The purpose of this article is to discuss the significant issues and inefficiencies associated with on-floor drying systems in comparison to the improvements offered by the better developed, more intelligent and modern FlowDrya continuous dryer from Stronga.
On-floor drying has been a popular choice over the years, especially with farmers, as they have many years’ experience drying cereal grains using on-floor dryers. From our experience, we have recognised that clients often under-estimated the differences between drying grain and wet woody biomass using on-floor systems.
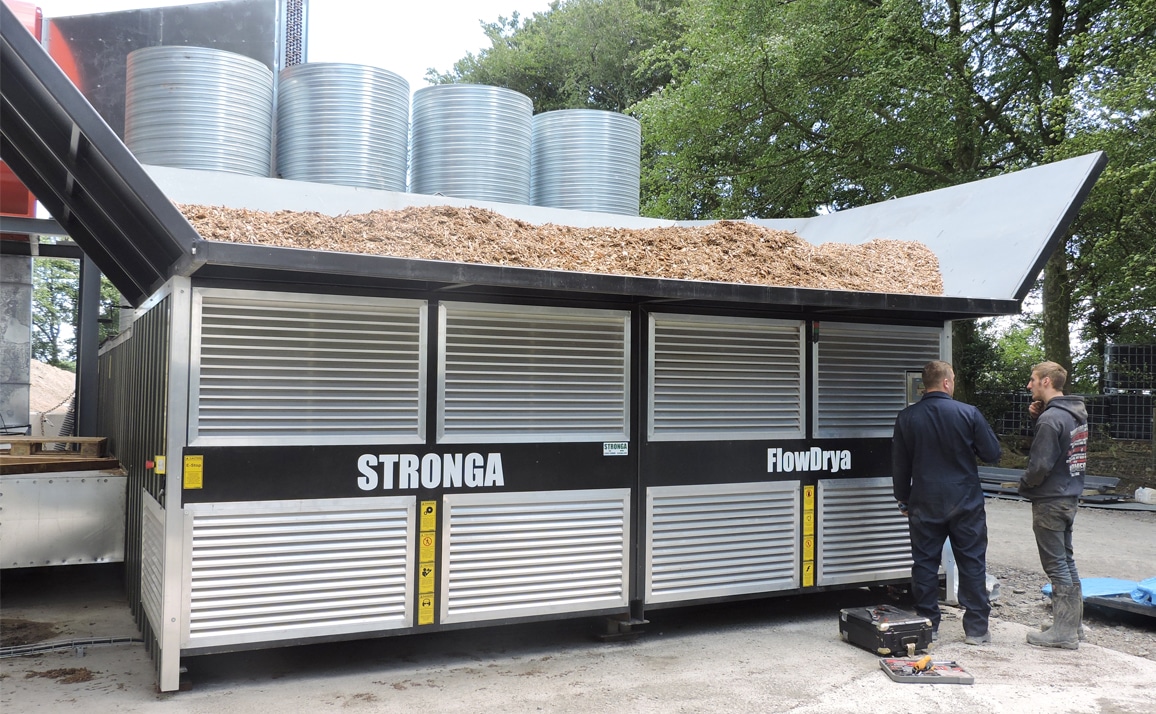
Common Misunderstandings
The common misunderstandings that we believe clients often make when choosing a woody biomass drying solution are as follows:
• Clients often over-estimate the depth at which they can dry woody biomass; and the associated issues of re-condensation and drying fronts.
• Clients often under-estimate the amount of handling that on-floor drying systems bring. Unlike the FlowDrya which can be automated, on-floor drying is highly manual (more information further into the article).
• Clients often under-estimate the amount of fuel and labour hours used in operating and maintaining an on-floor drying system.
• Clients often under-estimate the need for agitation when drying any material, particularly woody biomass. The only way of agitating the load in on-floor systems is through using a loader bucket which adds more cost and complexity.
