Journeying Towards Self-Reliance
Stronga engaged with a small-scale, forward-thinking family-owned farm who were attempting to achieve long-term self-sufficiency through utilising available waste resources. Having built an on-site anaerobic digestion (AD) plant, they are now on the journey towards self-reliance and renewable sustainability.
Using a feedstock comprising of chicken manure, farmyard manure and maize, the customer had the goal of creating a circular AD production process where they could benefit from the renewable energy created from AD biogas output, via cogeneration. To optimise the process, the customer also wanted to utilise the solid digestate fraction output and this is where Stronga collaborated with the client, providing the digestate dryer to allow them to use the solid fibre as a fertiliser, bio-fuel and cattle bedding. By using organic manure as an AD feedstock input, our client is significantly reducing their methane emissions, which is useful when applying for environmental grants. For their opportunities to be economic and environmentally viable, they needed to dry the digestate extracted from the anaerobic digestion process.
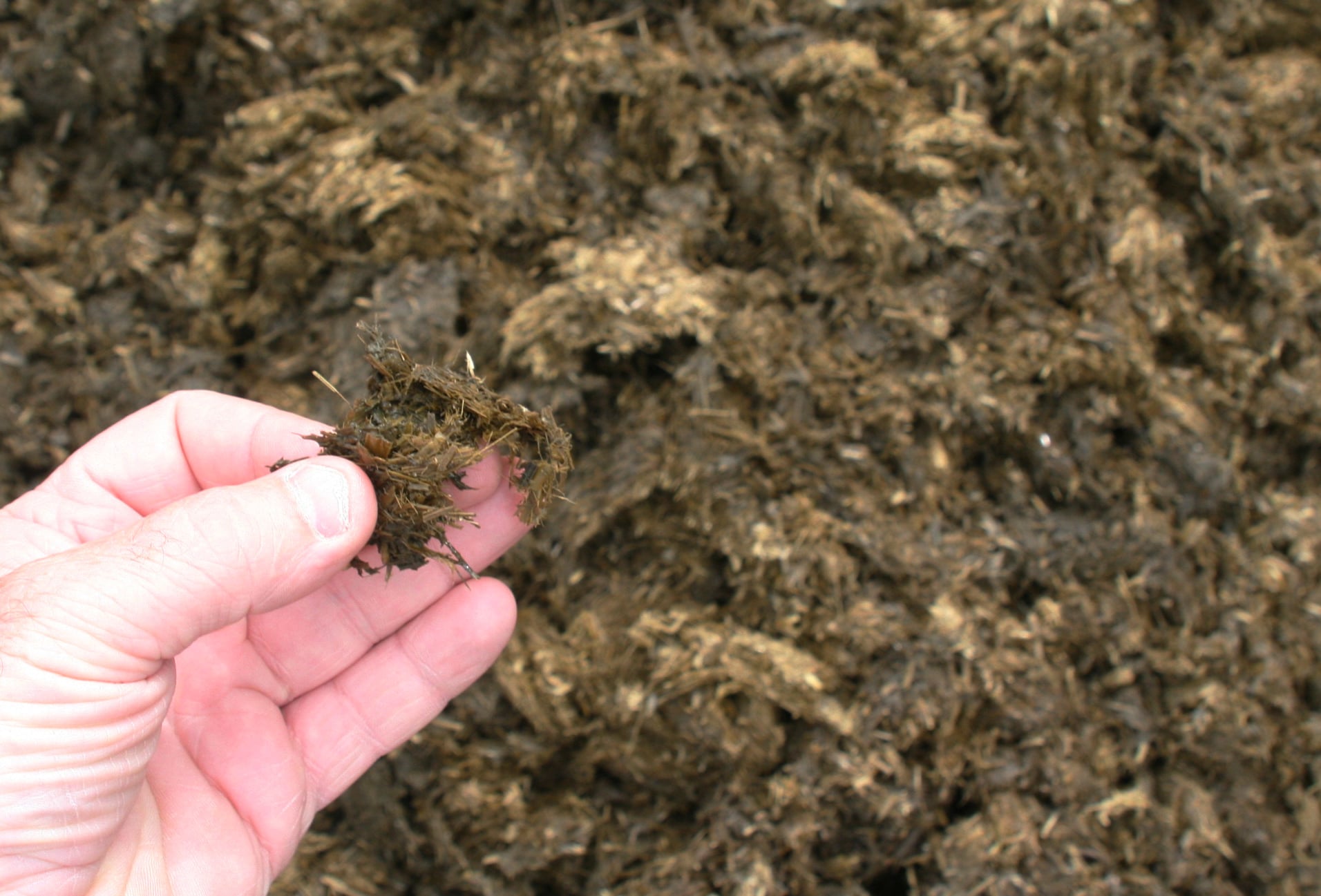
The Customer’s AD Process
The customer’s new process involves mixing livestock and poultry manure together and inputting the feedstock mix into the on-site anaerobic digester which produces two outputs 1) biogas, which they use for CHP, producing energy for on-site operations and heat for the dryer and 2) digestate fibre, which they use for animal bedding. Digestate is a rich organic material which is high in moisture and often sent to landfill, thus incurring costly tax, transport and gate fees. Drying the fibre adds significant value and utility to the resource.
