A Story of Transition
After decades of owning and operating a sawmill and producing construction timber, it was time for change. This generational family-business saw a declining market in traditional sawmill operations and had a vision of a better future, using residual timber for energy production.
Realising there was very little value in wet woodchip, they had an idea. The customer, ‘Equidomus’, who are based in Czech Republic, detailed their plan to dry wood fuel for on-site electricity and heat production, with spare energy available for sale to the local community and the grid. Installing FlowDrya woodchip drying equipment on-site, Stronga played a small part in enabling them to reach their goal and create a successful energy project for future generations.
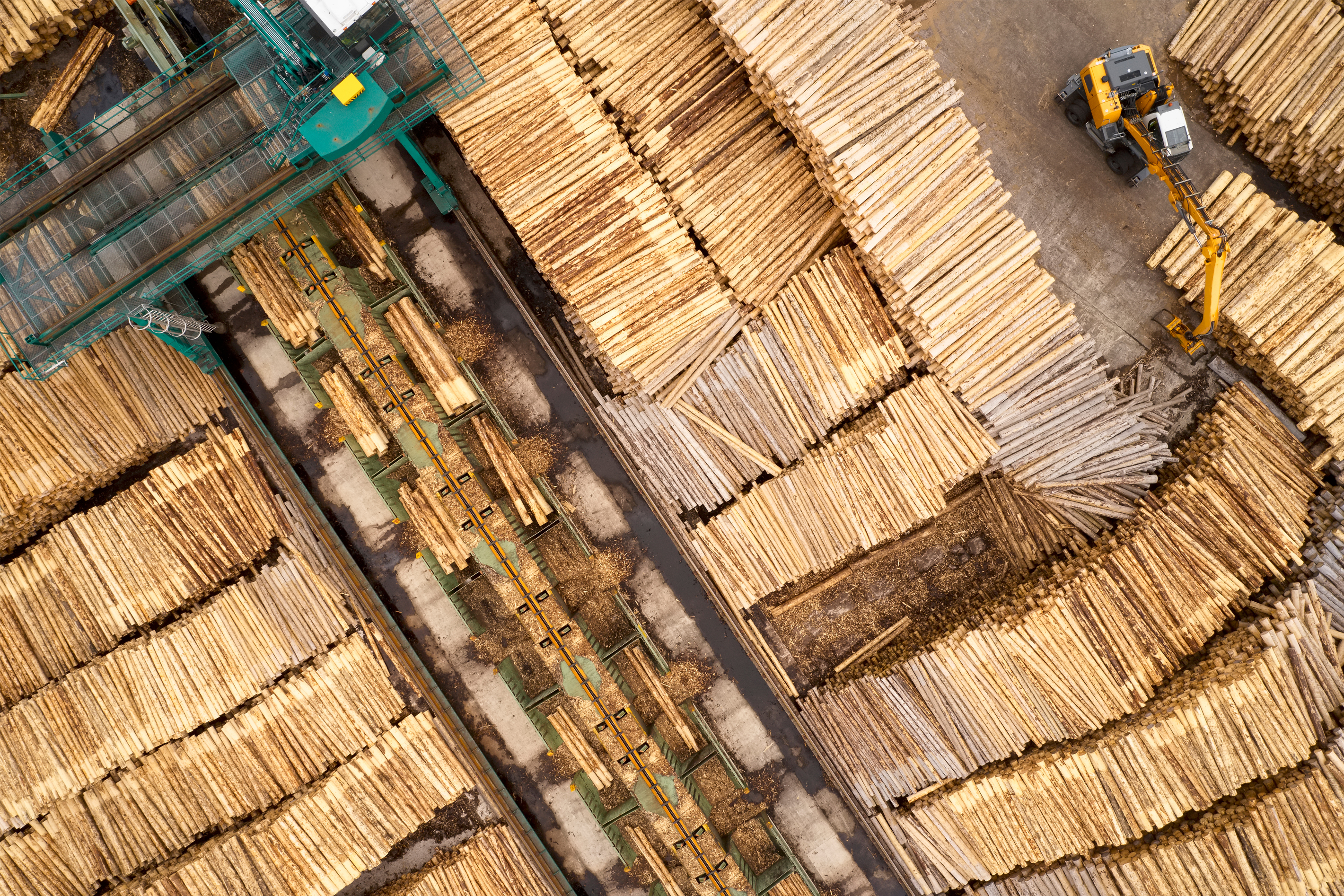
Gasification, Biochar & Wood-Gas – A Green Vision
During initial discussions with Equidomus, we understood the customer’s vision of powering their on-site equipment using greener, renewable, lower cost energy. Using locally-available energy for operations enabled Equidomus to benefit from energy efficiency with full control over production and consumption – whilst also qualifying for ‘sustainability’ financial grants.
