Wood Gasification: Progressive Technology
Whilst wood gasification was first developed way back in 1839, it remains increasingly relevant in modern times where businesses are increasingly embracing in-house energy production in a volatile world. Wood gasification provides a valuable alternative to fossil fuel usage, reduction of greenhouse gas (GHG) emissions, and sustainable and independent energy production.
The process, which is visualised in the graphic below, involves pre-drying biomass (typically waste wood, tree cuttings or crop residues) and then heating the dry material in an oxygen-regulated, wood-gas chamber. There are multiple steps involved in ensuring the gasification reformer provides electricity, heat and power, as well as its desired fuel output, wood-gas/syngas. These steps include pre-drying the fuel using Stronga’s FlowDrya system, pyrolysis, oxidation, gasification and reduction. The heat from the generator, syngas output and flue gas can all be used for heat, power, electricity and energy usage through CHP production. These outputs can be used in place of non-renewable fossil fuels to power engines and biomass drying systems.
There are many factors that ensure the gasification process flows smoothly. Moisture content of the input biomass is a key but often underappreciated factor which, if not considered, can have a detrimental effect on the energy and syngas output. Read on to learn more.
Wood-Gas from Wood Chips
Gasification allows businesses to convert organic biomass - which would typically be left to release GHG emissions into the atmosphere - into valuable energy. The biomass input allows sawmills, forestry owners, tree surgeons and farmers (dairy/grain) to take control of their own energy production while combatting rising energy, electric and gas import prices.
