasing renewable energy production from highly calorific woodchip fuel.
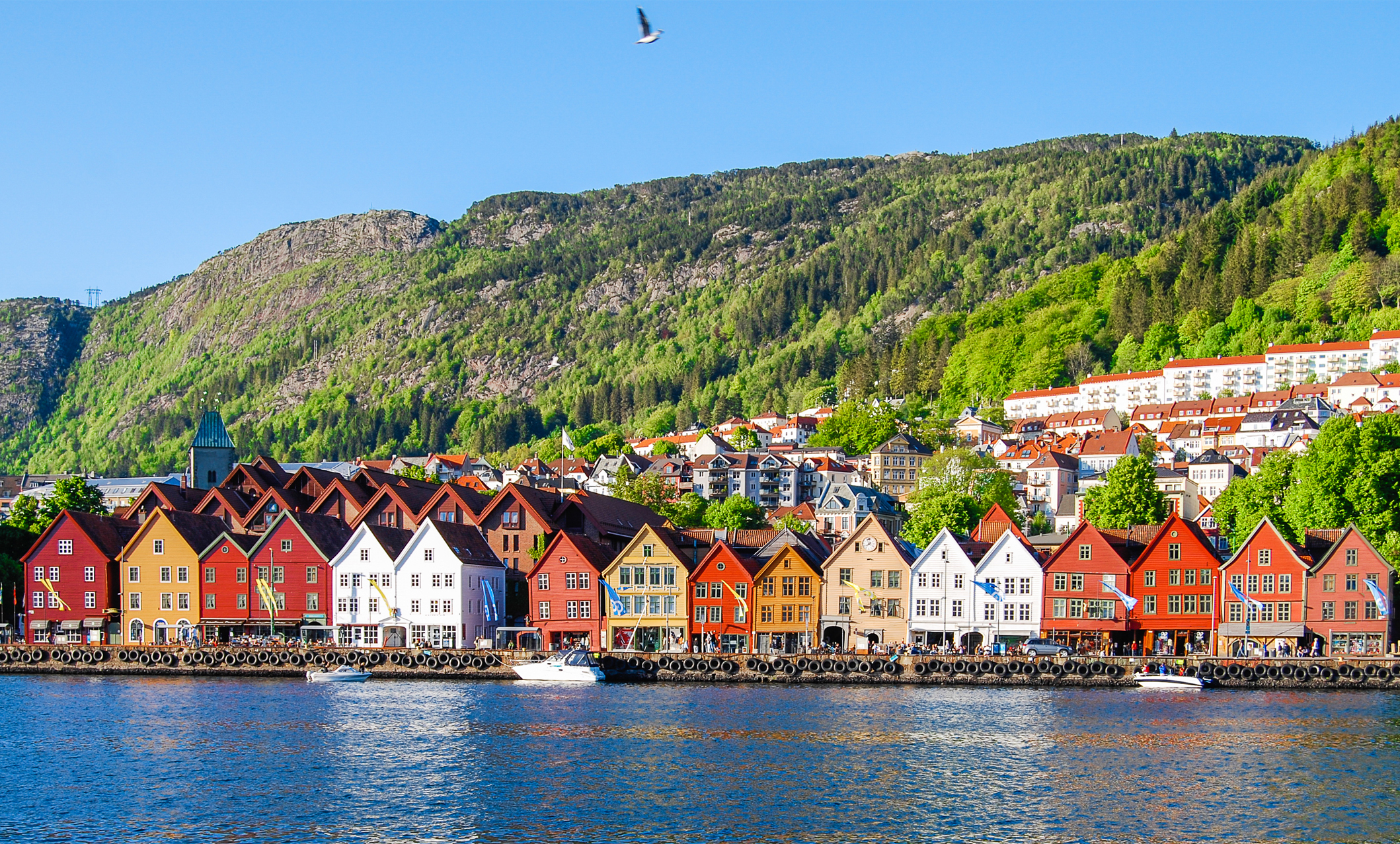
Matching Supply & Demand
During the consultation period, our client explained that they had recently built an on-site sawmill to help them satisfy high demand for construction timber with the potential to also sell valuable woodchip fuel, locally. Using Stronga’s container woodchip drying solutions, the client is able to create an additional income stream with minimal operational costs, utilising an otherwise wasted resource for extra profit.