The process involves separating the digestate and sending the liquor fraction back to the digester tanks, while the solid separated digestate fibre drops into the bunker where it is then loaded into the FlowDrya hopper. Once it has been dried down to the target moisture content in Stronga’s digestate dryer, it is available for storage and use – in this case as an animal bedding. However, it can also be used for landscaping, fertiliser, energy production and more, as shown in the graphic below. Notice how the heat from the biogas output is used in the dryer. Note – the graphic below shows various anaerobic digestion opportunities, together with a Stronga dryer. This customer’s specific process is highlighted by the yellow line.
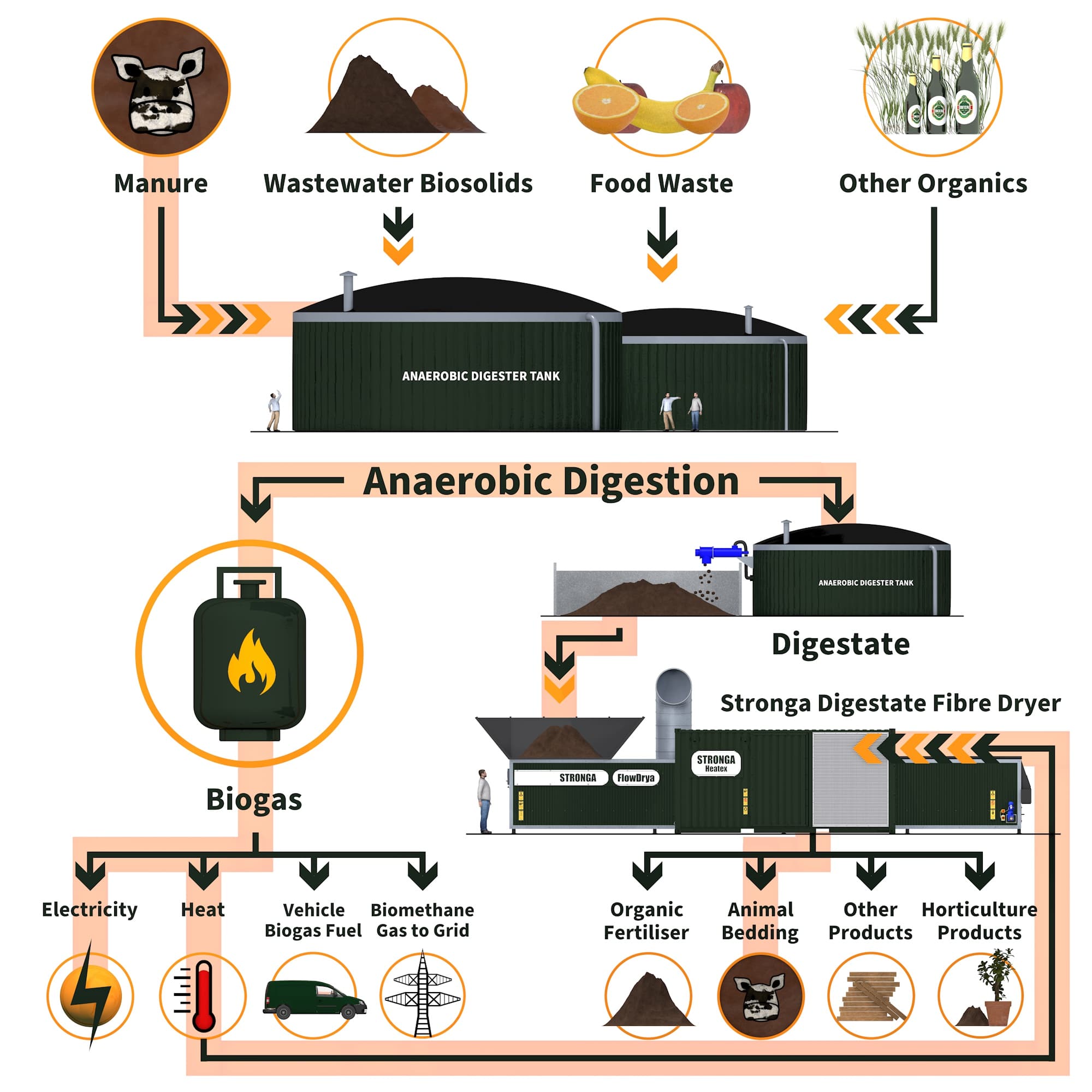
AD Fibre Animal Bedding – A Step into the Future?
