This article presents the technical differences in design and cost between three alternative methods of drying wet biomass materials; (1) Stronga’s FlowDrya solution, (2) Belt dryers and (3) On-floor drying systems. Costs in this article are considered in terms of initial capital investment and ongoing operating expenses, which include energy, service and maintenance expenditure. Other vital features are compared such as dryer footprint, material agitation, labour requirement, fire risk and control systems. Drying biomass requires energy which is an increasingly expensive commodity; choosing the correct dryer is a critical decision which can make or break the profitability of your business.
Read on to learn more about each type of biomass dryer and make an informed decision about the most suitable option for your business, to enhance your resource management processes.
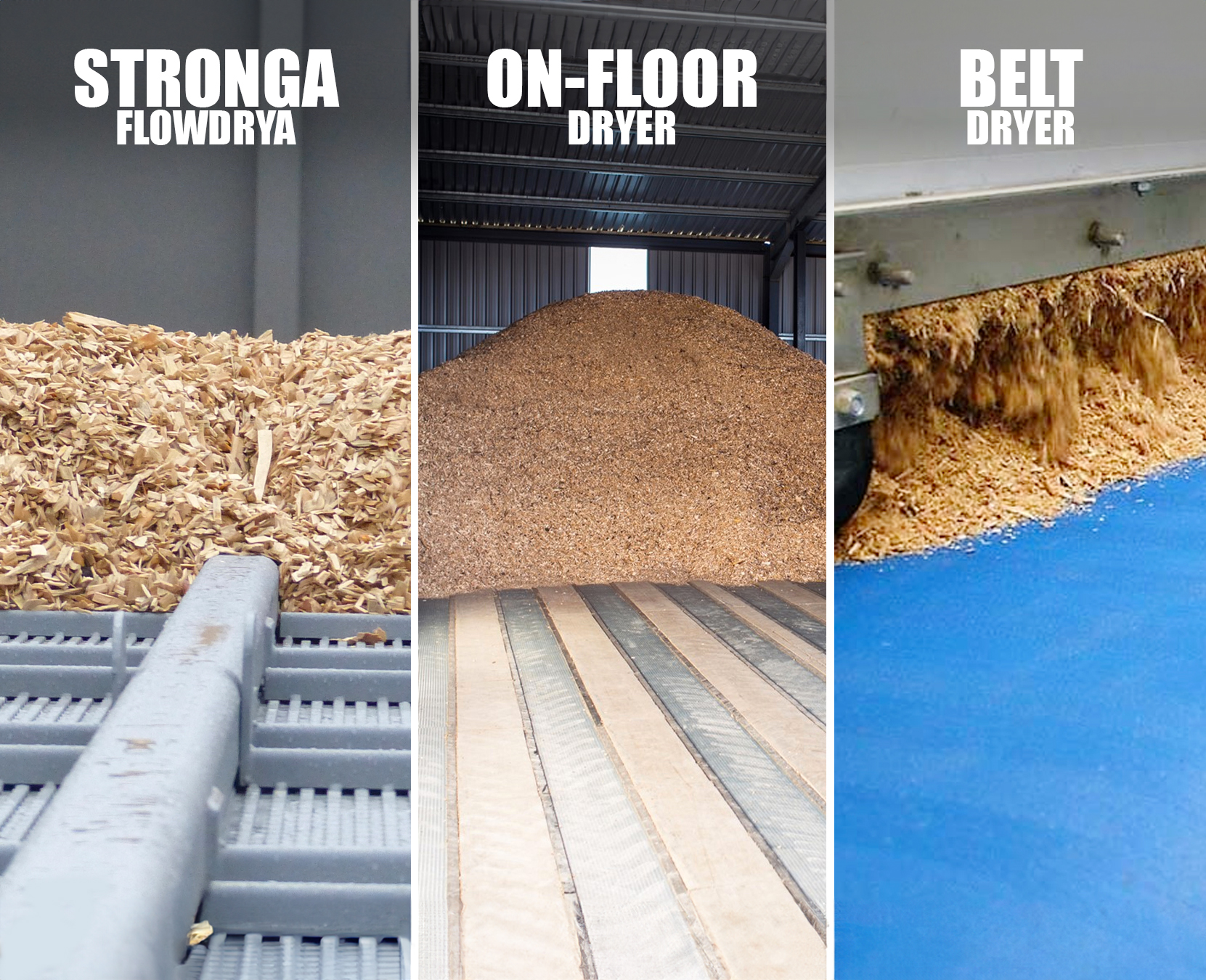
Comparing Design Complexity
Having a dryer with a simple design is essential for a smooth-running and productive operation. Complicated dryers with a number of moving parts are more susceptible to operational challenges; repairs are costly and consume valuable time. We believe clients should avoid these potential issues at all costs.
FlowDrya: Simple and strong with a sophisticated but uncomplicated structural design, few moving parts and straightforward operation using a powerful hydraulic power-pack. FlowDrya offers the most simple, long life, low maintenance drying solution available on the market.
Belt Dryers: A typical belt dryer design is highly complex with up to 54 bearings and 8 motors/gearboxes which all wear out over time and have the potential to catch fire if not thoroughly and adequately maintained. The belt itself is also a fragile, expensive-to-replace component, with a complex in-feed arrangement to match; the ability to spread material evenly, along the bed is much more complicated than the FlowDrya system.
On-Floor Dryers: Whilst on-floor drying might appear simple on the surface, these dryers are highly inefficient in several ways. The appearance belies the air-flow complexity beneath the floor which is required to distribute air consistently across a large area. Operationally complex, most grain on-floor dryers are inadequate for moisture heavy biomass.
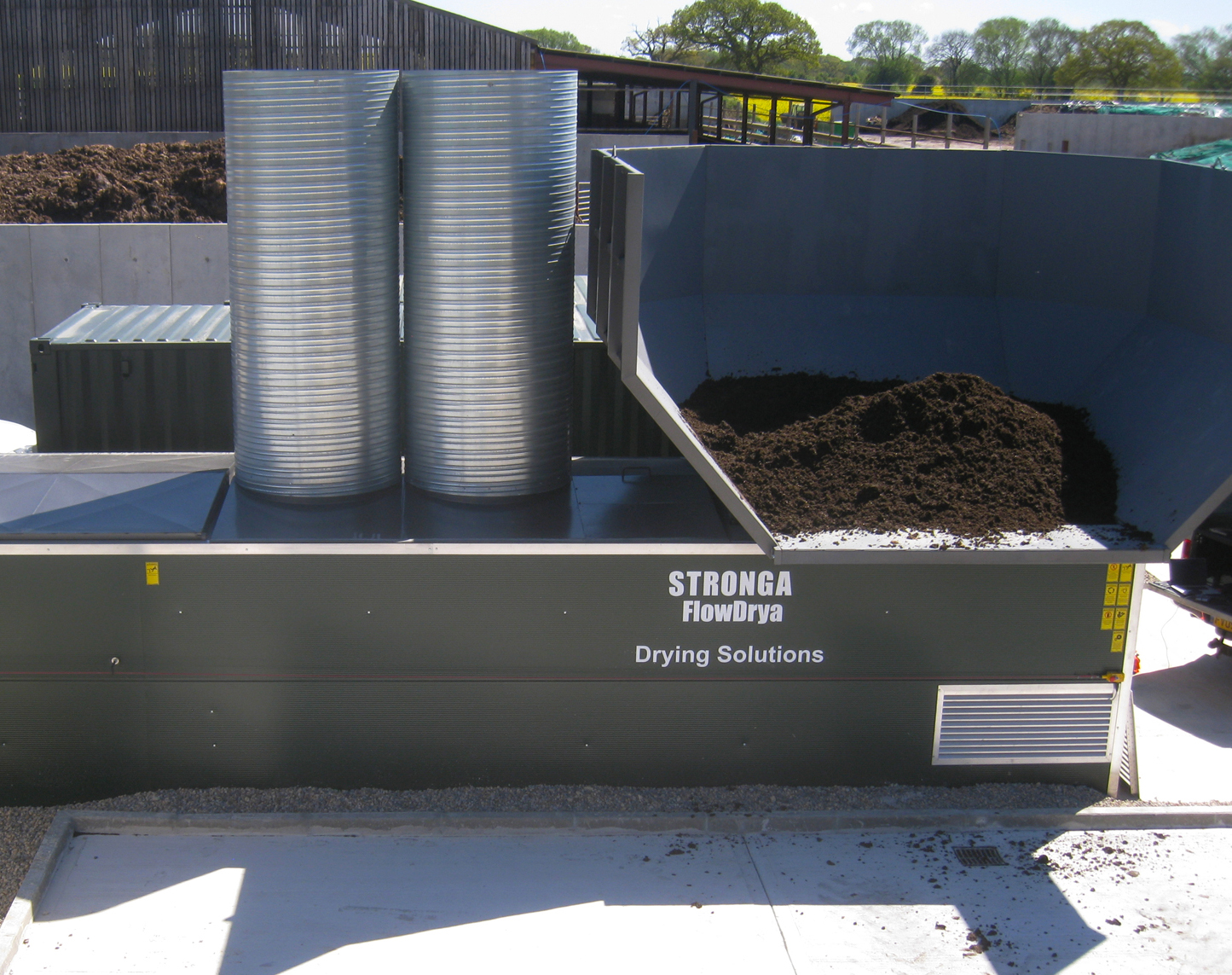
Comparing Equipment Life & Maintenance Costs
Investing in a reliable, sturdy and robust drying system is important. This will, in turn, reduce any after-purchase maintenance costs down the line. Although we pride ourselves on our quality, Stronga remain in contact with all customers after purchasing, maintaining strong collaborative relationships.