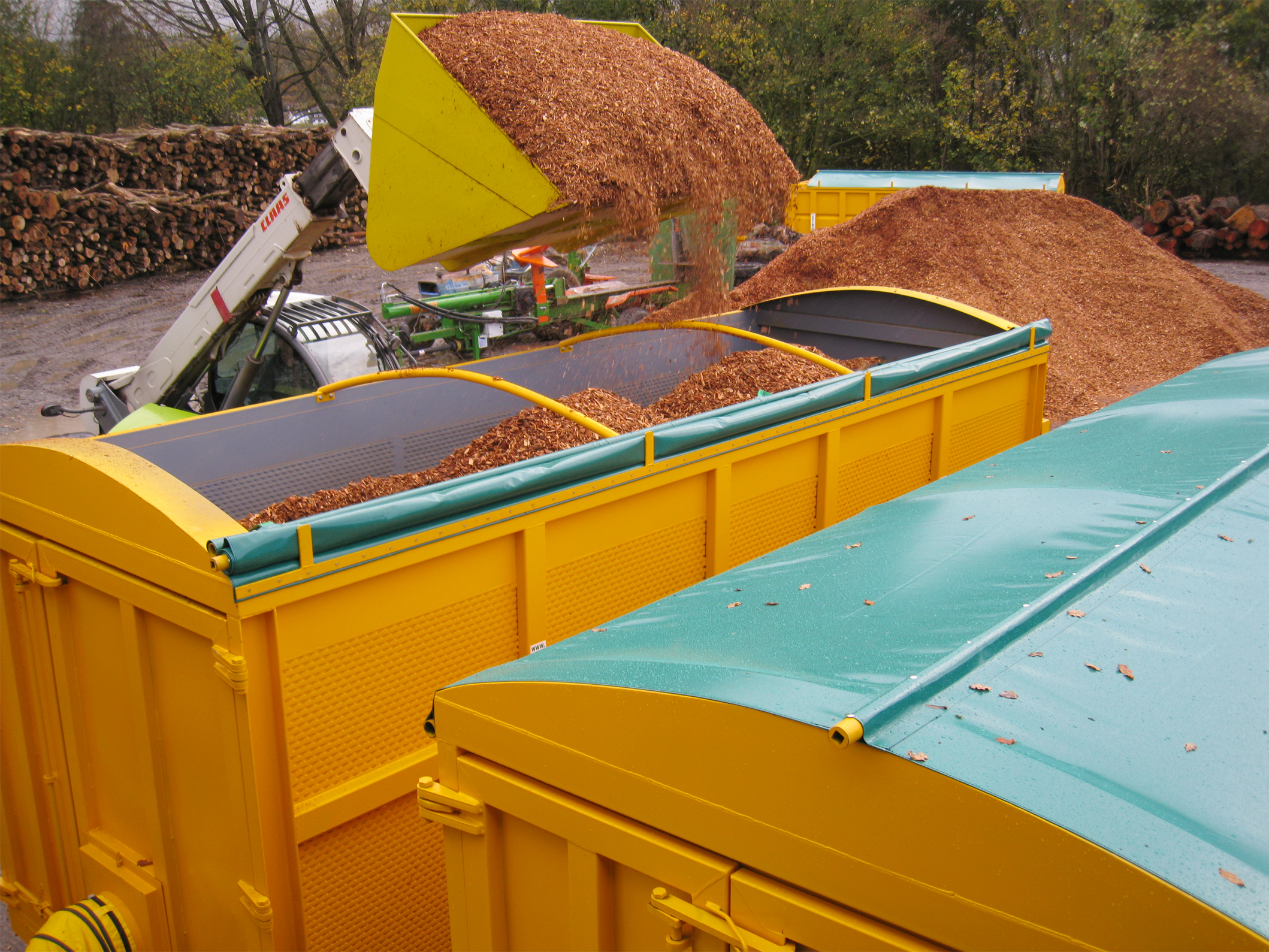
A Personal Touch from Stronga
Stronga encourage customers to engage in 1:1 discussions with our technical team, especially at an early stage in the project, to receive expert advice from our experienced advisers. After carefully considering this client’s input material properties, local climate, heat source and other parameters, our team decided that a small-scale Container Drying Station was the most cost-effective and suitable solution for their needs.
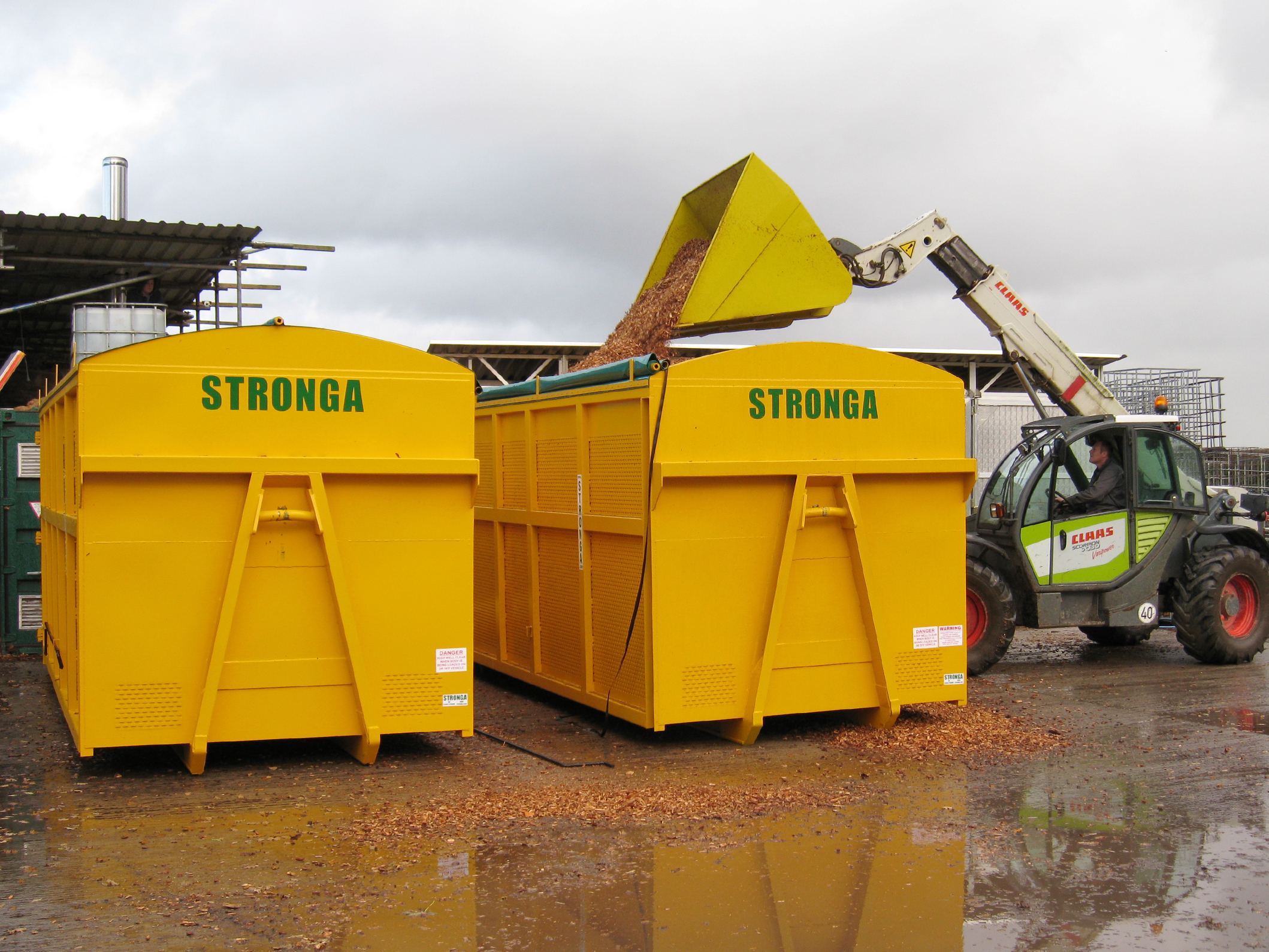
The Perfect Match
At full production, this particular Norwegian sawmill had a potential output of 10,000m₃ of woodchip a year but, at point of consultation, they were working in a start-up phase at approximately 3,000m₃ annually, aiming to sell woodchip year-round at a consistent 25% moisture content, setting them apart from competitors.
The Stronga team worked with the client and established the range of drying times for their project. Our team estimated the drying time, output quantity and energy consumption and explained the variable “uncontrollables” in drying, including weather conditions, biomass moisture content and more. It was agreed that by starting with two Stronga HAF drying containers, increasing to three later – they could achieve their goals. The drying process involved loading each drying container directly from a conveyor and moving the filled container to the drying station, minimising handling costs on-site. With drying complete, the same container would be delivered to the end user using a Stronga hook-lift trailer.
The animation below visualises the overall Stronga Drying Station process.
Handling & Delivery – Simplified
A key benefit of Stronga’s woodchip drying containers is that they can be automatically filled directly from the sawmill chip conveyor and then, when full, transported and connected to a Heatex via insulated, flexible ducting. After drying is complete, Stronga’s HookLoada trailer or a suitable hook-lift truck can then transfer the dry woodchip to the customer’s store; minimising handling costs. This efficient process enables the client to fill each container with up to 10m³ of wet woodchip a day and benefit from a well-proven batch drying process.