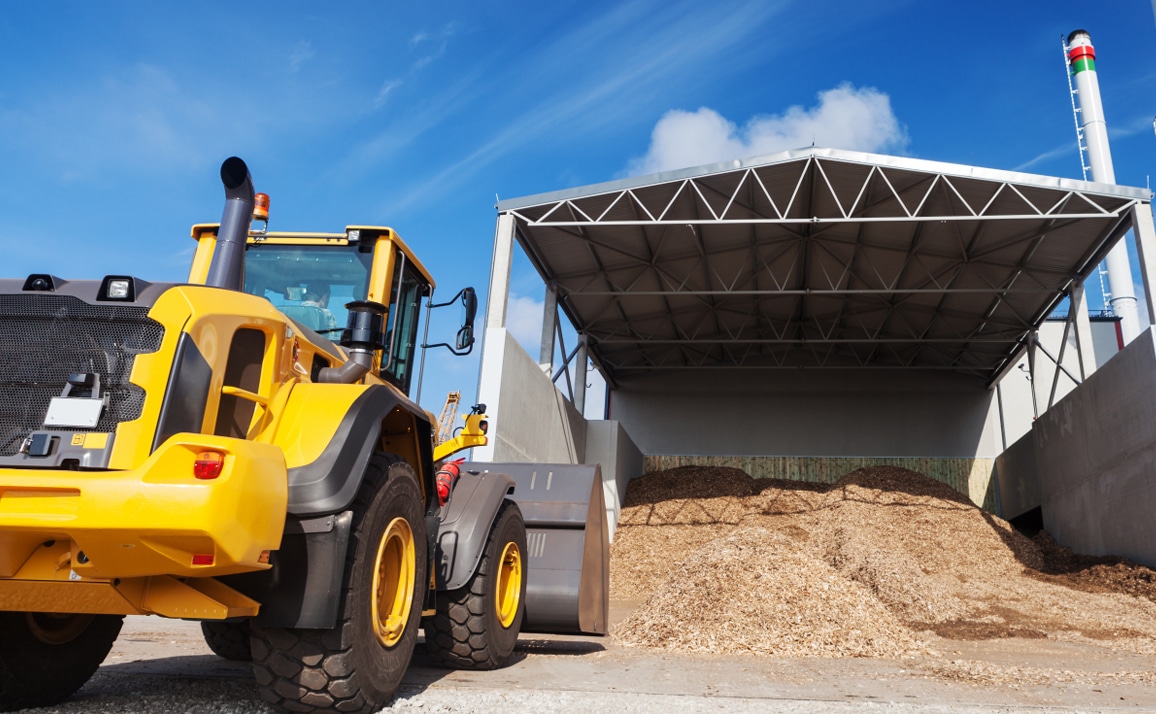
• Clients often over-estimate the drying efficiency of on-floor drying when these systems are largely in-efficient.
• Clients often under-estimate the amount of moisture to remove from woody biomass materials.
• Clients often under-estimate the losses in the ducting and flooring arrangement of on-floor drying systems.
• Clients often under-estimate the amount of space required for the installation – the outside space, the drying corridors, the ducting arrangement, and the drying floor space.
The compounding effect of the above factors results in a highly inefficient operation for drying woody biomass when compared to the FlowDrya.