Dried AD fibre animal bedding is produced from on-site waste and therefore forms part of a beneficial circular economy for farmers - reducing waste emissions and costly imports of virgin material whilst repurposing available material, over and over again.
Digestate slurry separation separates the water from the manure content and digestate fibre bedding is formed from the damp manure fibres component input for anaerobic digestion (digestate), ensuring all outputs are used. Drying the digestate fibre is essential for safe on-site utilisation and potential sale to the market. The customer had roughly 14 tonnes per day of wet fibre from the separator. Our team tested the material and found it contained roughly 66% moisture. The Stronga team scaled a FlowDrya to the requirements to ensure consistently dry digestate fibre output below 20% moisture content.
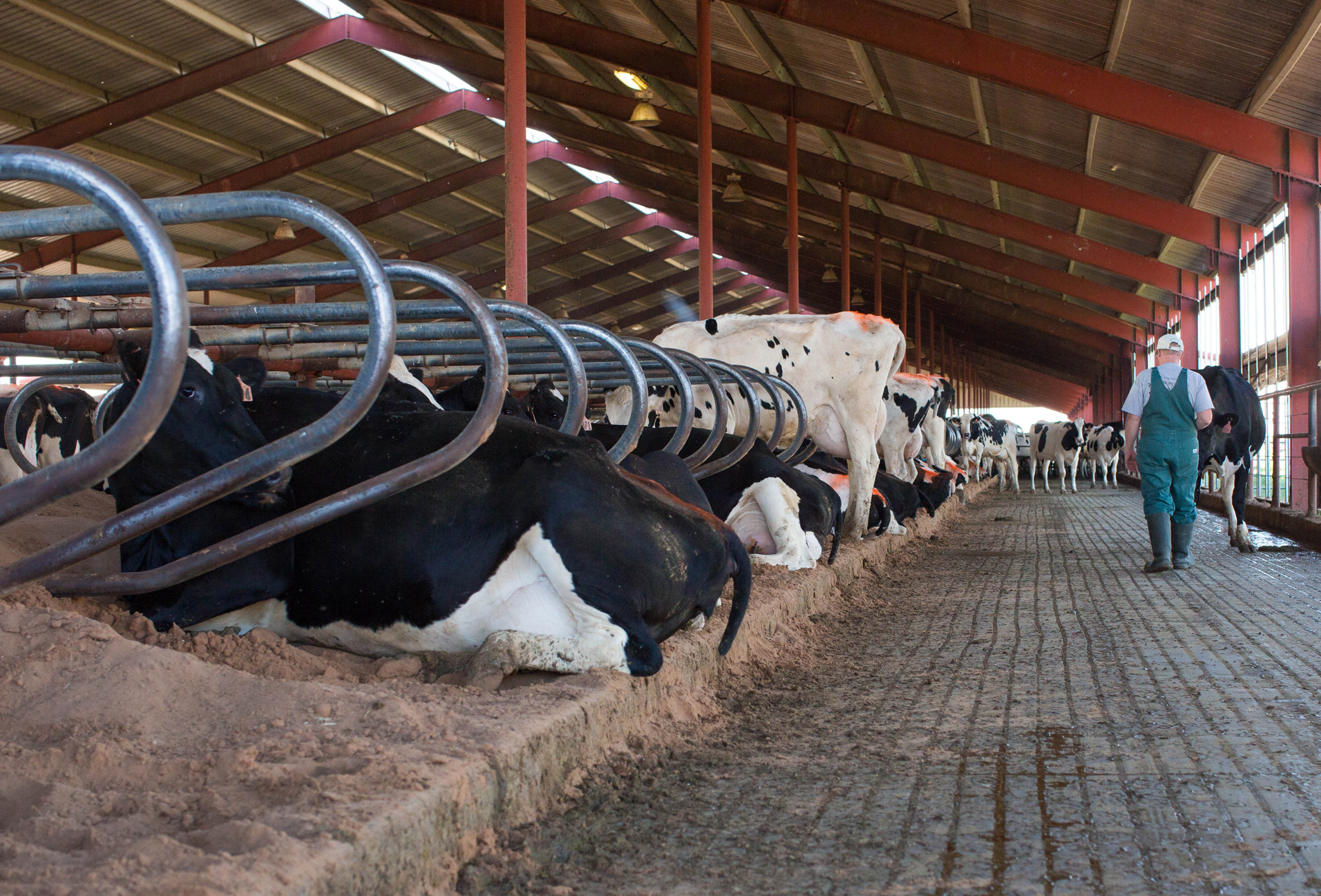
AD Fibre Bedding – Renewed & Reliable Value
Inflation and increased costs are encouraging farmers to act – repurposing digestate fibre which would otherwise be disposed of, into useful outputs. With the farm’s circular economy in mind, this particular customer devised a plan to create bedding for their animals to reduce wastage, disposal costs and purchasing while providing sustainability and financial security for future familial generations.