Global energy security is fragile; recent conflict and disruptions to shipping have only inflated prices further. Rising costs have only reiterated the importance of becoming self-reliant with local energy production. Gasification is available in different scales and it allows business owners to achieve in-house energy security. What’s more, it uses available resources that would likely only have gone to waste (woodchips, arb chip, crop residues and manures) to produce self-sufficient renewable heat, power and energy via CHP, heat exchange methods and gasification.
The dried fuel input (wood chip/crop residues etc.) can be sold to energy production plants before gasification as input fuel, or alternatively, after gasification. After gasification, the bio-fuel output can be retained to power local communities or used within the local-scale gasification process to contribute towards the operators own circular energy economy. It can also power on-site equipment and internal combustion engines. When wood-gas/syngas is used in place of a gasoline/petrol run engines, the emissions are far cleaner.
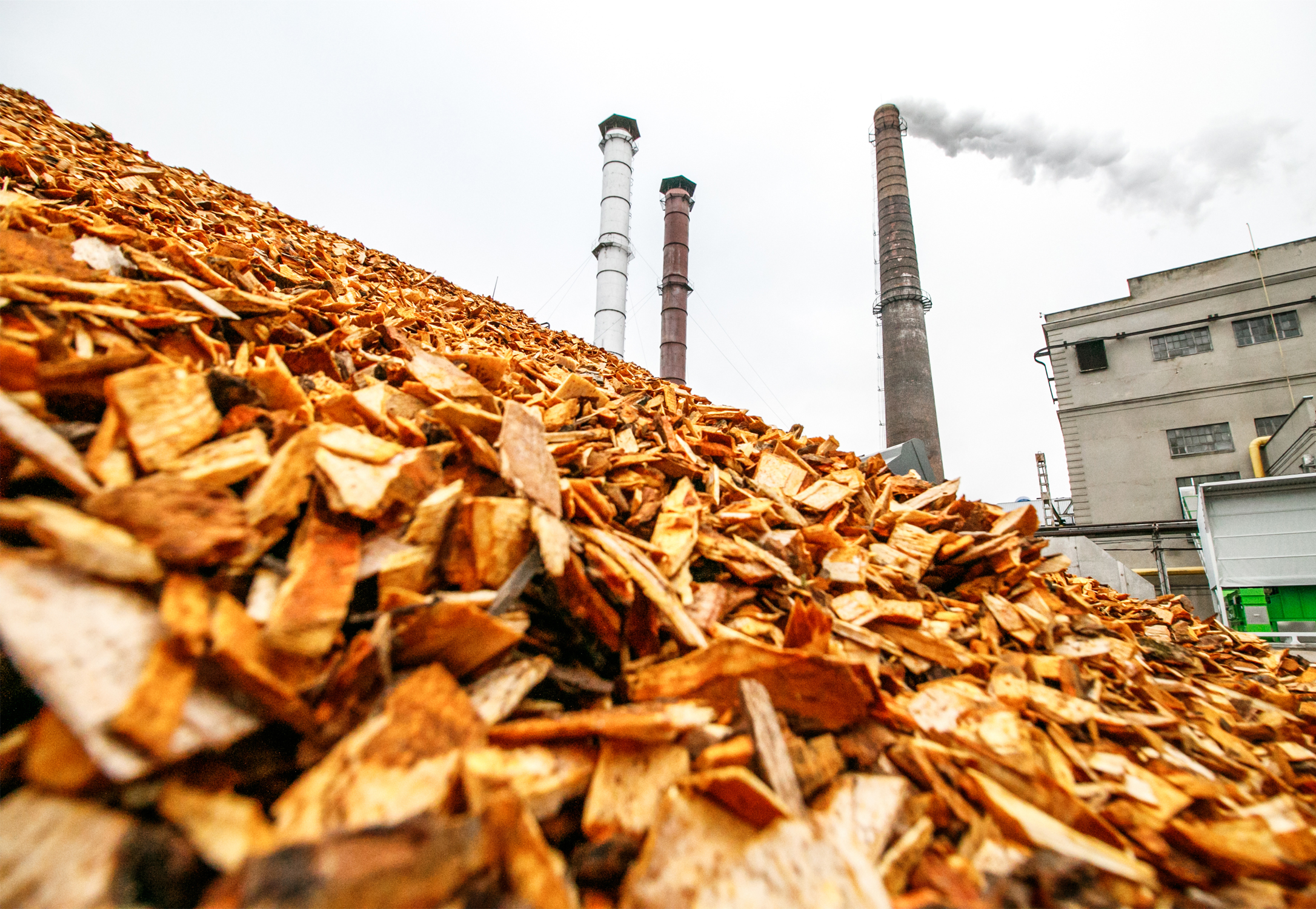
Become Energy Independent
In light of recent external energy pressures, gasification technology allows the production of cleaner, greener energy and local heat and electricity, whilst gaining another income stream. This allows customers investing in gasification systems to enjoy the benefits of these readily available resources and become energy independent.