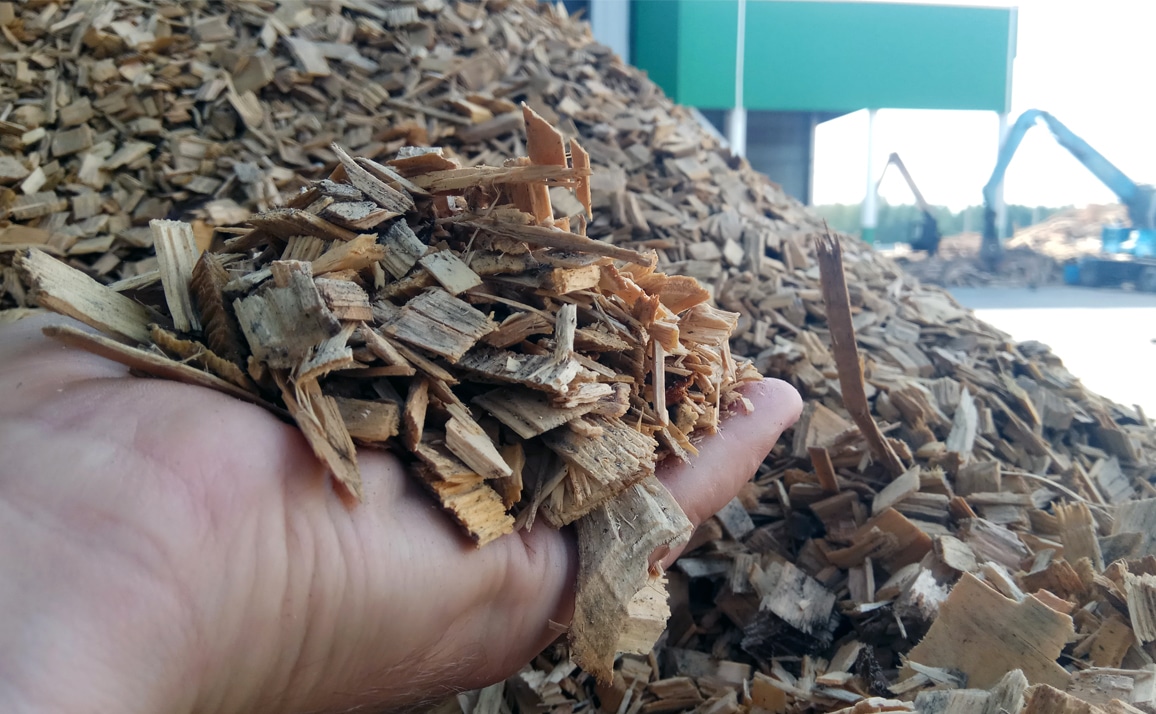
The Material to be Dried
Stronga have recently been discussing the potential of the FlowDrya with a client who has two distinct types of material which are currently dried in separate bays on an existing drying floor arrangement. The two material types are whole log chip and arb chip.
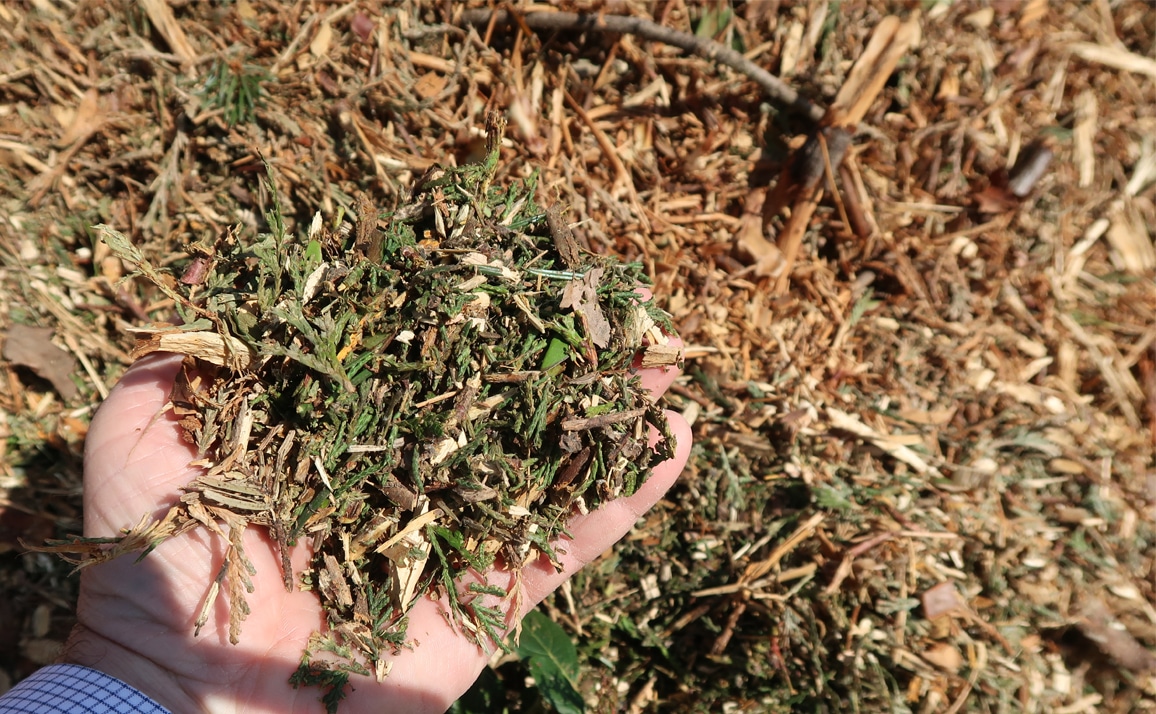
Material Handling Issues
The client described to us the excessive time and cost of loading and unloading the drying floor with the chip material.