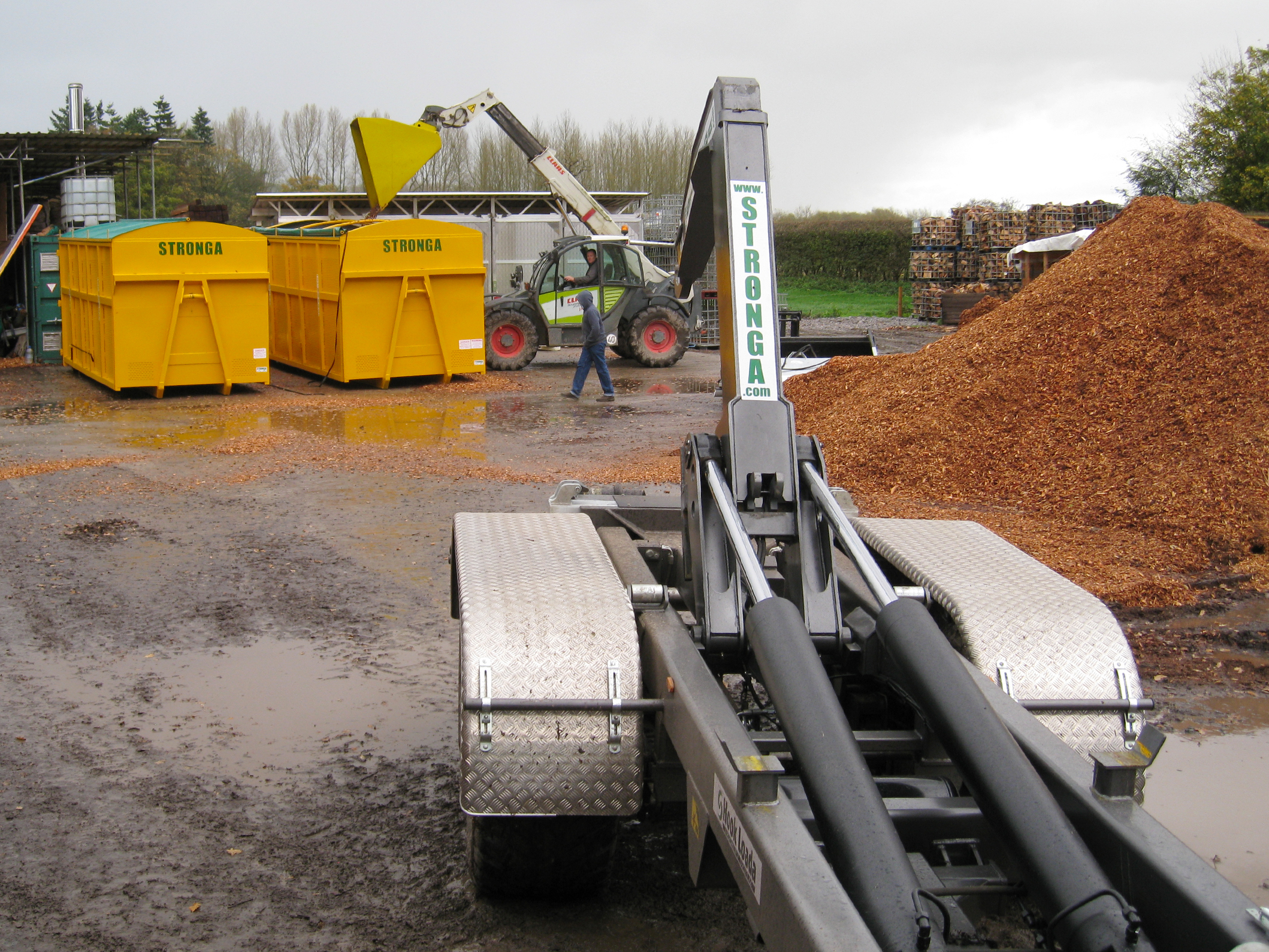
Why Smaller-Scale Businesses Choose to Dry Woodchip in Containers
Stronga’s clients recognise the potential of batch drying by-product wood chips in containers to maximise potential from a spent resource. With super-low handling costs, excellent space-efficiency and good drying performance with woody biomass materials, Stronga Drying Stations are an excellent solution for smaller-scale sites.
As the chart below demonstrates, drying significantly increases the calorific value of woodchip fuel. What’s more, drying also significantly reduces the chances of composting and moulding from decomposition activity, while dry woodchips flow better in conveyors, augers and boiler gratings, reducing the risk of blockages, downtime and issues in bio-heat production. Dry woodchips are also far easier and cheaper to export – providing an opportunity for owners to reach international markets.
Our client was pleased to know that our drying system would increase their customer satisfaction rate and overall sales income. They were keen to invest in efficient drying solutions, giving their woodchip a ‘clean-green’ stamp of approval.
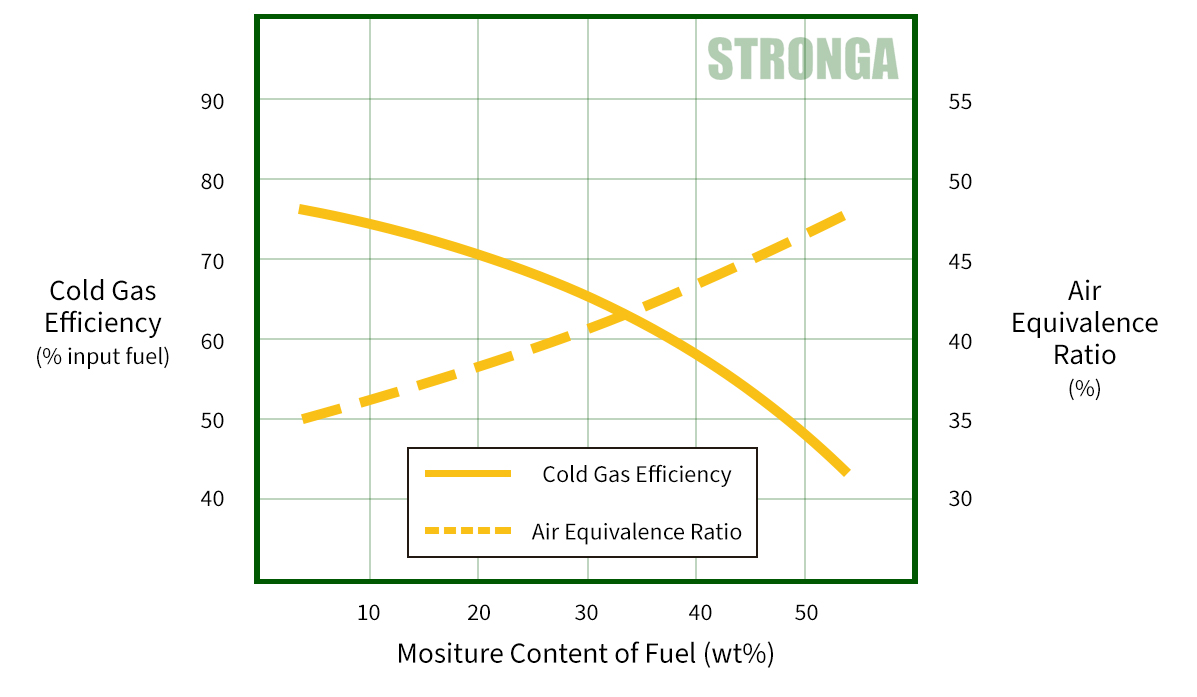
The Importance of Wood for Renewable Energy Production