Energy-efficient technologies such as gasification are often eligible for environmental agricultural grants. By utilising residual engine heat and reducing GHG emissions, gasification plant owners can make positive contributions towards reducing climate change. Turn your resource into revenue, get in touch with Stronga to learn more about pre-drying biomass before gasification - info@stronga.co.uk
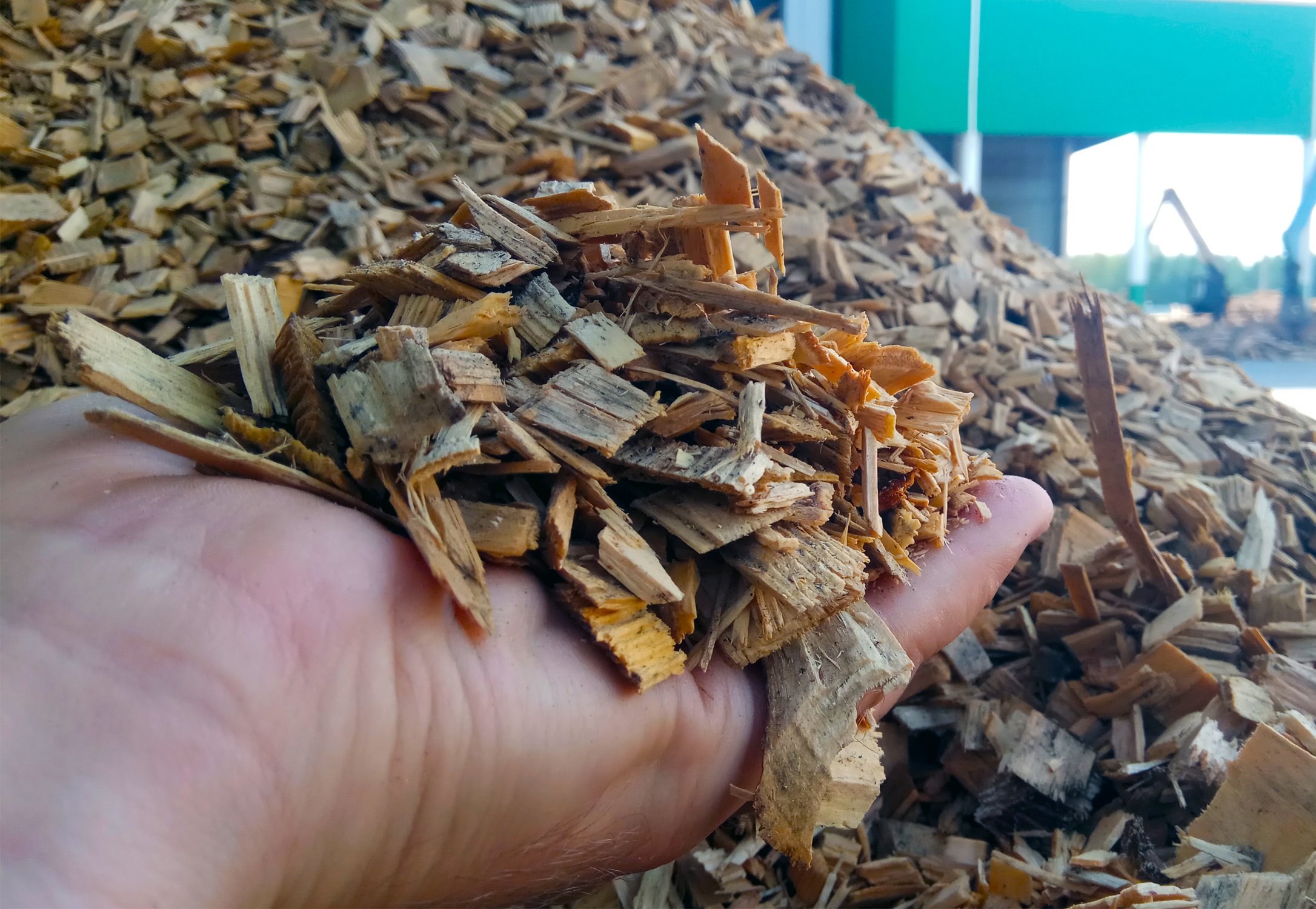
Improve Gasification Processes & Energy Outputs through Drying Biomass
When carried out efficiently, gasification paves the way for significantly reduced waste and fewer GHG emissions. However, the process needs to be optimised to avoid high energy consumption and the emission of harmful by-products. Drying biomass and crop residues before pyrolysis and gasification is one of the most important (but often under-valued) steps in the entire process. High moisture content is usually the common denominator when ‘un-clean’ gases are emitted from the reactor – placing high importance on the role of the drying system.
Whilst woody biomass is one of the most renewable sources of fuel available for gasification, it also has the ability to retain large amounts of moisture, with moisture levels varying depending on local climate and location of the plant. This moisture needs to be evaporated prior to gasification to avoid high operational energy usage, low quality output, low value gas and smoke/ash fumes. The graph below shows the correlation between moisture content of the fuel in relation to cold gas efficiency and air equivalence ratio. You can see that cold gas efficiency declines significantly with a higher moisture content input material.