In an attempt the reduce handling time and costs, the client increased the depth of material on the drying floor from around 600mm to 1100mm but this had the unintended consequence of causing other issues of re-condensing which increases drying time and reduces drying efficiency while causing more uneven drying in the pile. When all things were considered, there was no way for the client to reduce the excessive handling costs.
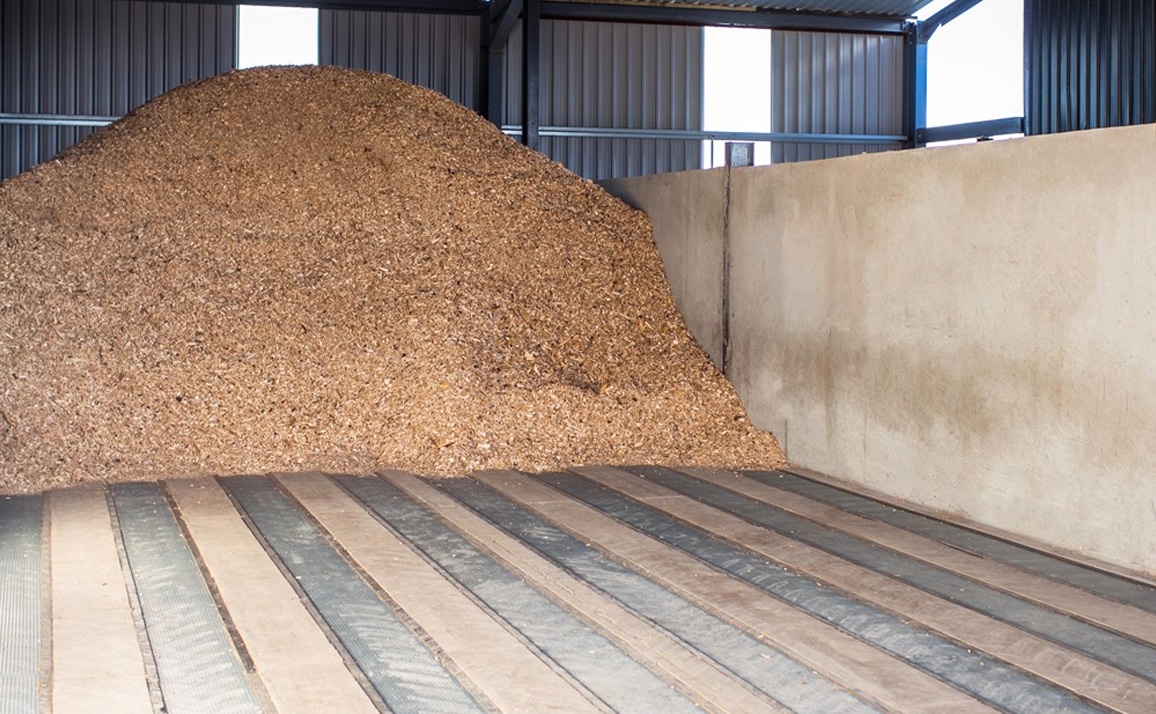
Material Handling Costs
Together with the help of Stronga, the client understood that his current handling cost was approximately £400 per exchange of material. The overall calculation was as follows:
• 10 hours to empty / refill each whole shed (material circa 1100mm deep).