Recent geo-political events have increased the importance of local, self-sufficient energy production. Importation, oil and gas fees are at an all-time high and, as a result, businesses are alleviating costs by investing in Stronga’s woodchip drying technology for local energy production. Norway can lead clean green programs for sustainable bio-energy production, increasing the stability of production, particularly for small-scale operations. Stronga’s drying systems actively contribute to renewable bio-fuels, enabling clients to produce a stable, dry, revenue-producing resource.
Renewable energy production is the future. In order to offset fossil fuel usage, drying by-products such as woodchip is an essential step towards a greener future. Our client didn’t want to miss out; get in touch with Stronga to discuss your potential contribution to renewable energy production and decarbonisation.
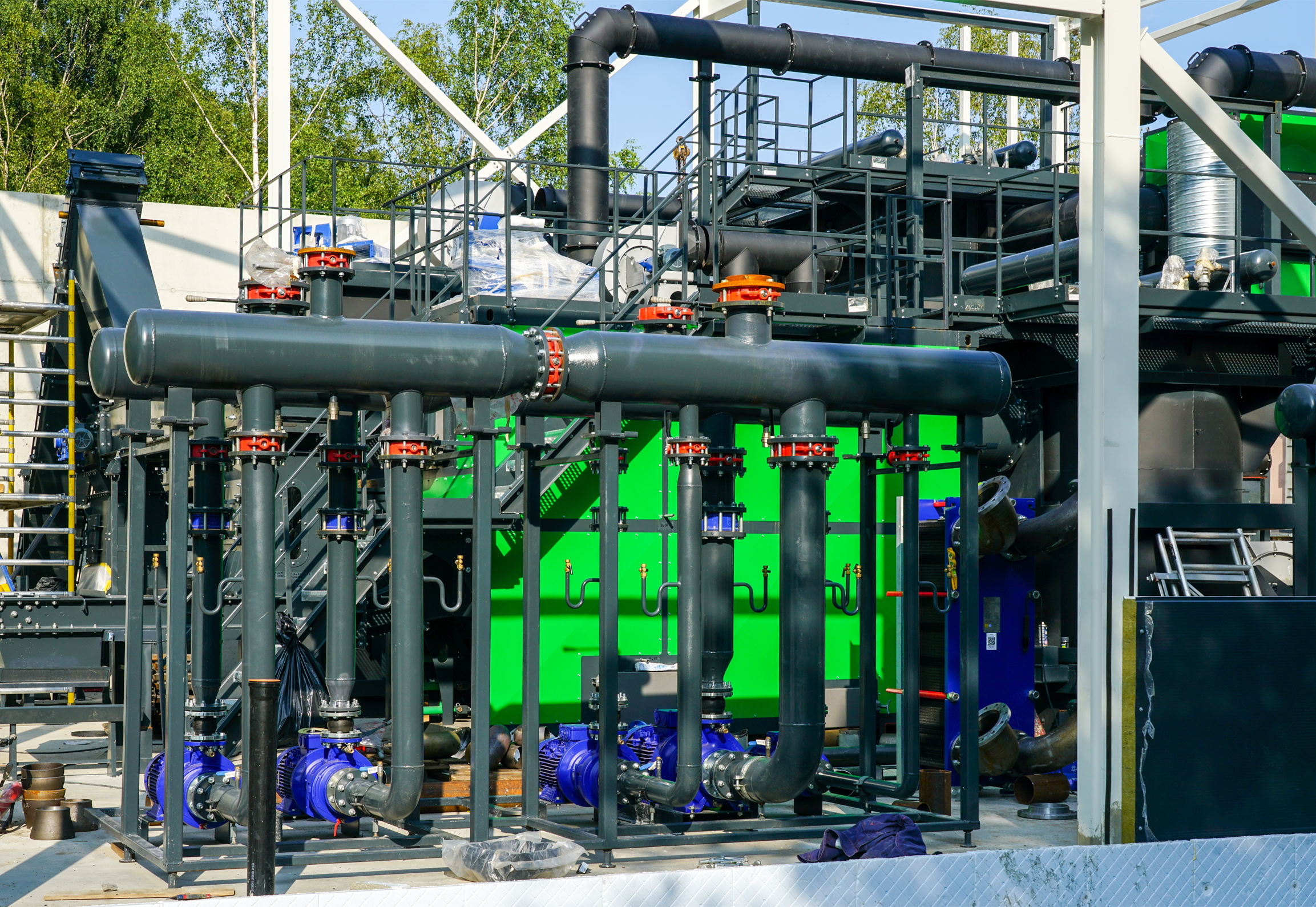
Create Your Own Renewable Income Stream
With a cold local climate, the demand for renewable energy production in Norway is particularly high, especially during winter months. Our client explained during our preliminary discussions that they wanted to produce consistently dry woodchip to distance themselves from the competition.