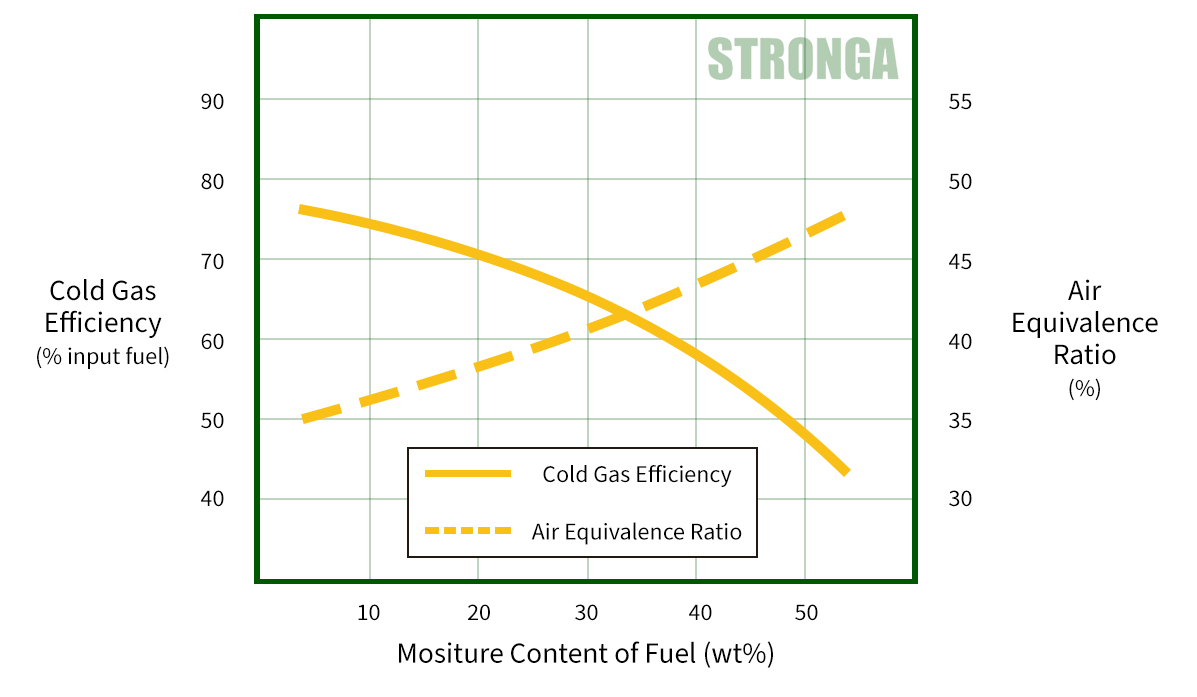
Modern Biomass Drying Equipment
Without pre-drying the biomass input before gasification, the process becomes far less energy-efficient, defeating the purpose and affecting the clean syngas output. Additionally, biomass with higher moisture content decreases the stability of the process and increases the chance of the gasifier malfunctioning, releasing carbon monoxide and higher volatile organic compounds.
For high-value heating and efficient wood-gas/syngas production, biomass is considered optimal with a moisture content of around 10%. The drying process can be a long and costly process, particularly in the case of sub-optimal dryer arrangements. Stronga’s drying systems offer a modern, well-proven, highly-efficient alternative to traditional drying practises, increasing the efficiency of heat and energy generation for gasification.