Now, using FlowDrya equipment, the client can input consistently dry woodchip into the gasifier to produce syngas for heat and electricity. Drying woodchip for gasification enhances the calorific value of the syngas, making the drying process an essential step in the whole setup. The client's process is visualised below, excluding the biochar output which is not relevant in this particular case study.
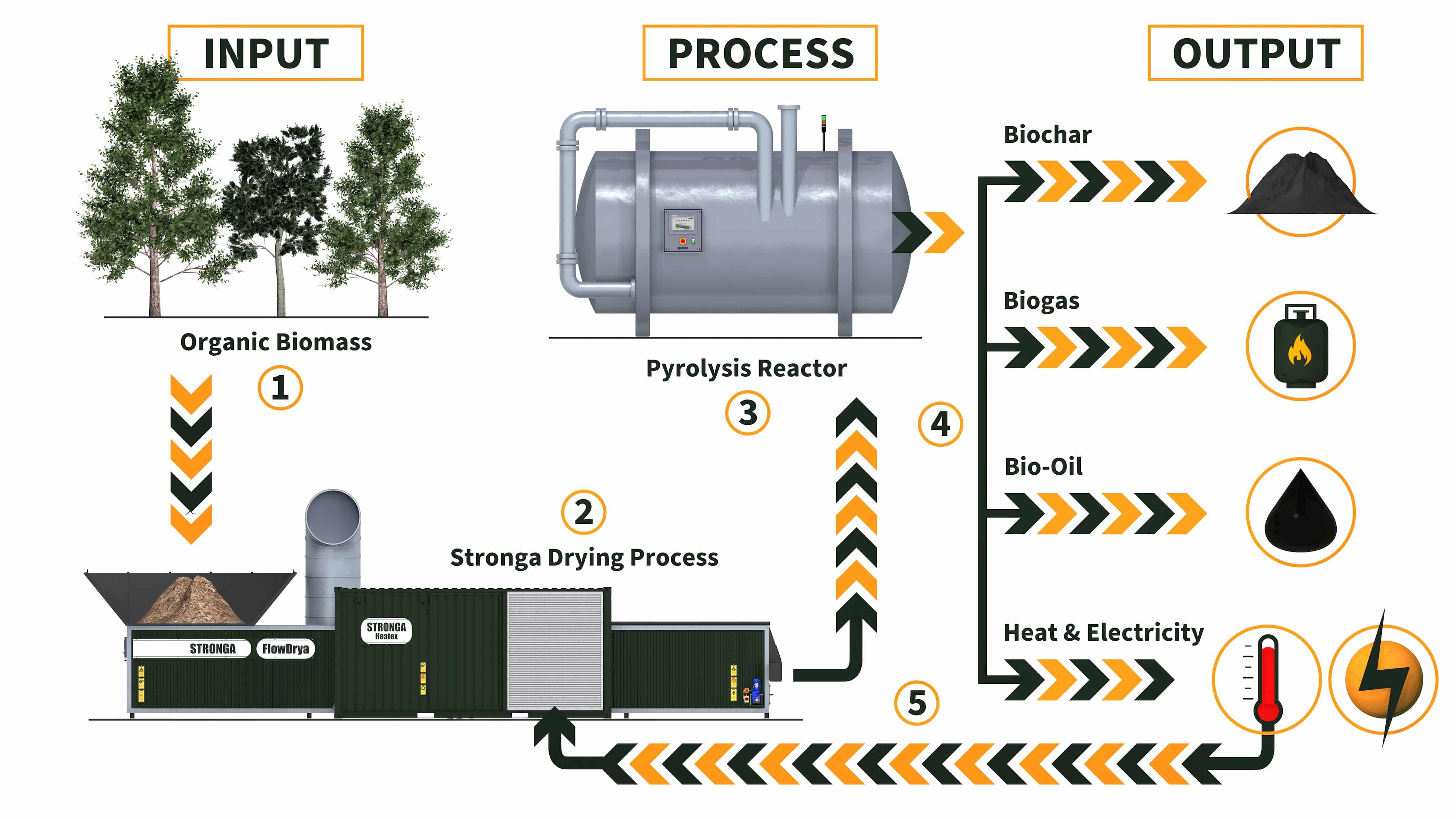
Discover the Benefits of Biochar
While Equidomus are not producing biochar from their gasification process, there is potential to produce this highly valuable resource. Discover the benefits of biochar below.