In this case, a suitable biomass boiler was already operating onsite for the wood kiln dryer and building heating, so no additional investment was required in the heat source for the suitably-sized Heatex unit. Businesses that have access to an abundant supply of valuable wood waste, together with on-site residual heat, have huge potential to create a renewable income stream with reduced waste.
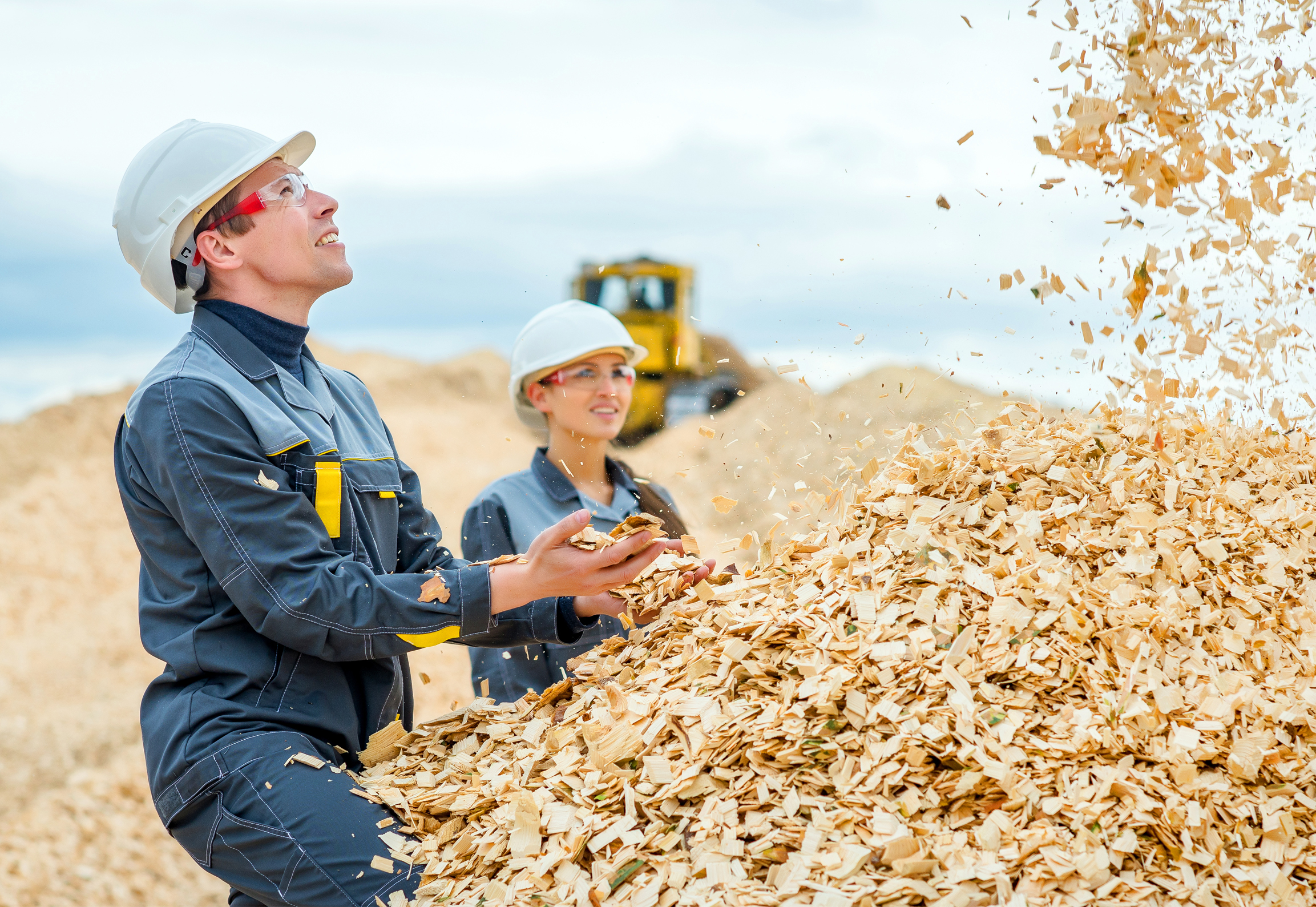
Optimised Efficiency with Stronga
During the consultation period, our client advised us that their biomass boiler had a thermal capacity of 450kWh which is split between their kiln and building heating. The woodchip container drying station would operate from the existing boiler infrastructure, avoiding the installation of another boiler while optimising their existing plant. Using spare heat from the boiler, Stronga’s woodchip Drying Station operates highly efficiently from an energy perspective, keeping costs to a minimum.