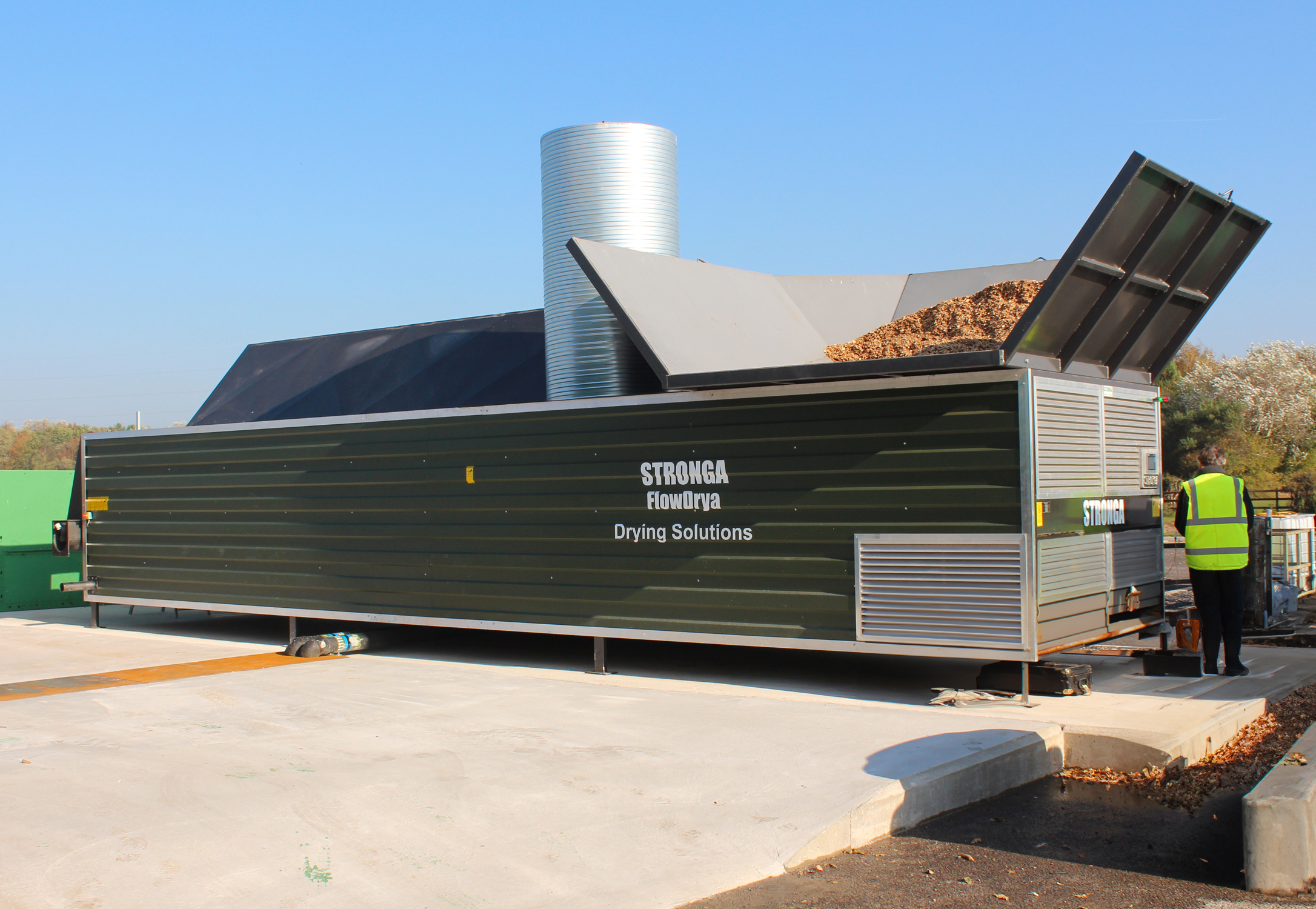
FlowDrya & Heatex; Offering Optimal Efficiency
Stronga are highly experienced in the niche field of drying various biomass materials with multiple years’ experience dealing with gasification production companies across the world. Our team design bespoke dryers on a project-by-project basis, guiding the client through the various intricacies of the project to optimise the dryer for the best outcomes.