Biochar is a natural soil enhancer which can be used to enrich arid, unfertile soil. On top of its soil-enriching qualities, Biochar also acts as a carbon sink, capturing and sequestering atmospheric carbon to reduce the negative effects of greenhouse gases in relation to climate change. In situations where woody by-products are left to waste, they actually release greenhouse gas emissions. Investing in technology to produce biochar, like our Czech friends, combats emissions while capturing atmospheric carbon at the same time; a win-win situation.
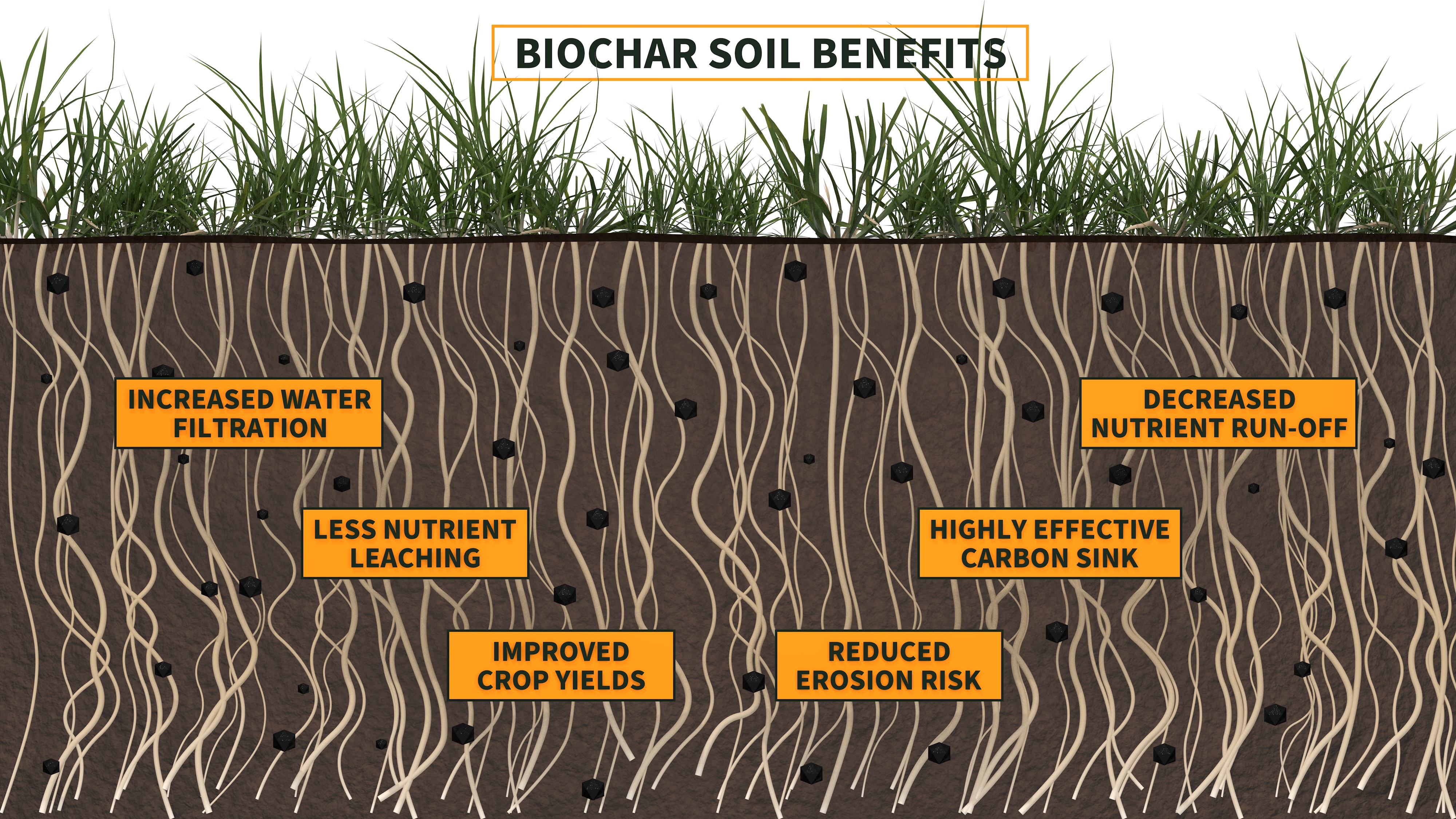
The Benefits of On-Site Energy Production
The other, even more beneficial output from gasification is heat and electricity which can be used to power on-site equipment and provide heating during colder months. Excess energy not consumed on-site locally can be sold to the community to provide a reliable supply of energy. Equidomus indicated that they wanted to dry sawdust down to 12% moisture content, and woodchips to 10%, drying spare woodchip to 20% for the local fuel markets. By entering the energy sector, our client became an energy producer and seller, reducing their own reliance on increasingly instable, expensive energy imports.