Our client was pleased with the ability to use existing energy heat source for drying, while filling, conveying and transportation costs were minimised using Stronga’s transportable Drying Station system.
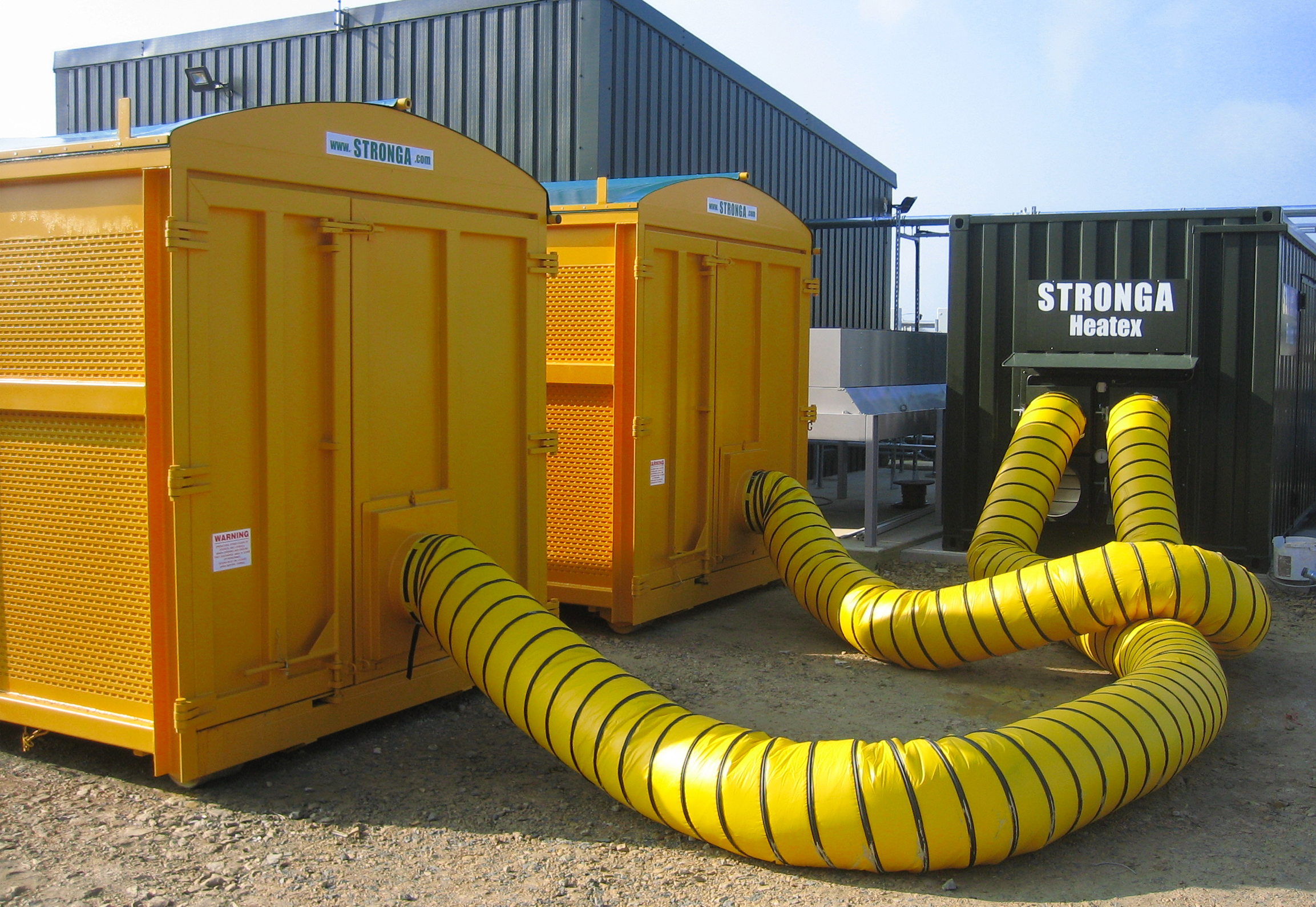
Stronga Horizontal Airflow Drying vs. Bottom-Up Drying
Stronga’s horizontal airflow drying containers are compatible with Heatex modules and HookLoada trailers which, together, create the complete Drying Station package. Clients are often intrigued by Stronga’s horizontal airflow drying (HAF) system which is circa 3X more effective than bottom-up drying containers, evaporating up to 1,500 more litres of water a day, per unit. This set up allows low density products, such as woodchip, to be dried consistently and uniformly. Discover some of the key benefits of Stronga’s container woodchip drying systems:
- Each HAF drying container features a central plenum with specially-designed air-balancing dampers to suit the material to be dried. These components are altered on a project and input material basis.