Gasifiers have different operating sizes and requirements and so do our continuous drying systems; select the size of your gasifier and state your input biomass and the team at Stronga will size and scale your FlowDrya and Heatex equipment accordingly. Drying is dependent on energy type and availability, properties of the biomass material, climate and much more. Contact us today and we will endeavour to provide you with bespoke guidance on your dryer/gasification needs – info@stronga.co.uk
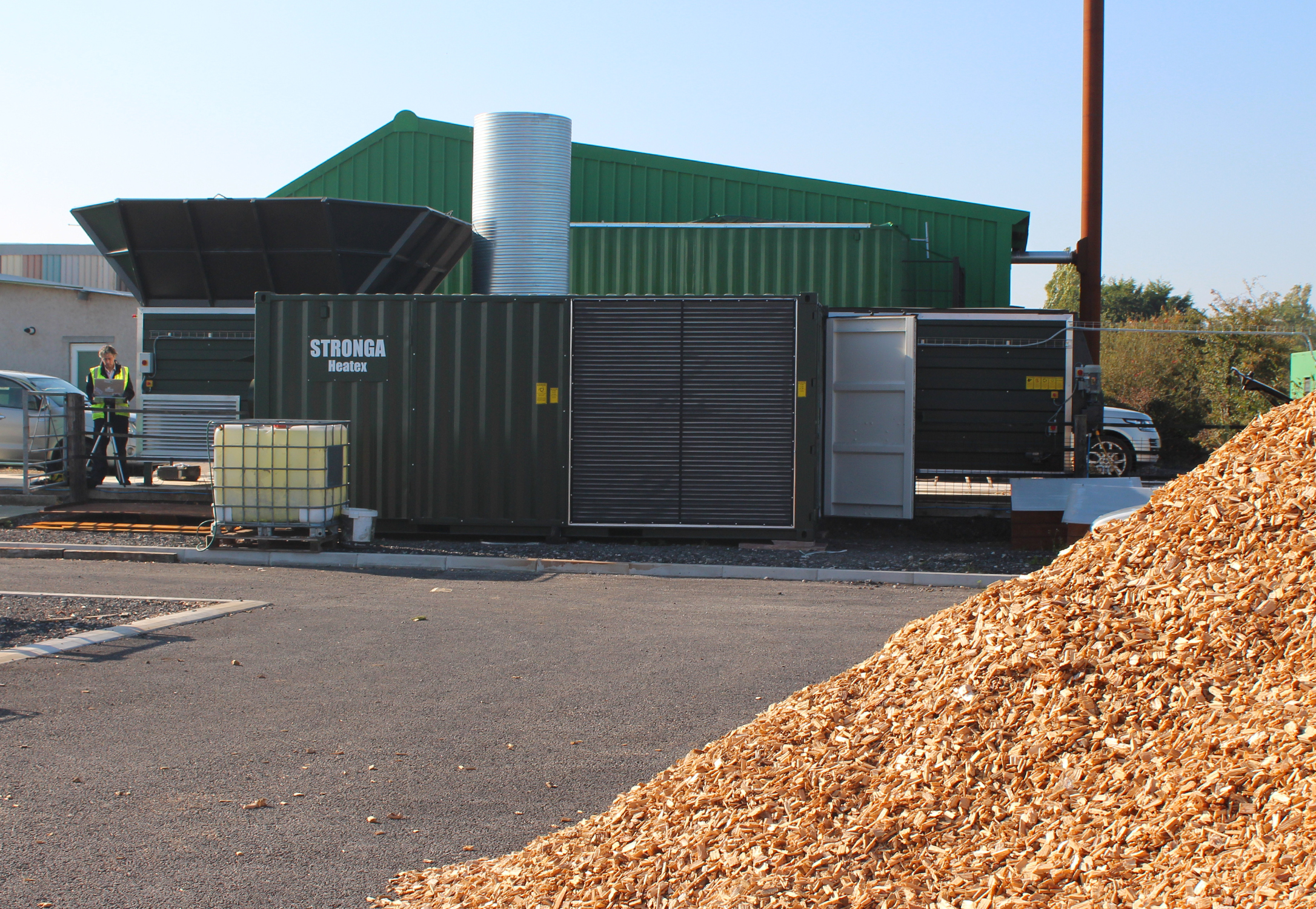
Typical biomass inputs for gasification are well-suited to the FlowDrya which offers an easily-controlled continuous drying process to reduce the moisture content of wet materials. Together, the FlowDrya and Heatex systems can accept residual heat, generator heat or flue gas, allowing them to fall in line with energy efficient requirements as part of your circular energy economy. Drying increases energy yield and quality whilst reducing energy usage and harmful emissions. Discover the key benefits of the FlowDrya.