Our client wanted to convert their operations to a more sustainable approach when it came to utilising wet woodchip residue. They needed a dryer that fit their long-term approach to business.
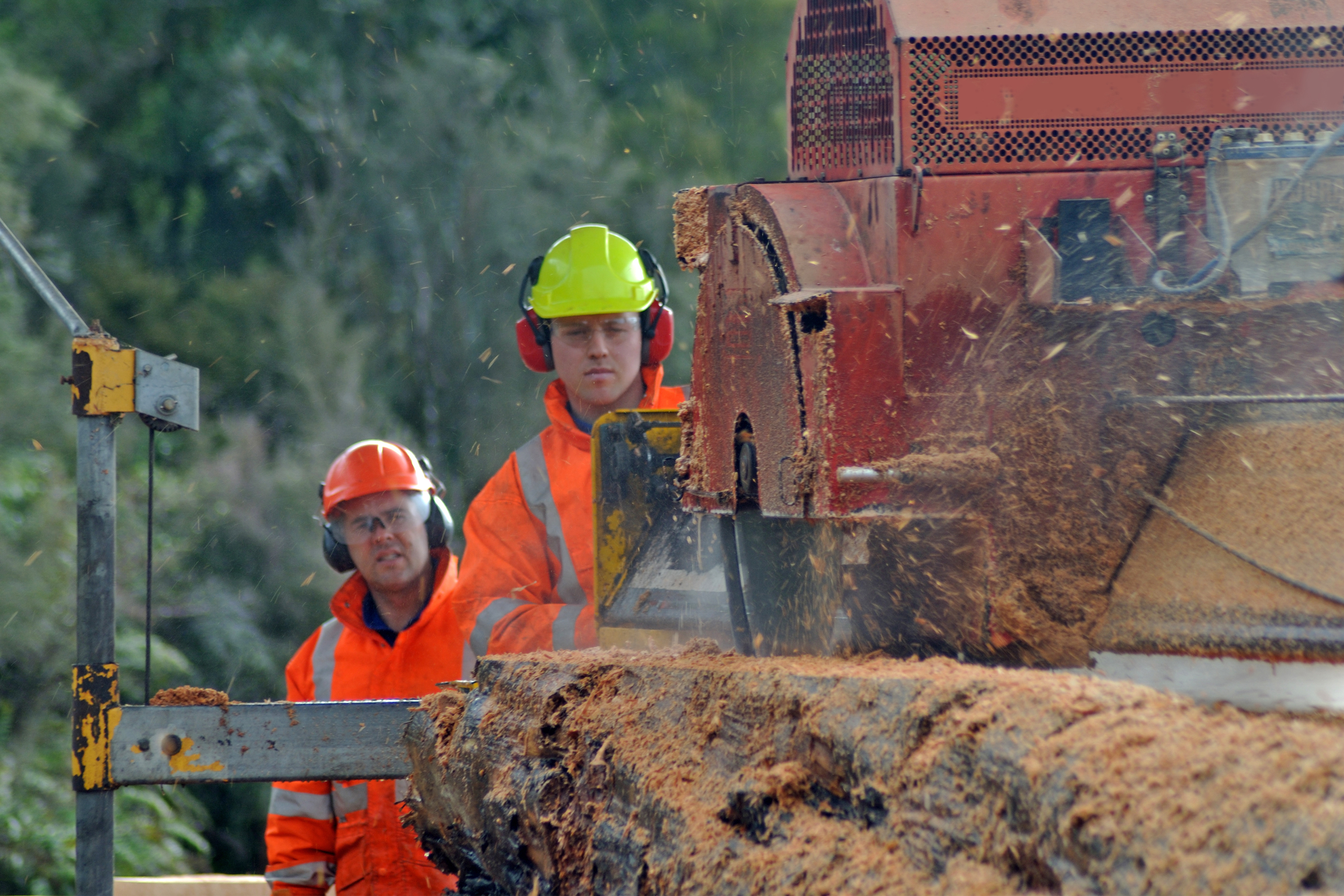
Effective Woodchip Drying Solutions from Stronga
Using a suitably-scaled, professional drying solution is key for optimum outcomes in wood gasification and energy production. If woodchip input is too wet, issues can occur, such as; operational faults in the gasification chamber, increased volatile organic compounds and the release of other harmful emissions. Typically, it is recommended that woodchip inputs have a moisture content of approximately 10% – this will reduce the energy losses spent drying the wood biomass during gasification.
Stronga’s FlowDrya equipment is built on a project-by-project basis to suit the moisture properties of the biomass. Moisture content can be constantly monitored in the dryer via optional, integrated moisture sensors. What’s more, settings on the DryStation™ HMI touchscreen can be adjusted accordingly, by the operator, to meet the desired output moisture content.