• £40 per working hour with fuel, machine costs and labour all accounted for.
• 10 hours x £40 = £400 per exchange of material every 4 days on average (the client confirmed 2-3 days on the best bays of log chip and 5-6 days on the worst bays of arb chip).
• Using the 4 day average, our client was emptying and refilling material 92 times per year at a cost of £37,000.
• £37,000 is the annual cost for on-floor exchange handling costs, alone. Additional costs and issues are discussed further down this article.
What’s more, the issue of handling was made worse in this particular case by the distance in the yard from the chipping area to drying shed location and back to screener and then to the dry material storage shed.
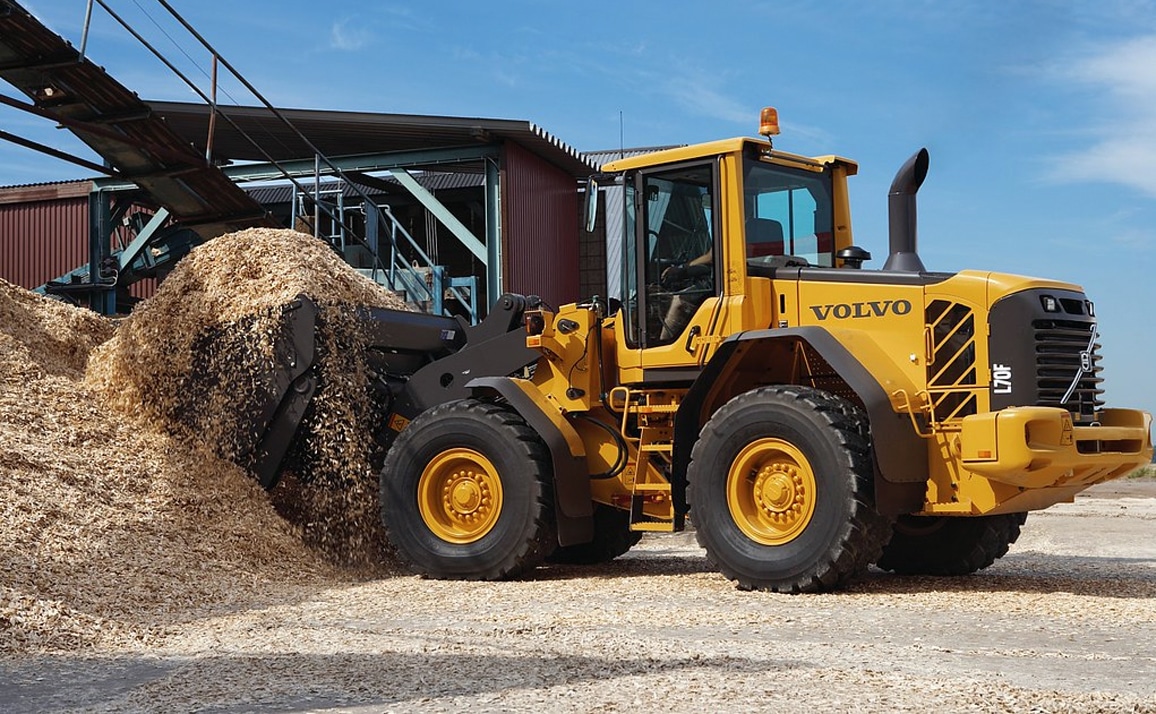
Energy Efficiency
While energy efficiency is harder to calculate than the handling costs discussed above, in our view, this client who is currently drying woodchip is experiencing the following losses with his on-floor biomass drying system:
1. Invisible losses in heating the uninsulated, large-scale concrete ducting which acts as a huge radiator. Stronga were able to produce a thermal camera survey to show the heat loss visually.