Once the bedding has been used, the customers put the waste back into the AD tank and re-dry it in the Stronga digestate dryer for use multiple times over. This fantastic process creates a closed-loop cycle with no external factors involved.
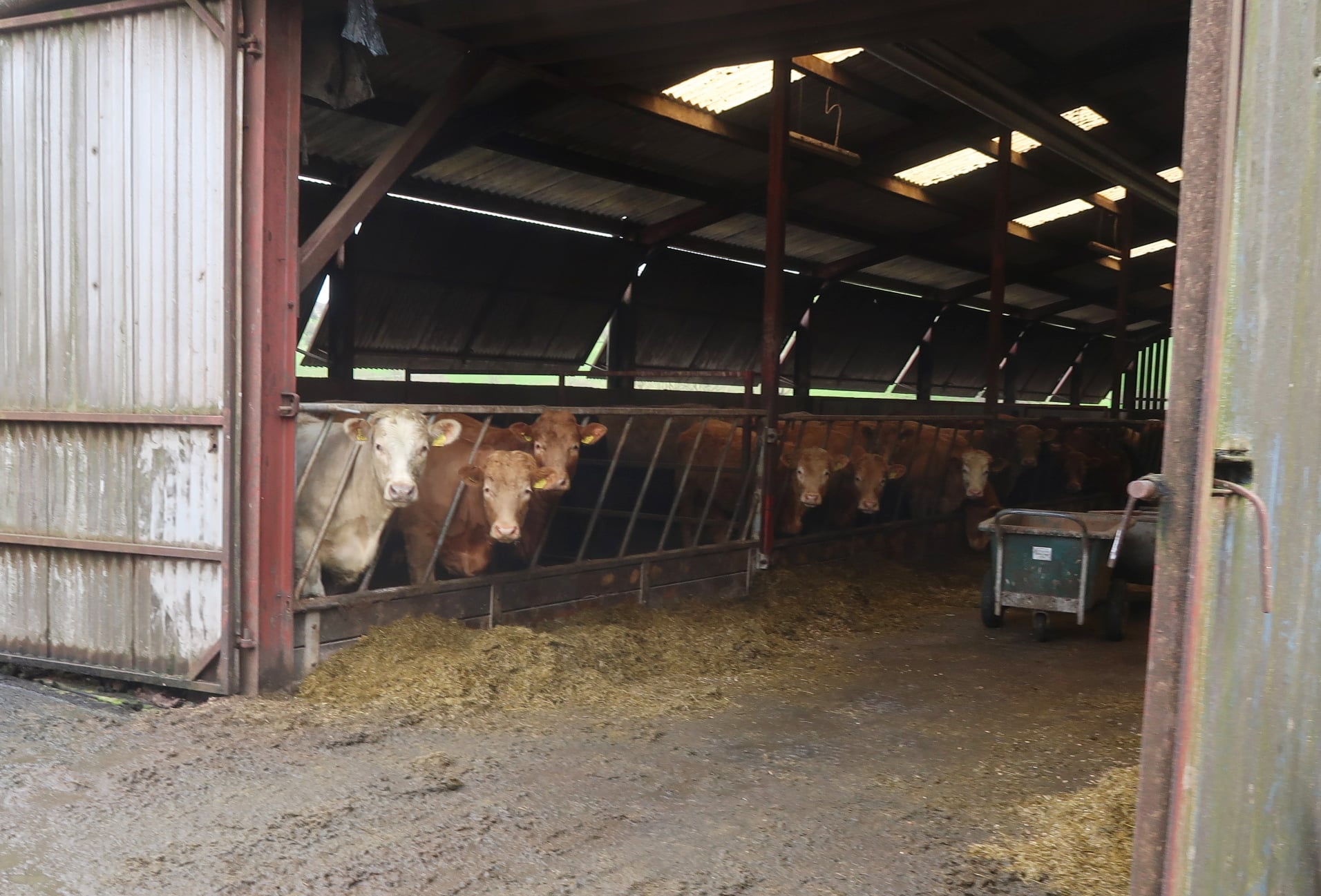
The Benefits of Dry AD Fibre Bedding
The benefits of dry digestate fibre bedding are substantial:
1. Dry digestate fibre is stabilised for long-term storage (low risk of moulding), making it a better asset and income stream if local area regulations allow the selling of animal by–products;
2. Dry digestate is available for use as an organic fertiliser post-bedding use; or alternatively, can be input back through the AD / drying process for re-use as animal bedding over and over again;
3. Dry digestate fibre bedding contributes towards better animal welfare;
4. Using dry digestate as animal bedding is more environmentally-friendly than importing in virgin material, each cycle.
5. Unlike sand, straw and sawdust beddings, AD fibre bedding is non-abrasive, absorbent (when dried before use), causes less caking and doesn’t get stuck in fleeces and fur, like sawdust does.