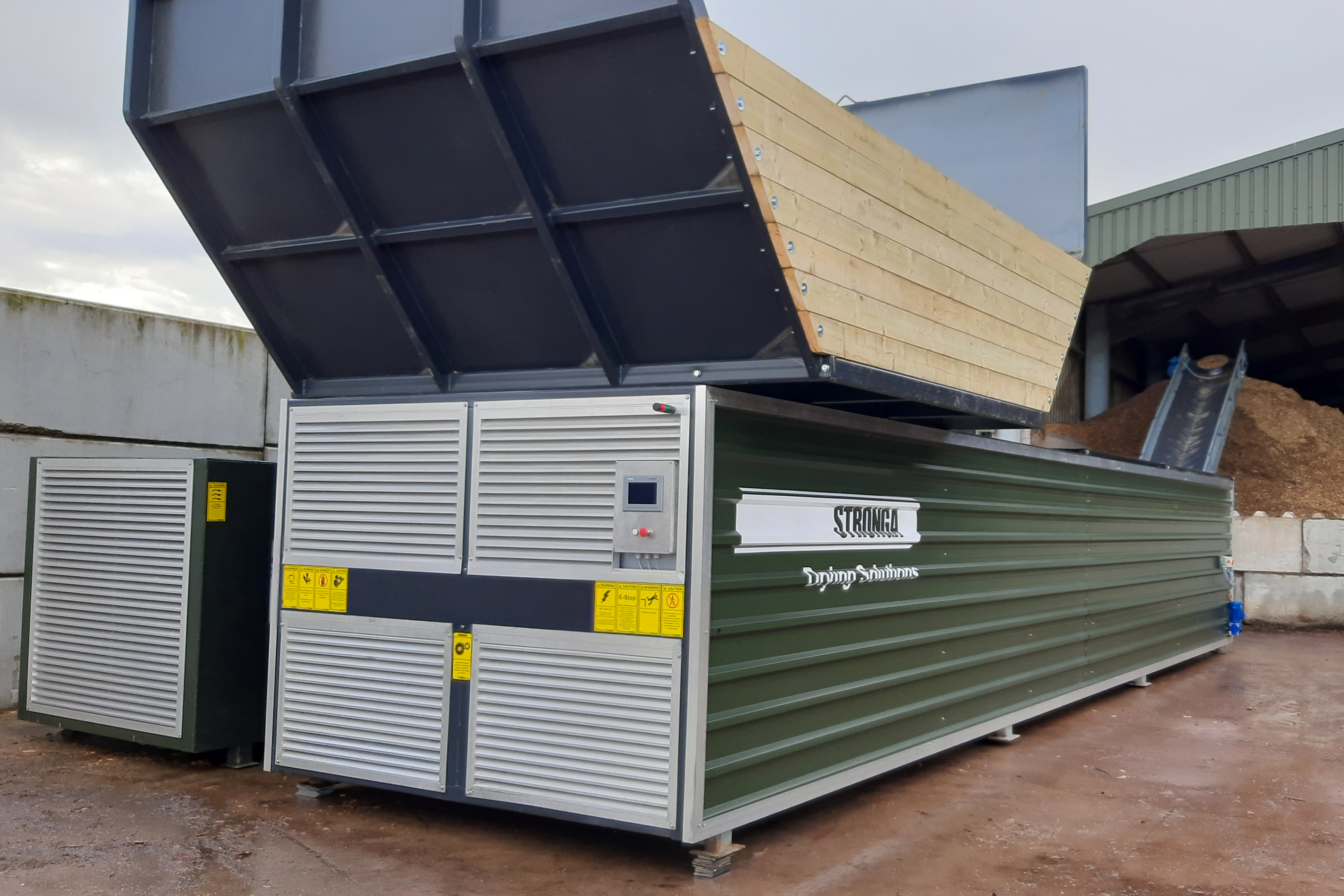
Equidomus strive for perfection and premium-quality in their timber product business. On-site, they operate long-life, premium-level technology from leading brands. They approached Stronga in search of equally reliable, robust and long-life woodchip drying equipment which could be designed to suit their individual requirements. Our team liaise closely with the customer during the sales process in order to fully understand the requirements of the business. In this case, our team designed and built a continuous flow woodchip dryer with a 30m² drying floor, extension hopper, rear discharge auger and more – to meet the client’s requirements. The project has been a huge successful, with Equidomus consistently delivering uniformly dried woodchips which are the perfect profile for their wood gasifier.
At Stronga, we only engage with projects where we can appropriately fit requirements and add sustainable value. The Equidomus project offered the perfect match.