FlowDrya: Despite having a long service life that can operate for over a period of 8,000 annual operating hours, the FlowDrya may actually only be working for less than 2,000 hours because of its unique stop-start operation. The result is 4x less component wear due to the simple construction and lack of moving parts which offers super low service requirements and maintenance costs. These combine together to extend the lifetime of the dryer.
Belt Dryers: The multiple components running belt dryers work overtime and continuously for every operational hour, which really adds up in high duty cycle situations. All electric motors, gearboxes, bearings and shafts work continuously, in contrast to Stronga’s stop-start system, thus wearing out over 4x faster compared to the FlowDrya.
On-Floor Dryers: The service life of on-floor dryers is variable, concrete drying floors have a longer life span than hard wood alternatives but on-floor systems still wear out equipment in other ways. Along with maintenance costs, on-floor drying requires more labour-intensive unloading and telehandler loading which not only increases labour costs but invokes telehandler/loader deprecation costs – there are many maintenance costs which must be considered with on-floor dryers.
FlowDrya not only has one of the longest service cycles but also the lowest maintenance costs and requirements.
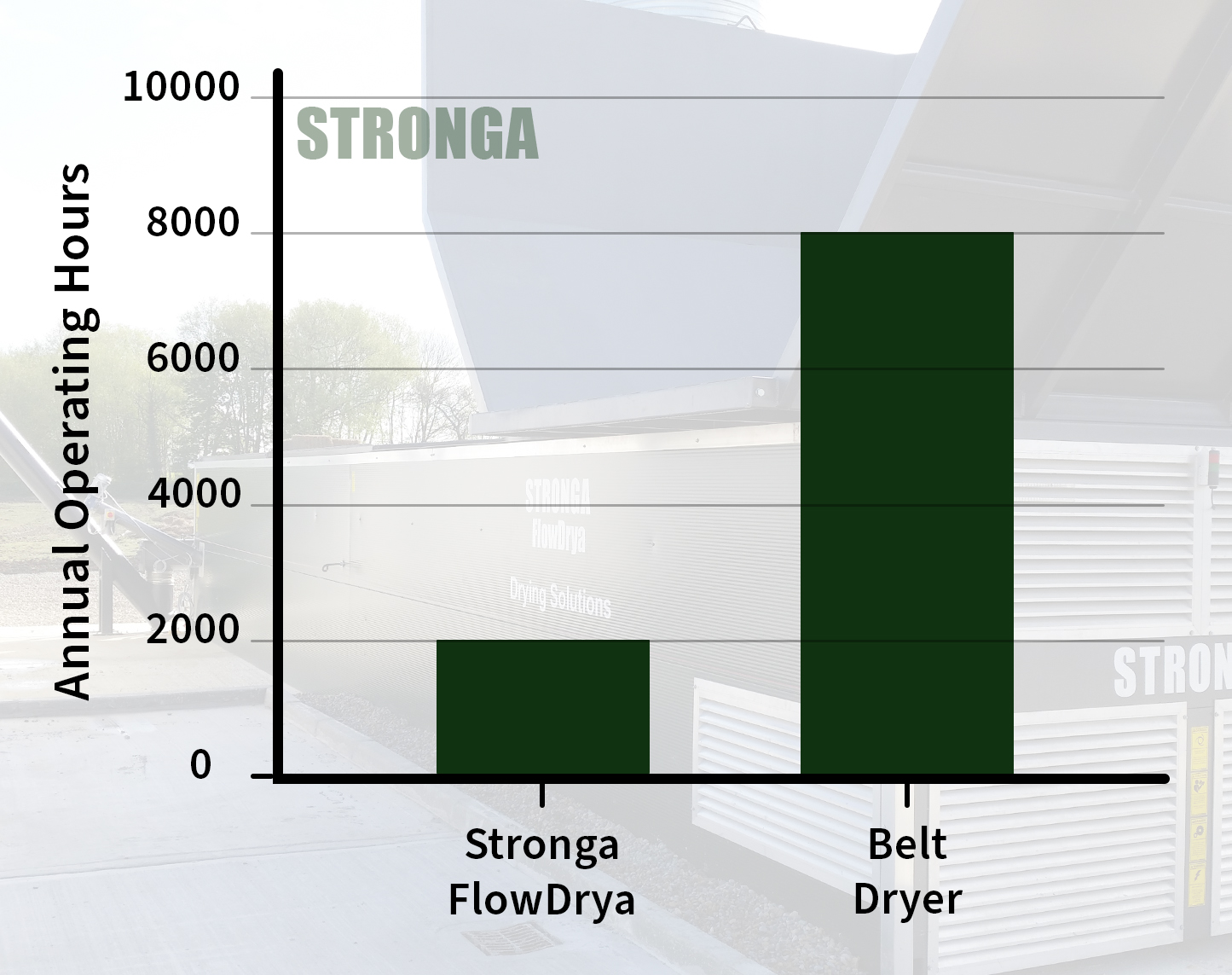
Comparing Dryer Installation Cost & Time
FlowDrya: FlowDrya is a modular solution which allows you to get to work - fast. It is fully assembled and pre-commissioned at the Stronga factory so the monocoque sections of the dryer can be installed quickly and easily on-site. Once installed, drying can begin almost immediately after. The Stronga team typically spend two days installing equipment on-site with commissioning taking place when the dryer is setup. Our specialist team stay with the client as material is loaded into the dryer and dried, answering any questions on operation and maintenance. Where requested, Stronga also offer remote access for remote, ongoing support and training.
Belt Dryers: Belt dryers are often large structures made with hundreds of parts and bolts, these components are never assembled together prior to arriving at the customers work site, this leads to long periods of installation while the whole structure is assembled. Often, parts will not fit first time and missing parts are frequently an issue, extending the build time further. After the ‘super structure’ is bolted together and all complex moving parts are installed, including belts, bearings, motors and conveyors, everything needs to be aligned, making belt dryers a time-consuming and costly installation.