6. Drying digestate for animal bedding provides farms with a constant source of bedding which encourages liberal dispersion in cubicles.
7. AD fibre bedding is proven as the preferred choice among farmers and livestock, encouraging longer lying times and contributing to reduced respiratory issues often associated with sawdust or straw.
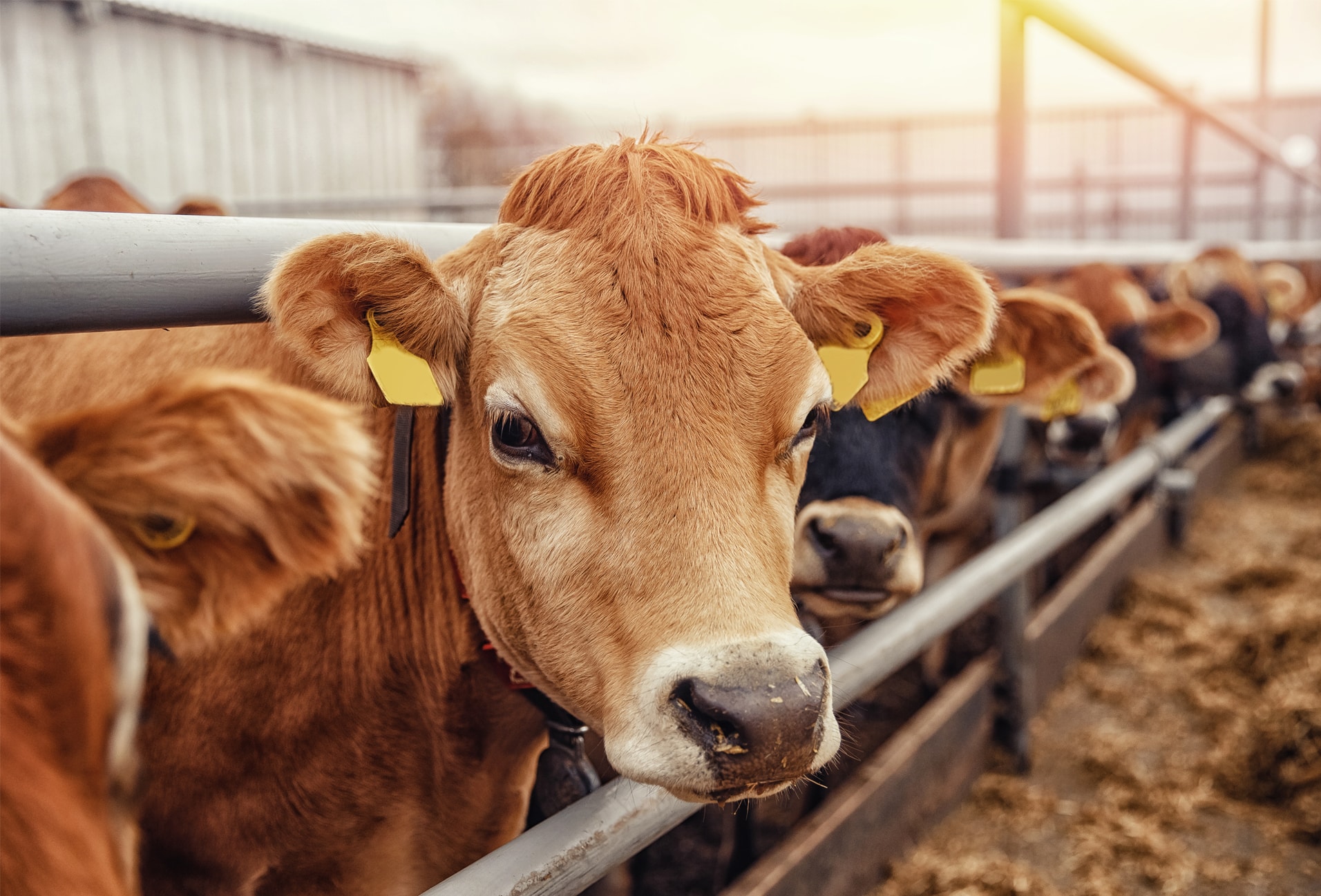
Success with Digestate Fibre Drying Technology
Through investing in digestate fibre drying technology, our customer has succeeded in making their AD plant as efficient as possible, creating a self-sustainable circular operation involving the biogas and solid digestate fibre outputs. With the help of FlowDrya, they have created a waste-free site, harnessing the power of residual energy and utilising available resources to their full potential - never having to import virgin animal bedding again. Drying bedding using FlowDrya equipment is an overall more sanitary option for farms, reducing atmospheric odour typically associated with wet manure bedding.