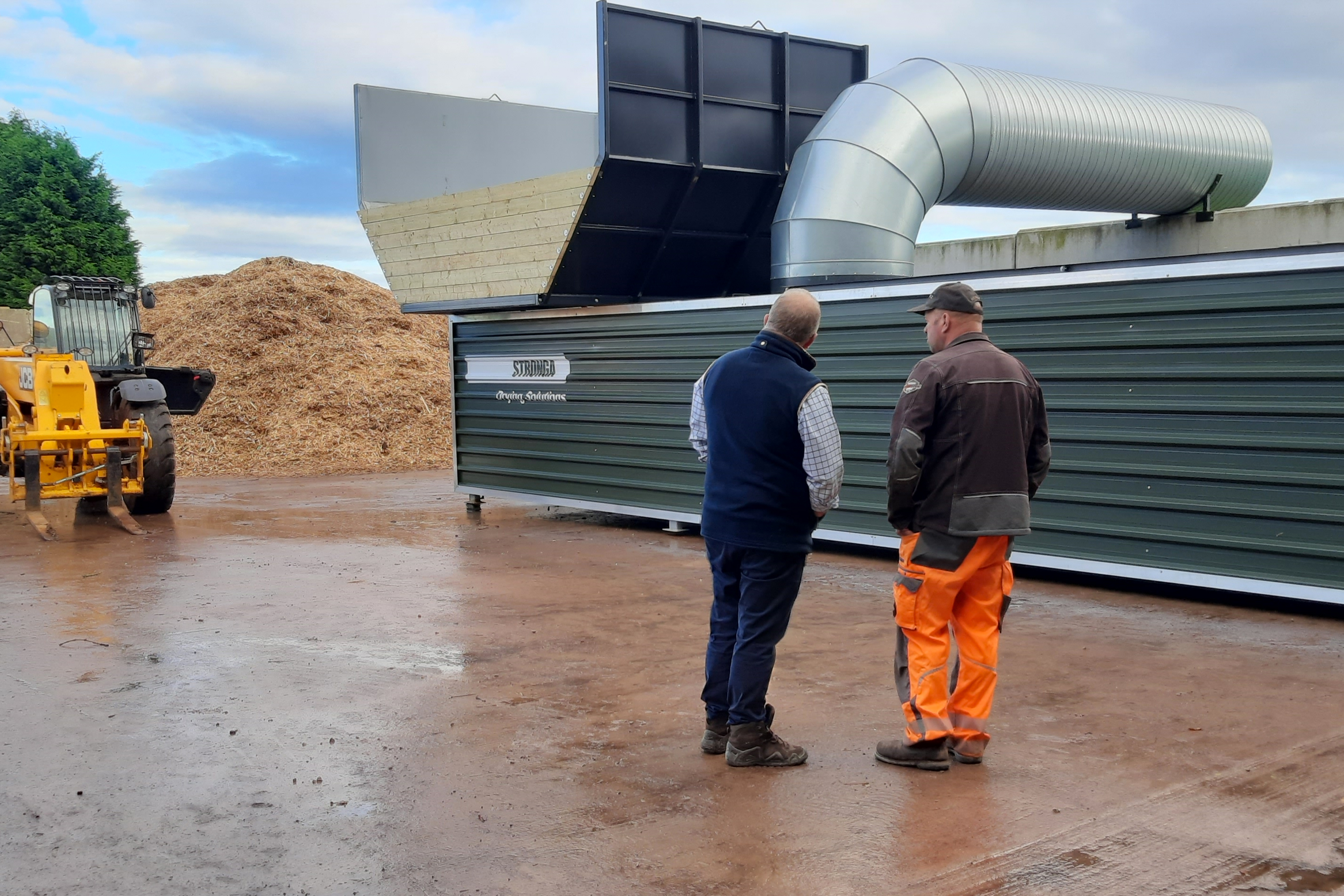
Circular Renewable Energy & On-Site Productivity
FlowDrya and Heatex are configured to accept residual heat energy from GenSets, biomass boilers and kilns – the latter of which many sawmills have on-site to dry logs. Using residual thermal energy from kilns in the Heatex allows the client to be fully energy-efficient, applying waste heat towards the useful process of drying woodchips. Alternatively, spare energy from wood gasifiers can also be used to dry woodchip fuel whilst also powering other on-site equipment.
Equidomus explained the level of residual heat delivered from their existing heat engines and we designed the Heatex and FlowDrya according to these specifications, ensuring the woodchip dryer would fully utilise the energy available. FlowDrya is insulated all-around to minimise energy losses during the drying process. Airflow injection from the Heatex together with the FlowDrya’s PulseWave™ agitation system ensure the output is thoroughly and uniformly dried to the required profile for gasification.