On-Floor Dryers: Due to the nature of the structures, planning permission is often required for the building of on-floor biomass dryers. This extends costs and adds uncertainty to the sales process. Grain type on-floor dryers are building-like structures and the installation process is much the same as constructing a building, with the added complexity of constructing tunnels and under floor vents, in such a way to balance airflow. Given all the factors, on-floor biomass drying systems often have the longest installation periods.
With all factors considered FlowDrya’s shorter and more simple installation process ensures no time is lost – allowing biomass drying operations to commence almost immediately after delivery of the dryer.
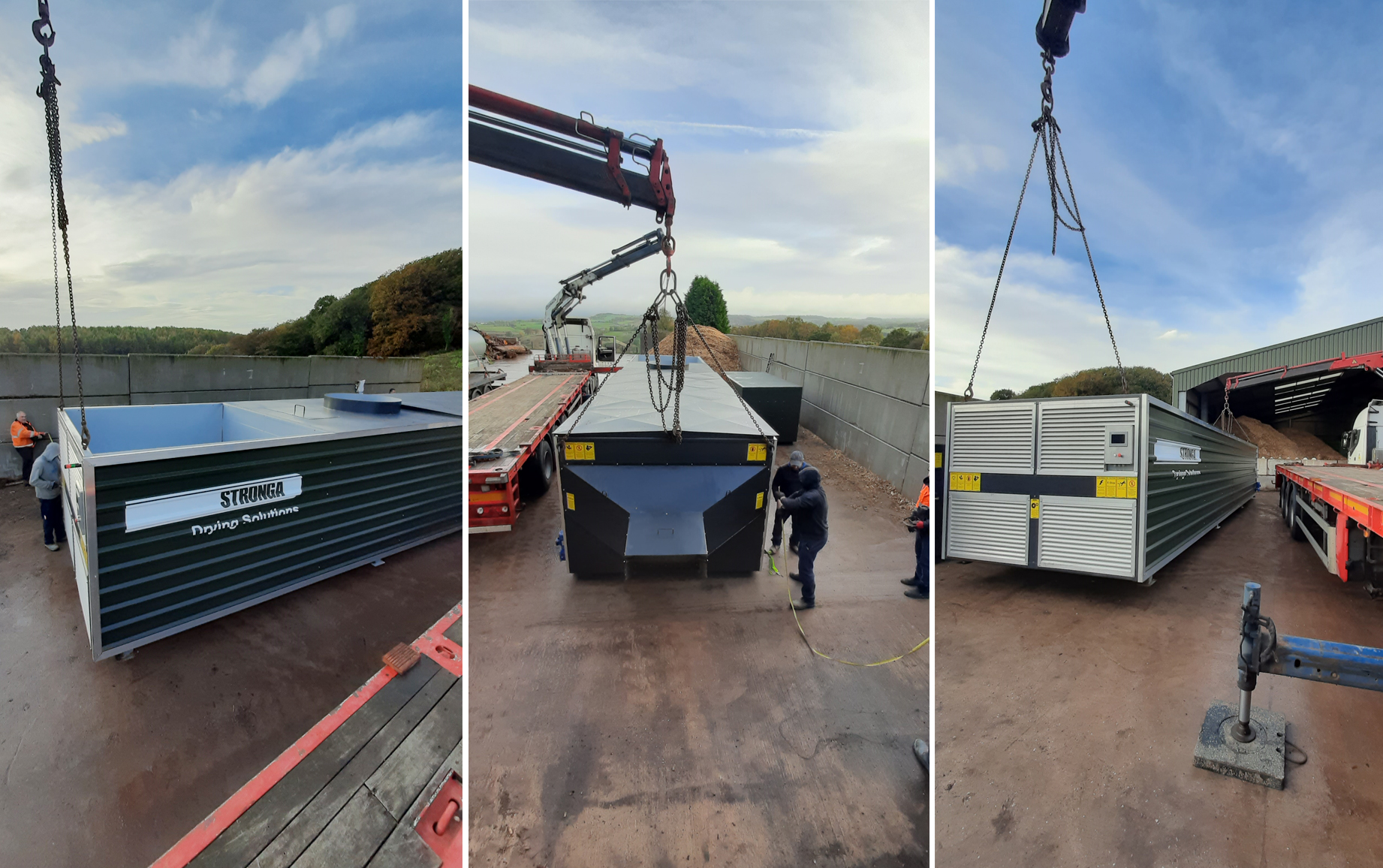
Comparing Electric Energy & kW-e Operational Power Requirement
In recent years, electrical energy costs have increased by more than 100% in some regions. Therefore, the operating hourly demand has become an even more critical factor to economic drying processes. FlowDrya offers 3x lower electrical demands than alternative drying systems; this leads to large financial and carbon savings.
FlowDrya: Electric costs and demands are low due to the stop-start arrangement where the operational-use and amount of electric depends on the stroke setting. In low moisture removal situations, the dryer may only be running for 20 minutes per hour – thus reducing stress on the machine and keeping electrical costs to a minimum. Additionally, by using residual heat to fulfil biomass drying requirements, FlowDrya becomes one of the most conservative drying systems available.
Belt Dryers: In comparison to FlowDrya, belt dryers have approximately 3-4X greater electrical power demand from the several paddle agitators, motors and gearboxes. Biomass levellers and sweeper motors used to clean the belt increase electrical load requirements significantly. FlowDrya doesn’t require these added complexities to operate effectively.
On-Floor Dryers: Although on-floor dryers have few components, they have a higher reliance on handling and operator involvement. Increased fan back pressures create additional energy requirements which increases electricity costs and electrical parasitic load which is an increasingly expensive commodity. Loaders and telehandlers required with this increased handling mean on-floor biomass dryers have higher service costs, where loader buckets are used for agitation and emptying the store.
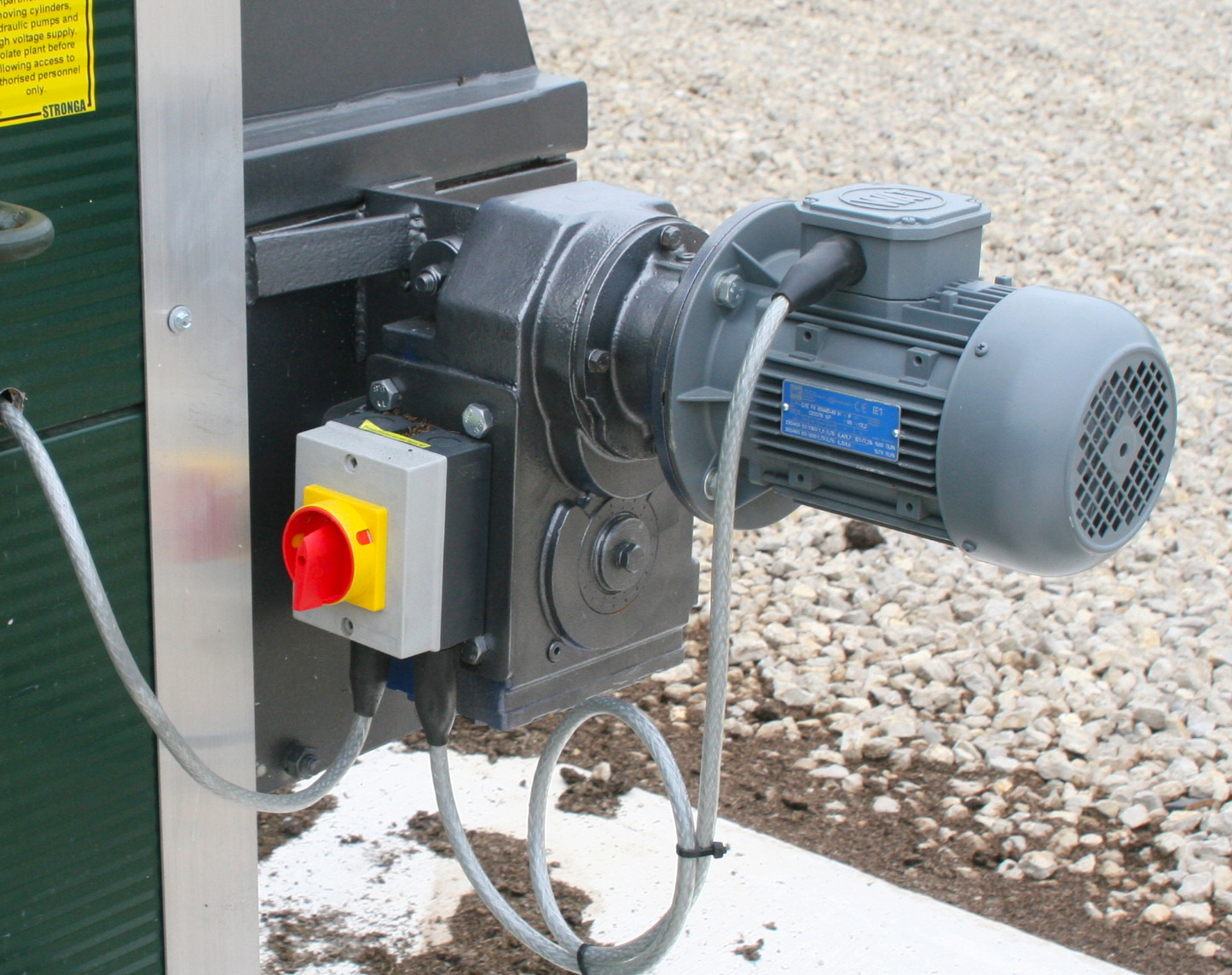
Comparing Hopper Refill Frequency
Labour costs and availability have become increasing concerns for businesses in recent years and so, refilling frequency of the dryer becomes a key consideration if businesses are to remain competitive in the market.