- Simple design with no belts, chains or sprockets – allowing for lower operating and maintenance costs.
- FlowDrya and Heatex equipment is tailored to the customer’s requirements; climate, energy supply, biomass input and more are all carefully considered.
- Stronga biomass drying equipment is fitted with a ‘DryStation™’ HMI, allowing operators to easily adjust parameters to achieve the desired output moisture content for the gasifier.
- Compact, space-saving, modular design with optional fixed and hydraulic roof systems available for external positioning.
- Hydraulic PulseWave™ system (see below) continuously agitates the material on the drying bed, ensuring the output biomass is uniformly dried. Belt dryers operate at a very shallow depth and there is no agitation of the material load.
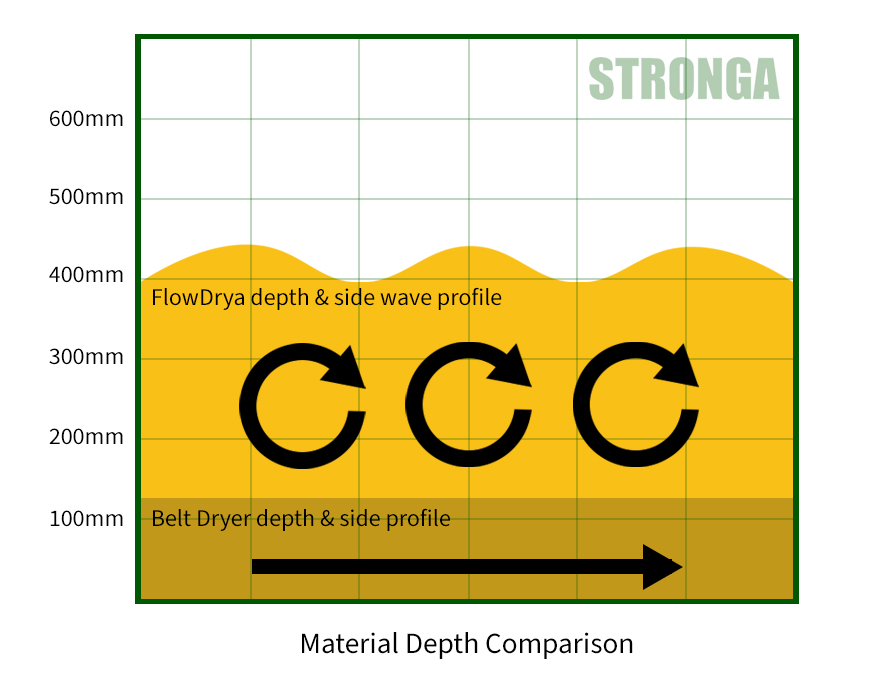
Become Energy Secure Today
Stronga’s continuous biomass drying systems work synonymously with gasifiers to produce clean syngas outputs for electric, energy, heat and power production. Consult Stronga to begin your clean energy production journey today. We look forward to hearing from you.
Bibliography:
Francois J, ‘Detailed process modelling of a wood gasification combined heat and power plant’.
Mishra, Somya, Rajesh Kumar Upadhyay, ‘Review on biomass gasification: Gasifiers, gasifying mediums, and operational parameters’.
Svoboda Karel, ‘Integration of biomass drying with combustion/gasification technologies and minimization of emissions of organic compounds’.
Share this post