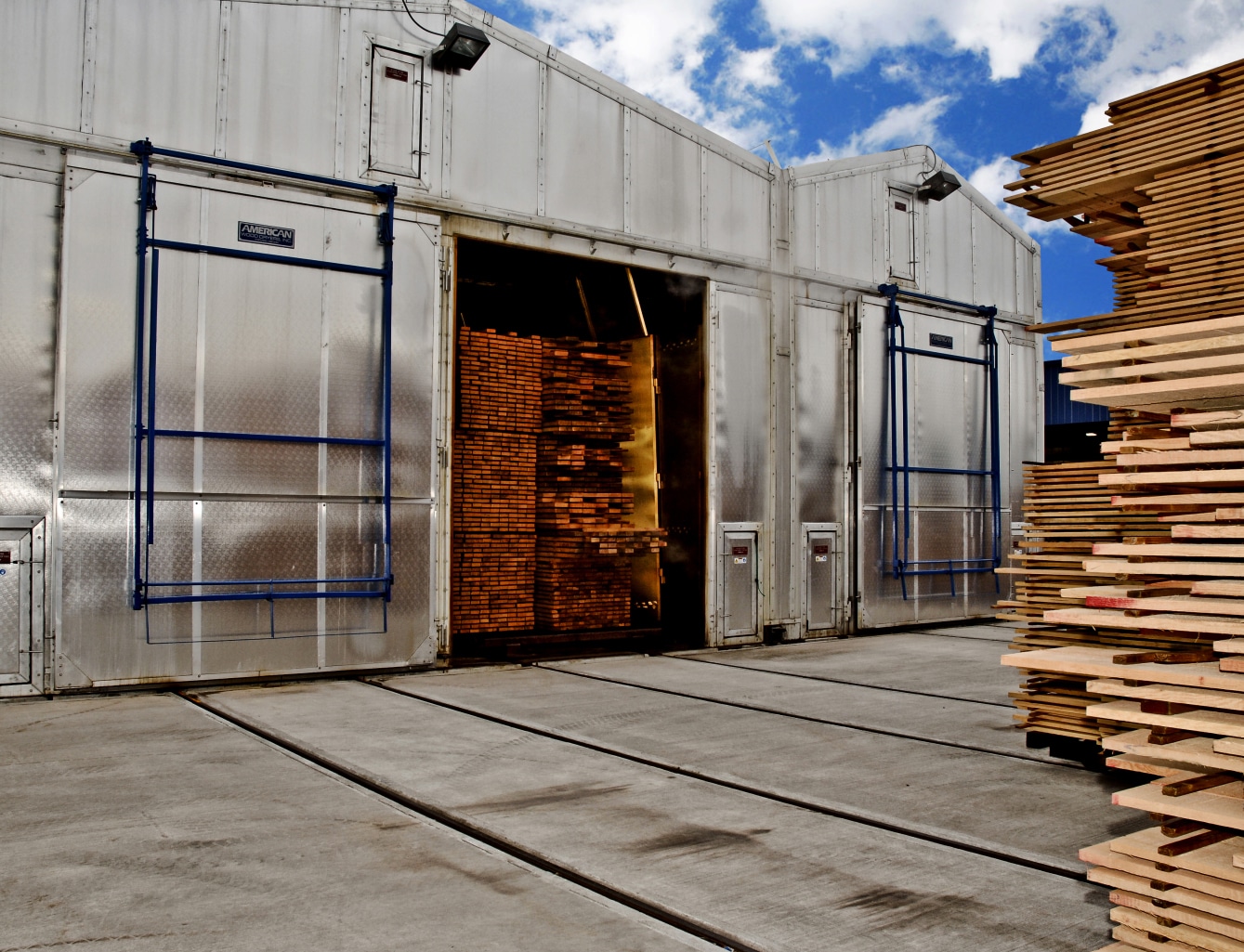
Smarter & Stronga
- Stronga’s FlowDrya woodchip dryer is designed according to properties of the material to be dried, residual energy available, local climate and more. Our team collaborate with the customer to ensure the dryer is optimised for the desired outcomes.
- The DryStation™ HMI control screen allows the operator to modify parameters to achieve the desired output moisture content. The live data logging function records key parameters for up to a year.
- The hydraulic moving floor PulseWave™ agitation system ensures output material is uniformly dried.
- The optional extension hopper allows the client to load huge quantities of woodchip into the dryer, reducing frequency of loading cycles while minimising labour costs.
- Our experienced team install and commission the modular drying system (see below) before taking the designated operator(s) through comprehensive training. Your team will feel confident operating our simple but effective woodchip drying system.