- Manage the whole project from start to finish; Collect, Dry and Deliver your dry woodchip with our three-part integrated system – Heatex, HAF container and HookLoada.
- Stronga’s batch drying containers have a high load capacity and thus can batch dry large quantities of woodchip, every single cycle.
- Stronga’s modular drying containers are equipped with high-grade polyurethane roll sheets which allow the client to batch dry each load outside.
- Slotted container sides reduce back pressure in the plenum whilst also ensuring dust emissions are minimised.
- Flexible ducting connecting the HAF drying container to the Heatex is fully insulated to minimise heat losses.
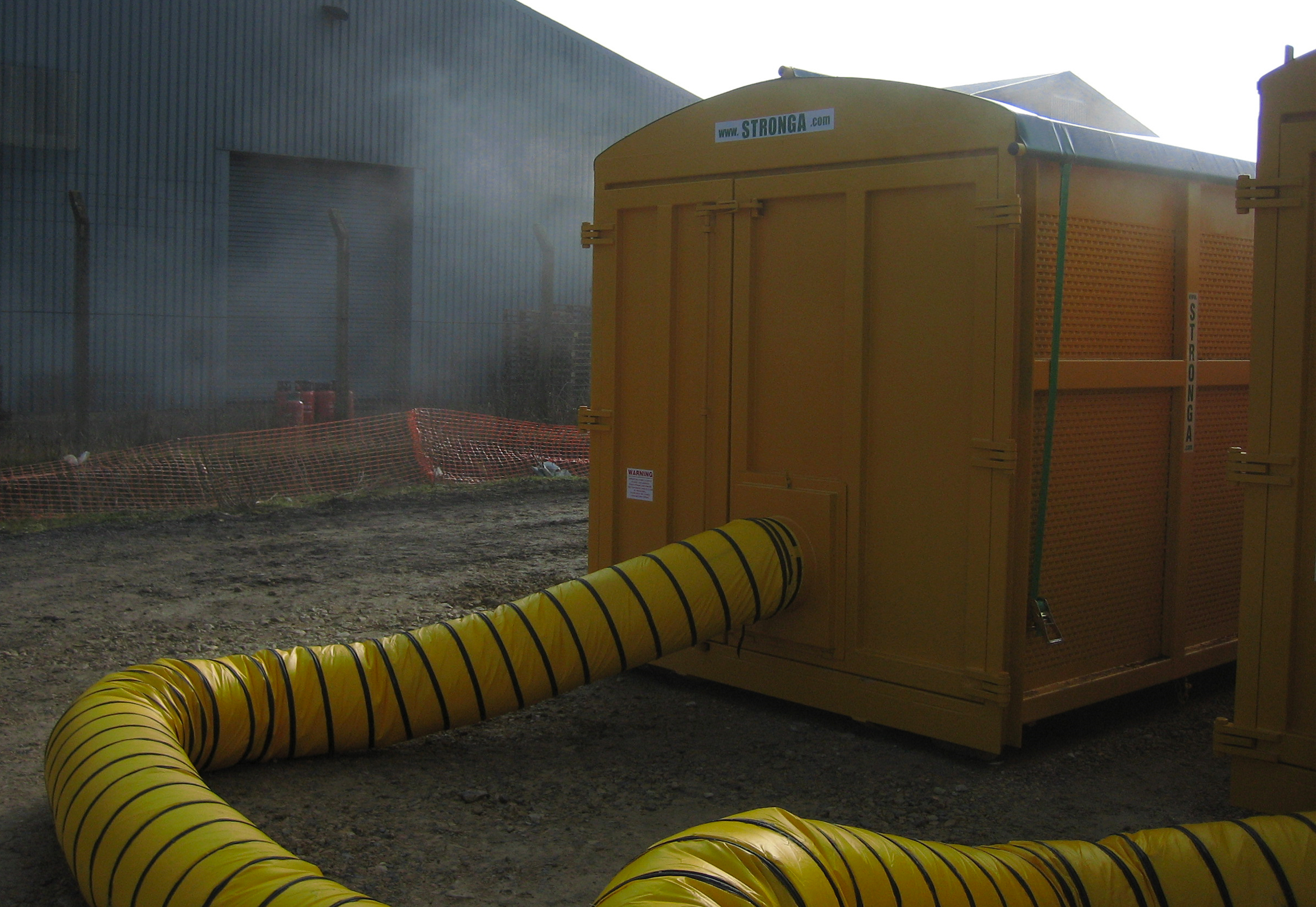
As explained above, Stronga Drying Stations offer a fantastic drying solution for small-scale batch-drying requirements. However, in many cases, and particularly for larger-scale operations, the FlowDrya continuous drying system offers the best solution in terms of drying efficiency, ease-of-operation and control of output moisture content. Collaborating with Stronga offers significant benefits for prospective clients as our team endeavour to provide you with the best all-round solution for your requirements.
Reduce carbon emissions and limit your waste today; we would be delighted to help – info@stronga.co.uk
Share this post