FlowDrya: With huge biomass in-feed hopper capacity, there is less reliance on hard-to-come-by, reliable and expensive labourers. FlowDrya’s large hopper capacity offers industry-leading, pre-drying storage, which significantly extends reloading intervals reducing handling and labour costs. With extension hopper options available, wet material capacities can offer 8x more capacity than comparable belt dryers. At 3am on a Sunday morning, this will matter to you!
Belt Dryers: Most belt dryers have almost no hopper capacity. While some units may have separate infeed systems, they have a small capacity of circa 5m³ and require a full-time loader and operator to keep the operation in motion, even during over-night periods.
On-Floor Dryers: Through our research working together with existing on-floor dryer operators, we have seen first-hand that experienced loader operators spend many hours loading out the floor, attempting to spread the biomass evenly and then after-drying, attempting to mix the material, gauging when drying is complete. After drying, handlers are required to empty, move and store the dry output elsewhere. On-floor operators are aware of the costly series of associations. One client we spoke to was refilling bays every 4 days on average, or 92 times per year, the ‘semi-hidden’ associated costs are enormous.
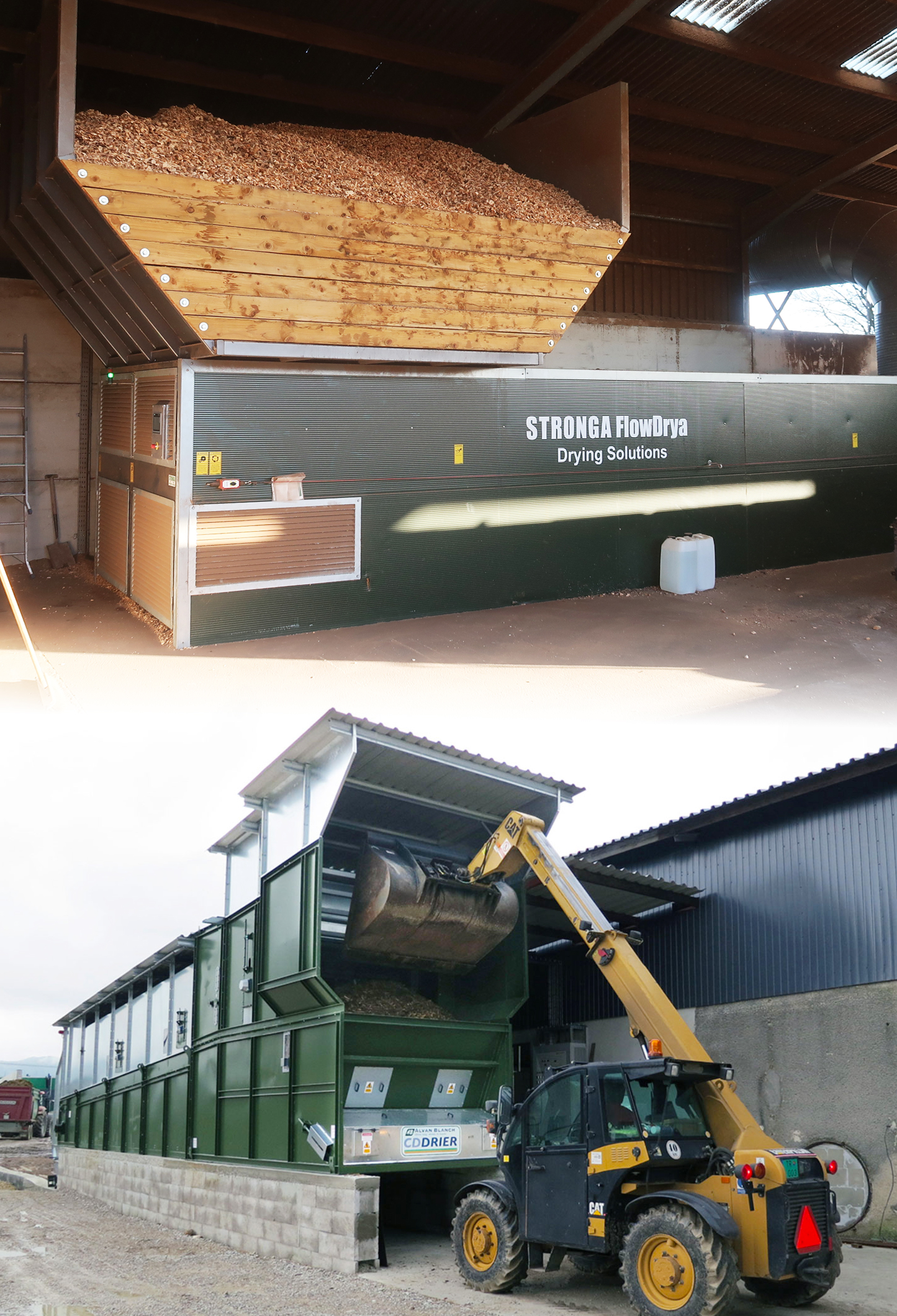
Comparing Material Agitation
Anyone with experience drying biomass understands the importance of agitation in the evenness and efficiency of the drying process. Thorough agitation is a fundamental component of an effective biomass drying process.
FlowDrya: Stronga’s compact biomass drying system has excellent agitation thanks to its unique, automatic and integrated full mixing of material on the drying bed. This is an especially useful feature for woodchip feedstock, where agitation occurs at a depth of between 350-450mm. FlowDrya’s full material mixing ensures all output material is evenly and thoroughly dried. The PulseWave™ agitation feature prevents any over or under drying issues, inherent in other types of drying system. The animation below visualises the PulseWave™ motion.
Belt Dryers: Belt dryers offer no real agitation of the material. As an inadequate solution, belt dryers employ various types of flickers and cross dryer paddle rotors which offer little agitation benefit. In reality, these flickers do very little to mix the material which is thinly distributed across the belt – all they do is contribute to higher electric costs and increase complexity.