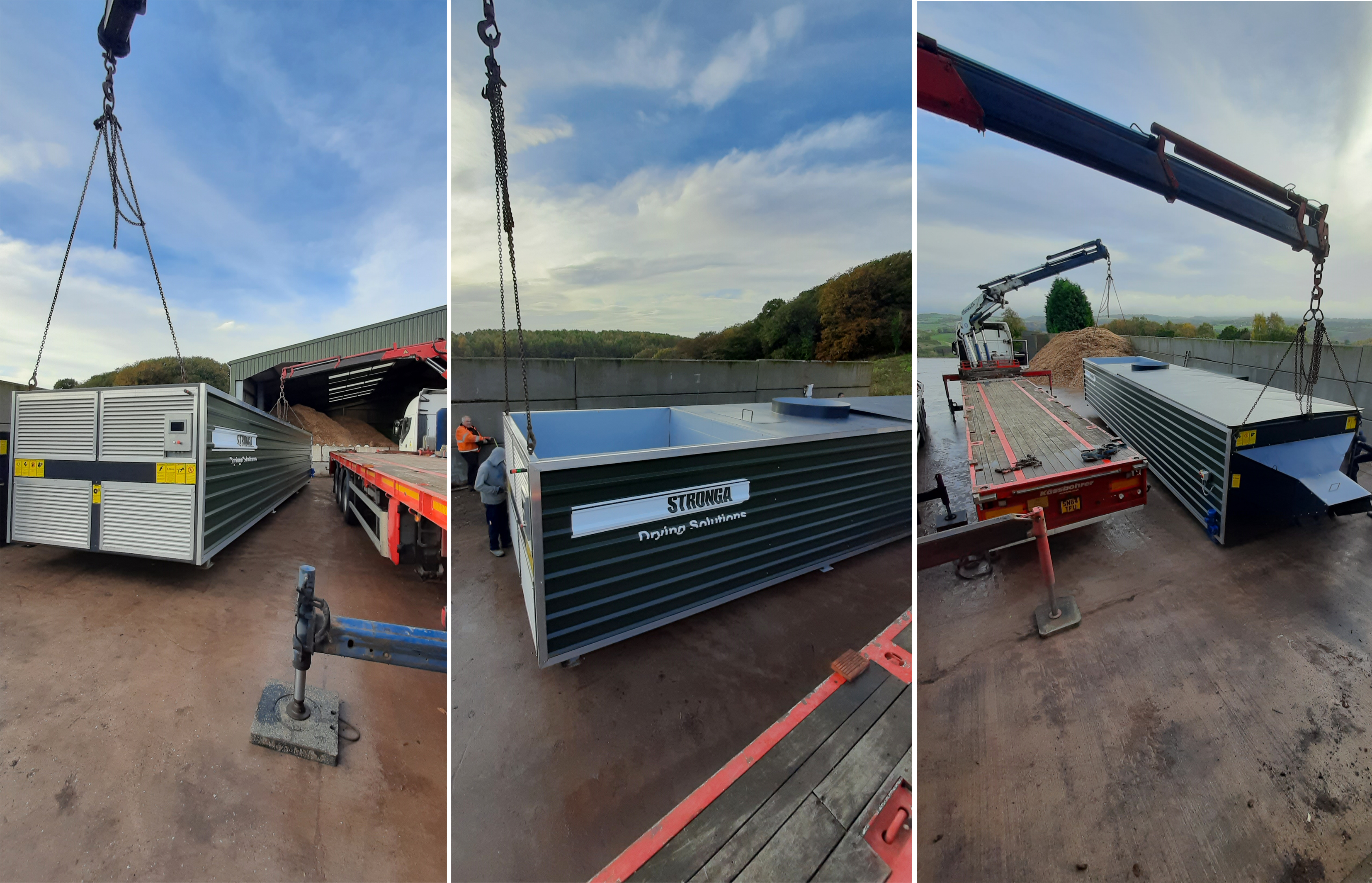
- FlowDrya’s stop-start system means that, whilst the dryer can operate for up to 8,000 hours a year, it is actually only “live” for a fraction of the time, reducing energy consumption while minimising maintenance costs.
- The independent Heatex unit, which features energy-efficient plug fans in modular housing, is an essential part of the woodchip drying solution, allowing residual energy from gasification to be re-purposed for drying woodchips.
- FlowDrya was developed with longevity in mind to reduce operational and maintenance costs for our customers. There are no belts, chains or sprockets which are common in other drying systems. The simple but effective design of FlowDrya extends operational longevity while reducing downtime.
Investing in FlowDrya and Heatex equipment allowed this particular Czech sawmill to gain significant value and utility from their spare wood, drying woodchips that would otherwise be wasted and producing ‘green’ energy. Add value to your resource – contact our team today to get bespoke advice on your project - info@stronga.co.uk
Share this post