Note - there are regulations in place when dealing with animal by-products relating to moisture content, transportation and uses as bedding. These should be carefully considered before deciding to act.
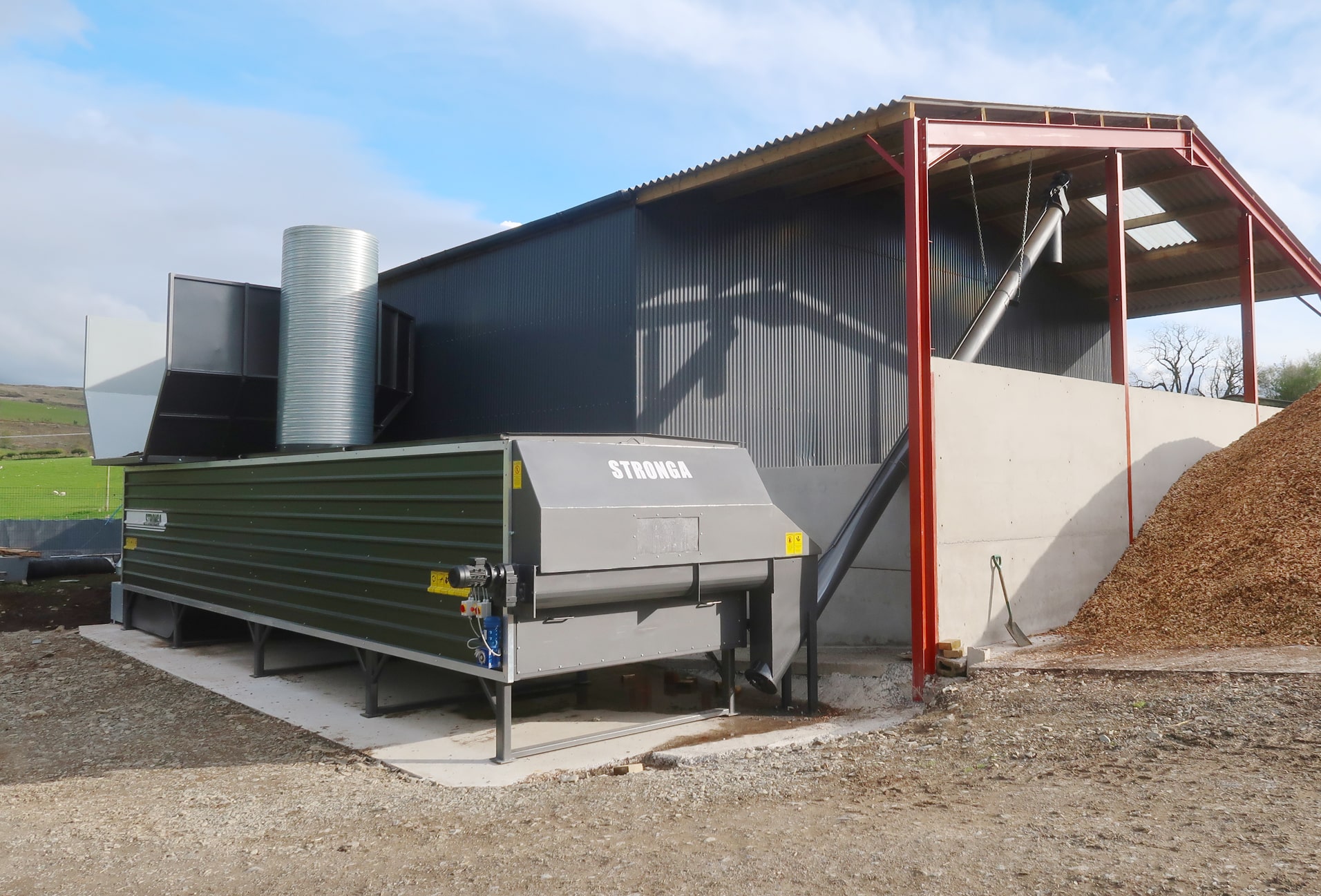
Digestate Fibre Drying Experts
Together with the customer, we established there was 200kWh spare heat available from the cogeneration plant for the digestate fibre drying process. Considering factors such as digestate properties, moisture content and more, the Stronga team scaled the FlowDrya for 200kWh residual energy availability, optimising the farm’s waste energy to provide useful AD fibre bedding for on-site cattle. Our team discovered that the digestate output already had a high temperature, meaning even less energy was required to dry the fibre in the FlowDrya.