On-Floor Dryers: On-floor drying systems offer no material agitation whatsoever. The outcome is a re-condensing “fronts” effect while the output material is unevenly dried – the top layer is never fully dried whereas the bottom layer is over-dry. Manual agitation is the only choice, this is extremely time consuming and ineffective. Without proper agitation, floor drying is extremely inefficient for energy consumption and evaporation rate.
Comparing Control of Drying Biomass
Another critical point to consider when buying a biomass dryer is control of time in the process. Productive and efficient drying processes are fundamental for effective output rate; the rate of biomass drying can make or break the success of your biomass drying operation.
FlowDrya: FlowDrya offers complete control of the time material is on the drying bed via the easy-to-use, smart-control console which is unique to FlowDrya. Operating in the form of strokes per hour, operators can gain real control of output moisture (each stroke creates full agitation of the biomass depth). Modern, reliable HMI touchscreen controls which are fully self-protecting, intuitive and easy-to-use and they have all the features customers need, including setting key parameters, data and energy logging.
Belt Dryers: Belt dryers usually operate with a thin layer of material on the belt. Operators are required to manage the belt tension and adjust the belt speed according to the biomass, moisture content and ambient temperature and humidity variations. This process is often overly complex and harder to operate than FlowDrya’s well-developed DryStation™ HMI. Additionally, because belt dryers have more components, which include air-knife type fans, belt sweeper motors and flicker rotors, there is an added control complexity.
On-Floor Dryers: On-floor dryers pose a significant issue; there is no way of ‘stopping’ the drying process. Grain-type on-floor drying systems often over-dry material at the bottom of the biomass pile with under-dried material at the top. Consequently, this process causes large amounts of wasted energy and time, as well as significantly reduced, uneven output. There is little control over the drying process in on-floor biomass drying systems, where there are large amounts of moisture to remove.
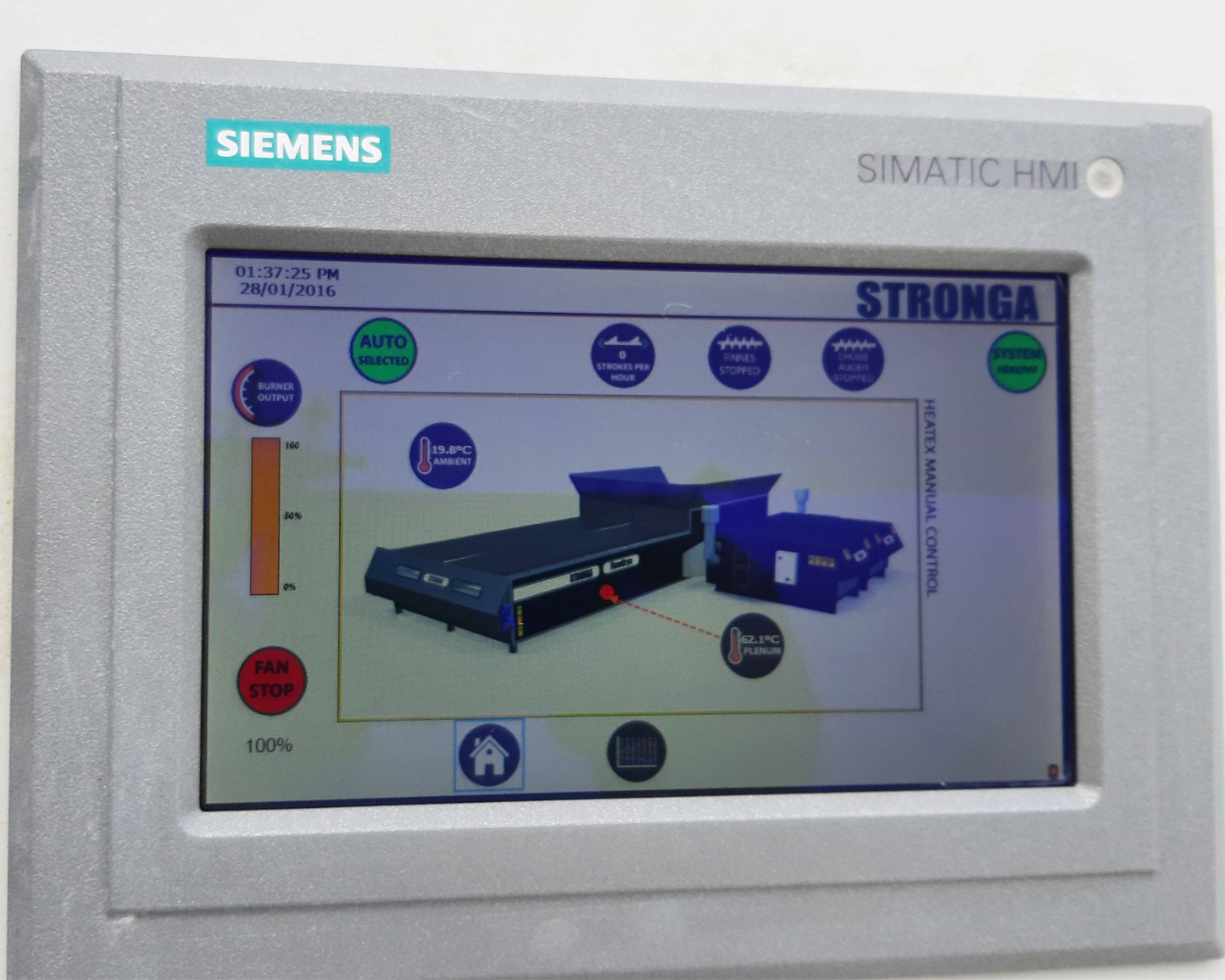
Comparing Fire Risk
FlowDrya: To our knowledge, FlowDrya systems have never been at fault for any fires that have occurred on site. With low temperature drying, indirect air from the independent Heatex, stop-start operations, very few, slow moving parts and no bearings, chains or sprockets, FlowDrya represents an extremely low fire risk, making it exceptionally safe to own and operate.
Belt Dryers: Historically, belt dryers have caught fire due to the over-heated bearings or due to plastic belts slipping and heating up. Some belt dryers also use direct flame heat sources which have higher fire risks in the same way drum dryers do. Polymer belts have an inherent problem causing static electricity which has consequences relating to electric discharge. Many belt dryer manufacturers have sought to evade this risk by installing anti-static polymer belts; however, it is not clear how effective these are. Due to frequent belt dryer fires, insurance companies often require the owner to install expensive fire suppression systems which further add to the service requirements, maintenance costs and overall capital outlay.
On-Floor Dryers: With very little control over the drying process, operators often unintentionally over-dry the material, especially close to floor-level; historically this has caused devastating fires. Additionally, loader buckets scraping the floor create sparks in biomass due to friction and, once a fire has ignited in the on-floor building, it spreads rapidly and is difficult to control. Many clients often under-estimate the risks of on-floor drying fires. Stronga have been approached by many clients after such fires, to install fire-resilient, continuous drying systems.
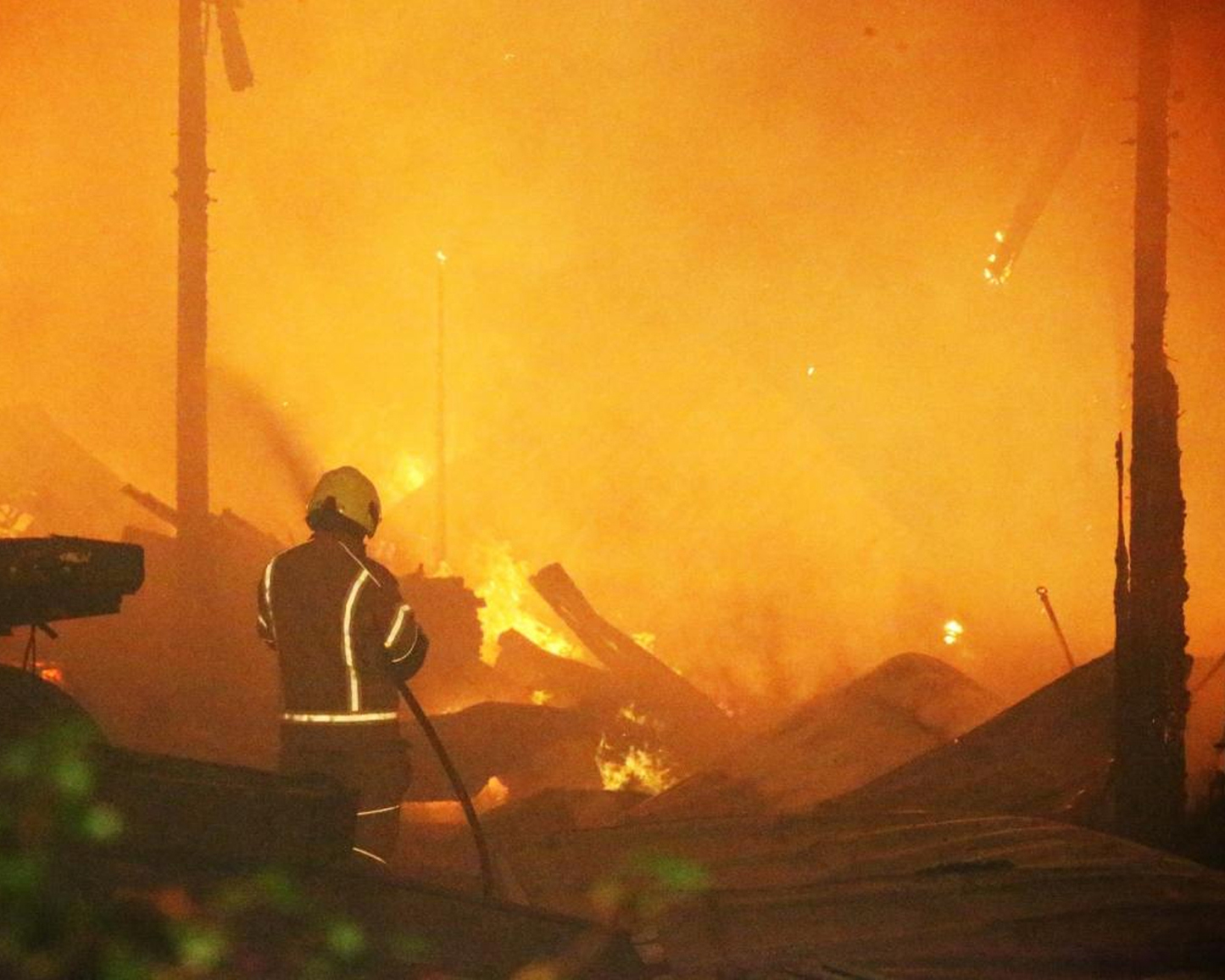
Comparing Dryer Footprint
FlowDrya: FlowDrya has a very small footprint because material is dried at a far greater depth of up to 500mm compared to approximately 100-150mm on a belt dryer. Deeper drying with full agitation means that FlowDrya can be more compact than like-for-like belt dryers. FlowDrya can be scaled to suit parameters, including sizing the dryer for residual heat loads and amounts of kWh/th available. Physical land space has become increasingly valuable over recent years; a compact, modular biomass drying solution suits clients with space limitations. The FlowDrya system is a hit with small-scale operations in particular, looking to conserve valuable land.
Belt Dryers: Belt biomass dryers operate at a much shallower depth than the FlowDrya, meaning the dryer needs to be much larger-scale – potentially up to 3x bigger than equivalent FlowDrya models. Physical commercial space is often at a cost premium; this can be a key deciding factor for some clients.
On-Floor Dryers: Stronga recently worked with a client who had circa. 600m² of space in total dedicated to his on-floor biomass drying bays, plus additional yard space for access. For comparable output, the modular FlowDrya can sit outside, occupying a mere 60m² - 10% of the space required.
Note – the graphic below is for illustrative purposes only. Dryers from all manufactures can vary in size considerably, depending on the material, location of the dryer and so on.
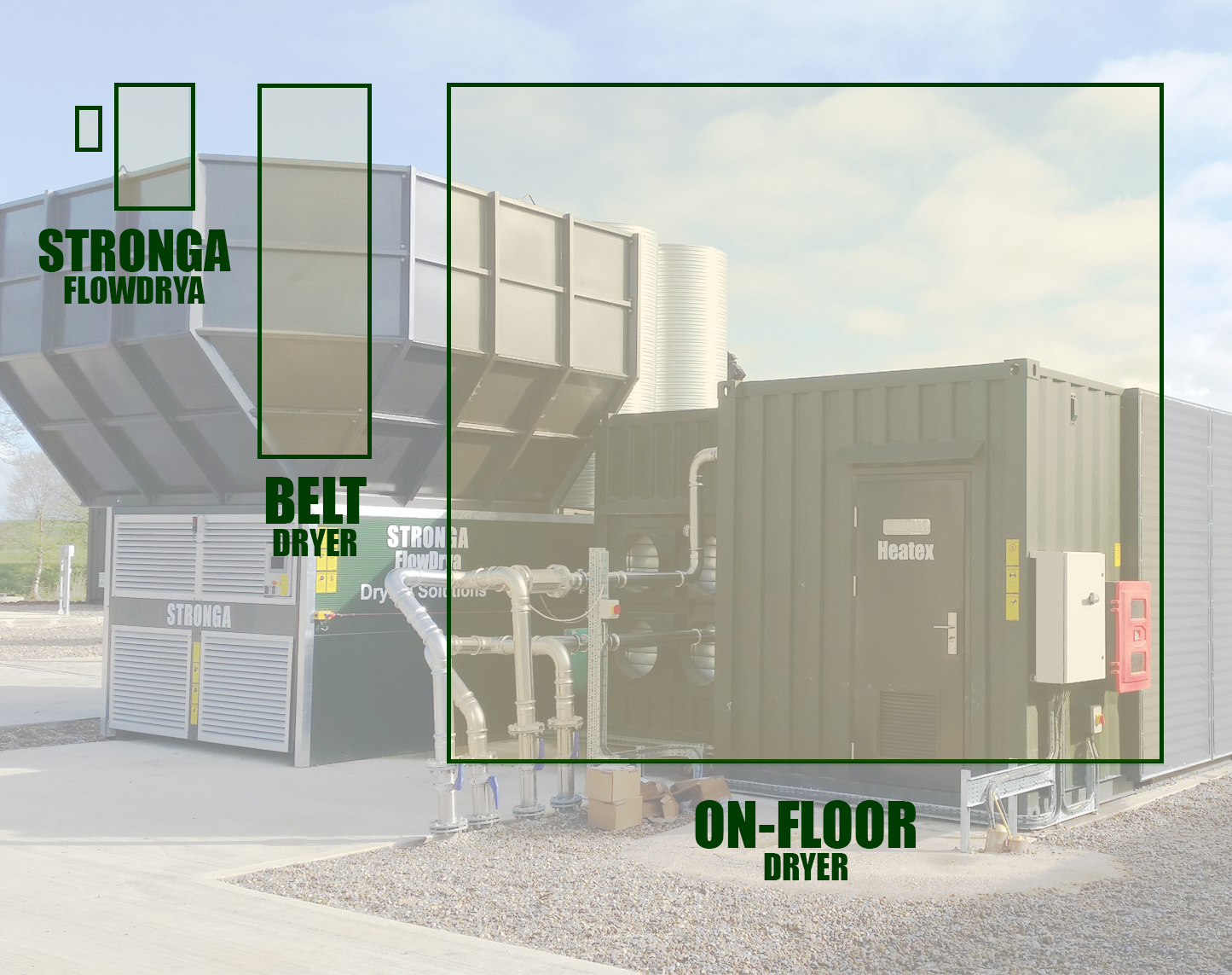
Comparing Fines Material, "Screener-Cleaner"
Fines separation ensures the main dry output material is clean as the fines fraction can contain foreign material such as fine sand, glass etc. In some processes, such as gasification and pellet-making, it is vital to use clean material to reduce wear and extend the service life of equipment, where foreign-matter can cause a multitude of issues to machinery.