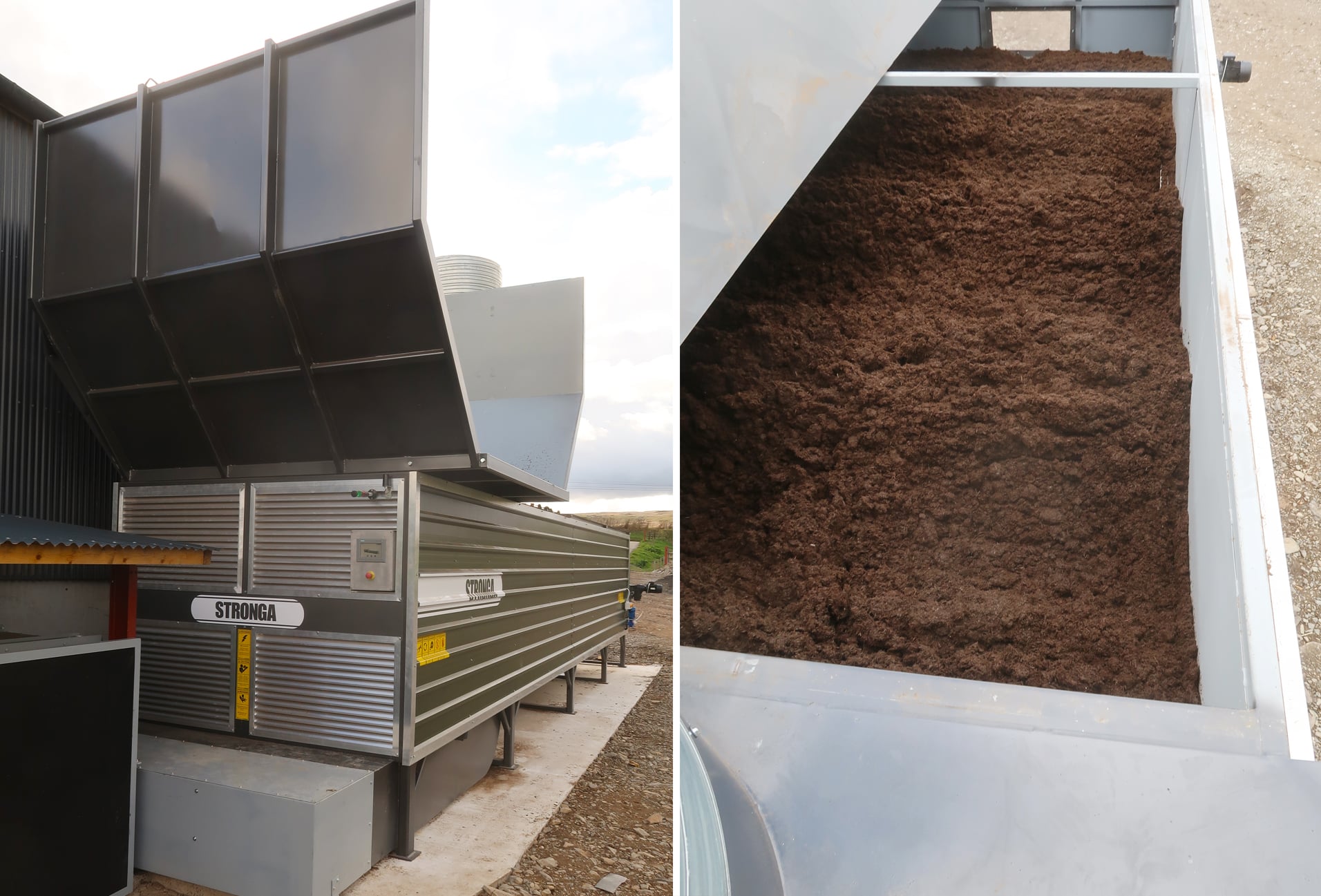
1st Choice for Drying Digestate Fibre
Stronga are pleased to report that our client is currently evaporating an average of 200 litres per hour of moisture from the digestate. In annual output terms, using FlowDrya, they are currently delivering approximately 1,600 tonnes per year of dry digestate which they are using as animal bedding onsite.
Discover the benefits of FlowDrya equipment for drying digestate:
- Stronga designs each FlowDrya with the customer’s requirements in mind. In this case, the digestate dryer was specially-adapted to suit the customer’s friable material which contained small lumps.
- FlowDrya has a ‘stop-start’ system. The machine ‘sleeps’ between strokes so despite the long operating hour capability; the digestate dryer is actually only ‘live’ for a short period of time so service and maintenance costs are greatly reduced.
- The hydraulic PulseWave™ agitation system ensures digestate fibre is naturally mixed and tumbled along the length of the FlowDrya drying bed.
- FlowDrya is fully insulated all-around, ensuring energy efficiency is optimised in line with the customer’s waste-averting approach to operations.
- The integrated DryStation™ HMI touchscreen allows for excellent operator control over the digestate drying process, delivering a consistently dry digestate fibre / bedding output.
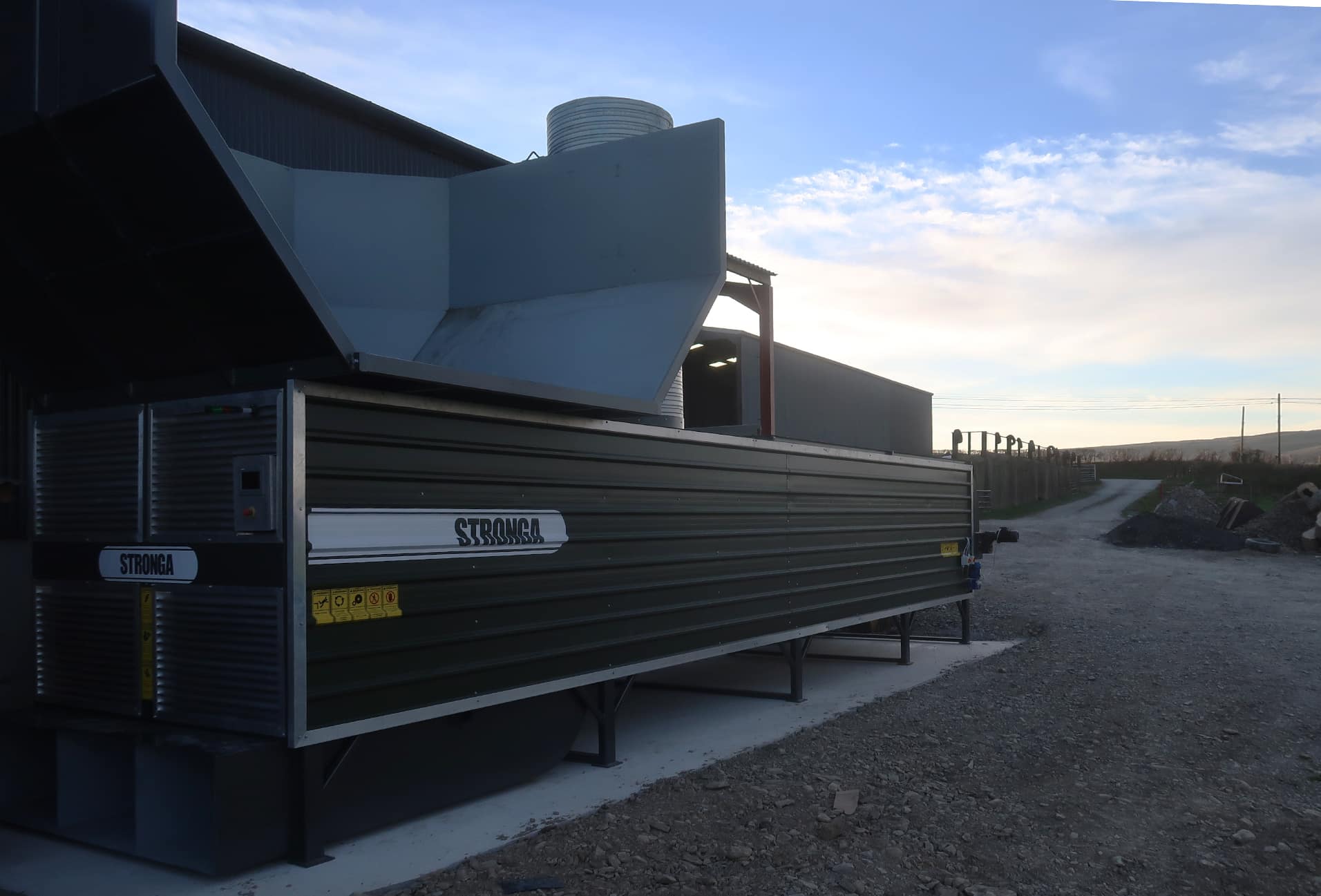
Stronga’s FlowDrya enabled this client to produce high quality digestate fibre animal bedding from dried, anaerobically-digested manure feedstock. You too can cut your costs and waste today; get in touch with Stronga to discuss our digestate fibre drying systems – info@stronga.co.uk
Share this post