FlowDrya: A unique feature of FlowDrya is the in-built screen / fines fraction separation auger for soil and heavy small particles. Small fines drop through the main drying steel floor and are collected in the sub-floor plenum and augured out into a separate container, away from the main output of material. The type and amount of ‘fines’ depend on the input material.
Belt Dryers: Belt dryers offer no potential for screening or cleaning of the material – fines particles and foreign matter often present in biomass can cause substantial issues, including blinding the belt, blocking airflow and causing the belt to jam. Larger foreign bodies within biomass can cut plastic belts which are expensive to replace and cause costly downtime.
On-Floor Dryers: As with belt dryers, on-floor drying systems also offer no material screening. In fact, fines material often finds its way into the channels under the drying floor which require manual cleaning, as they can block airflow. This further reduces the drying efficiency of an already poor performance biomass drying system.
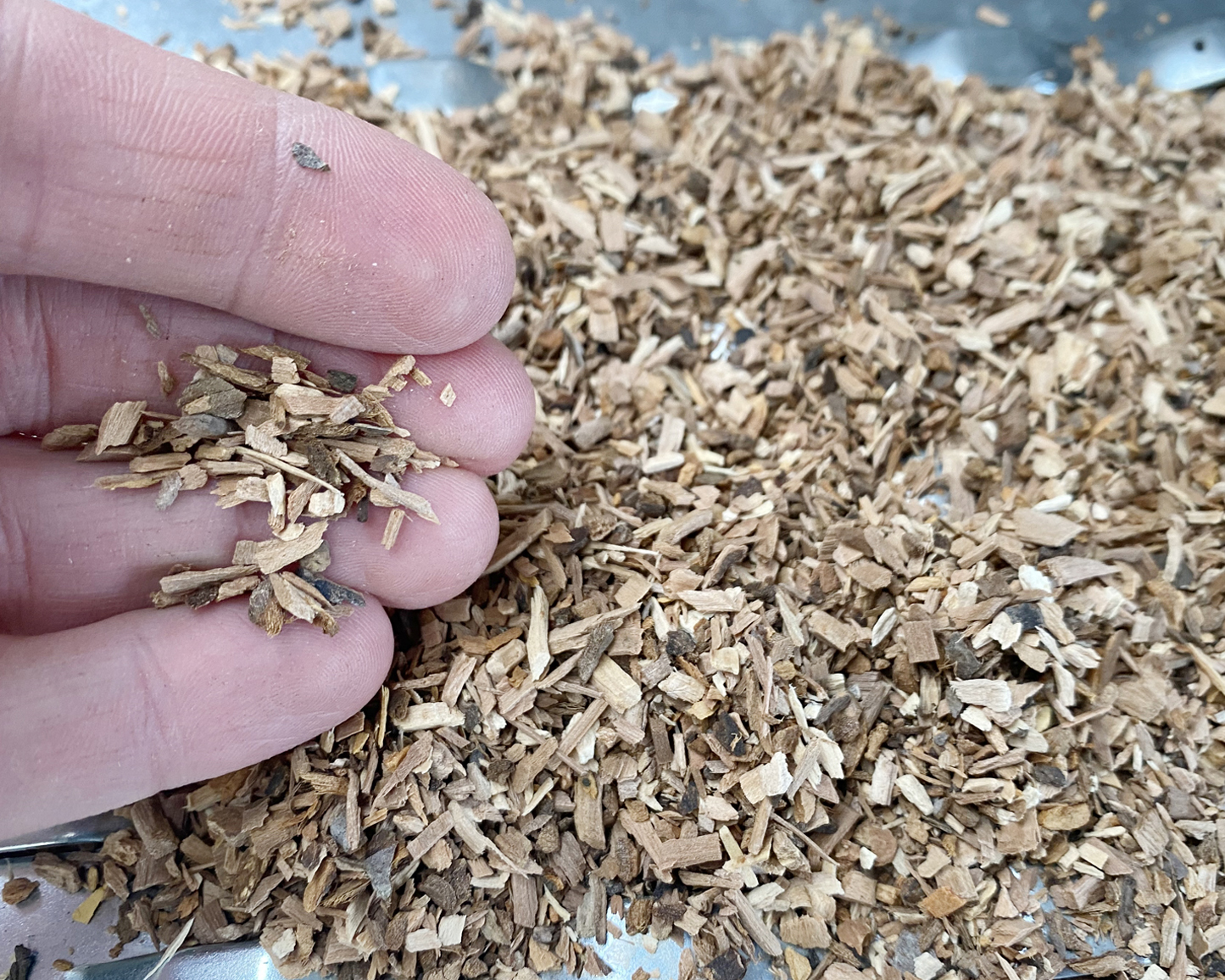
Comparing Capital & Operating Costs
FlowDrya: Due to the combination of factors above which include 1) compactness 2) few moving parts 3) fast onsite installation 4) highly useful PulseWave™ agitation system 5) low parasitic load, electrical requirements 6) low maintenance costs 7) long-life designs and (8) low depreciation costs, FlowDrya appears to offer the most economic biomass drying solution available in the market.
Belt Dryers: Belt dryers have a large footprint with hundreds of mechanical moving parts, adding to the initial capital outlay. Added complexity causes higher maintenance costs in order to maintain and extend the life of the machine. More downtime and increased ‘after-care’ maintenance requirements increase the overall operating expenses. Belt dryer’s complex components are difficult to maintain and expensive to replace.
On-Floor Dryers: As the UK-market chart below shows, the cost of concrete and building materials required for on-floor dryers have surged since 2020. The cost of ready-mixed concrete increased by almost 30% in 2022 alone. The capital costs of a grain-type on-floor dryer have also increased in the same period. Operating costs are often hidden in the form of significant amounts of labour to operate expensive loaders and telehandlers. The capital and operating costs of on-floor drying operations do not take account of the extremely low performance efficiency or the wasted heat energy which is not converted into evaporative drying output. On-floor drying buildings are not relocatable assets; it always pays to consider the long-term costs.
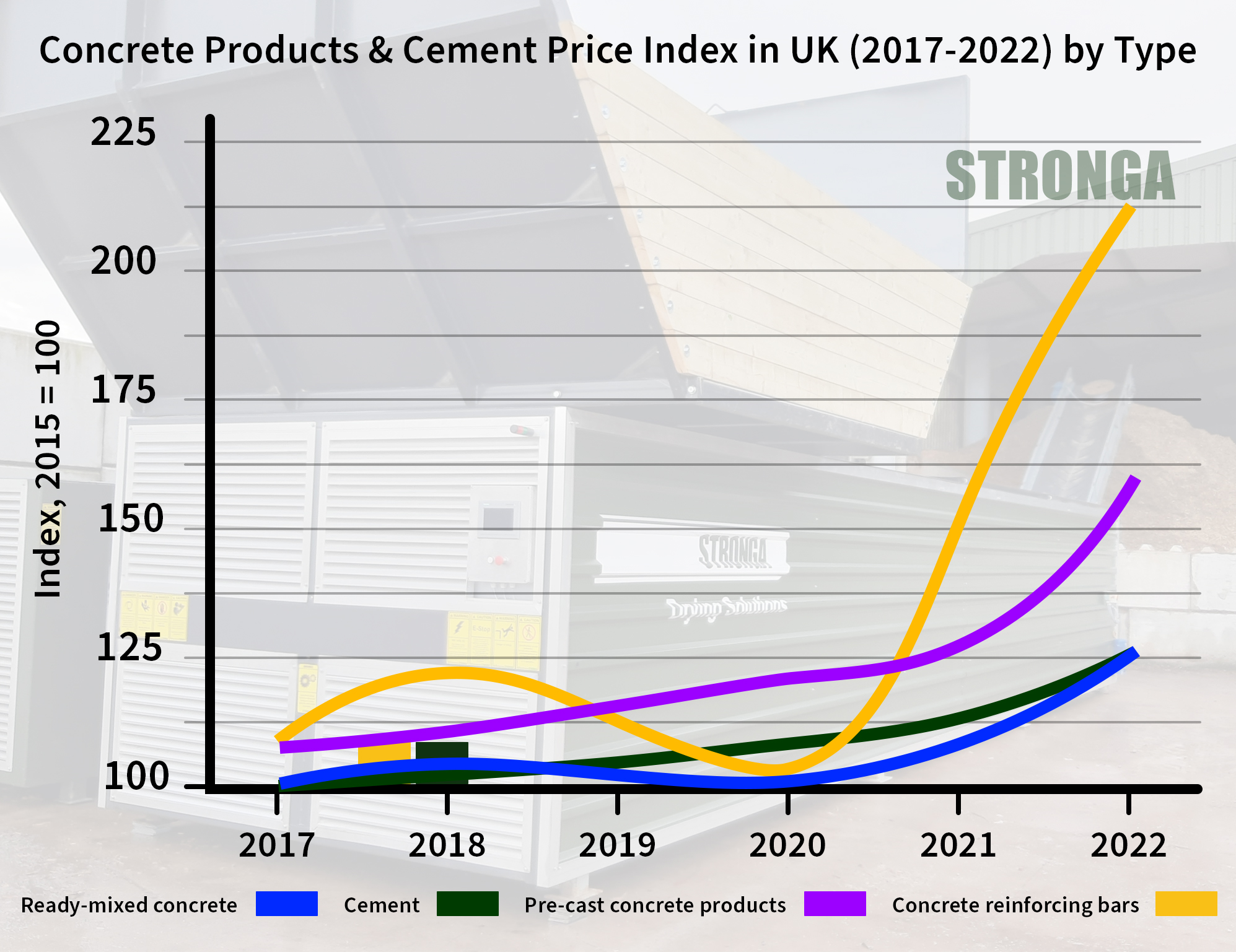
Stronga’s Talented Technical Team
With all points above considered together, we believe the FlowDrya system offers a far more economic, long life drying solution when compared to like-for-like belt dryers and on-floor biomass drying systems. All Stronga dryers are fully assembled and subject to strict quality checks in-house before delivery, and all key electrical components are labelled and organised for rapid installation.
Setting up efficient drying operations is a complex matter with many variables to consider. We have attempted to cover much of the useful ground in this article, however there are many aspects which are individual to location, seasonality, material variables, heat source variations and flexibility across certain materials. If you would like to engage further, we have experienced and talented experts available for individual project collaboration. Stronga builds bespoke continuous drying solutions for each client to match their requirements in terms of the properties of the material to be dried, heat source, location and more.
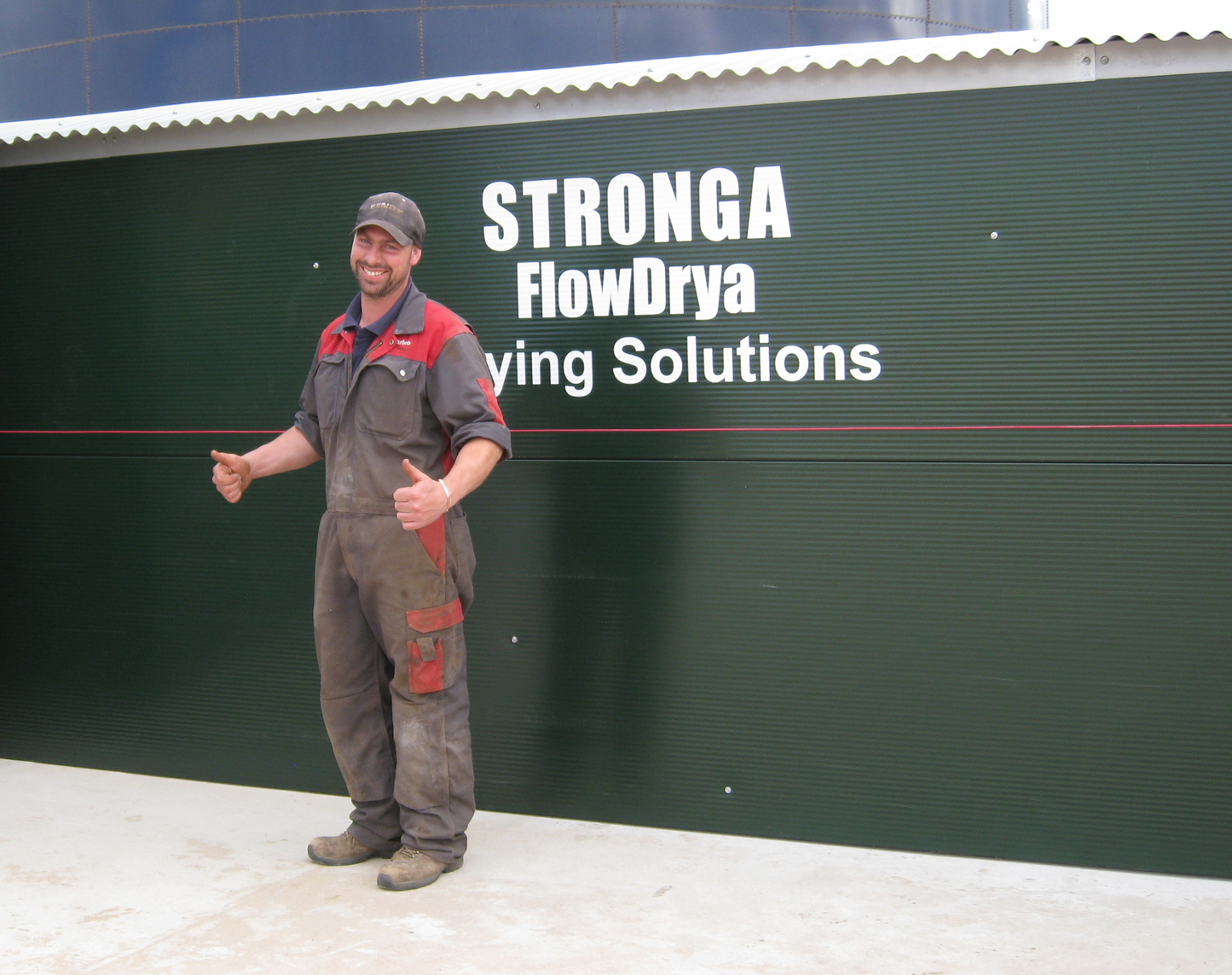
Setting the Quality Standards
When compared to on-floor and belt drying systems, the business case for FlowDrya is highly compelling. The user-friendly operation and minimal maintenance requirements make for a highly economic biomass drying solution. Today, FlowDrya is the basis for our success in a wide range of applications and sectors. Our aim is to continuously improve our biomass drying systems with respect to emission reduction and energy efficiency. We are proud of our many years’ worth of experience in designing and building biomass drying solutions and are justified in claiming that we are setting quality standards, worldwide.
Contact our technical team today for more information. We look forward to hearing from you.
Email – sales@stronga.co.uk or call – 01992 519000
* This knowledge we share is based on customer feedback, figures included in this article are estimates and based on average FlowDrya models. Actual performance data can only be issued on a project-by-project basis depending on the model of dryer and other factors. There are many factors to consider in drying. Each project, location, material and heat source create the many variables in performance. We have done our best to compare solutions; however, we recommend you speak directly to our team for more detailed information.
Share this post