2. Losses from the un-even airflow in the ducting and drying floor laterals due to:
• Ducting arrangement and floor distances. The client confirmed that the drying bay closer the Heatex (fan coil heat source) end is drying faster due to increased airflow, coupled with the cooling effect of the drying floor furthest away from the heat source.
• Mixing different materials on the same drying floor (log chip and arb chip) imposes different back pressures. More air flows through the more open log chip material, causing uneven drying between materials.
3. Re-condensation – the effect of re-condensation on kWh per litre evaporated is easy to underestimate.
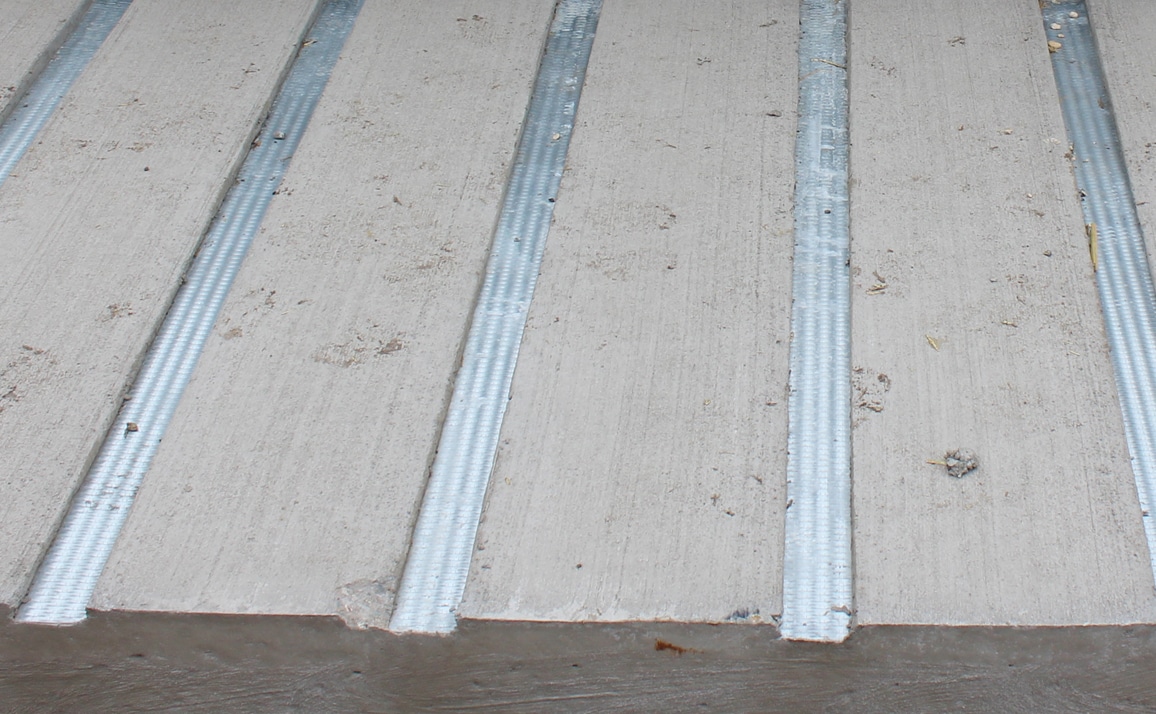
Fresh Arb Chip Bulk Densities
The fresh arb chip bulk density measured on the client’s site varied in the pile depending on the leaf material content. The bulk density was observed to be around 300kg per m³ on a dry day. The arb chip on top of the on-floor drying pile measured 390kg per m³ - therefore we can see 90 litres of moisture had been absorbed into the layer at the top of the arb-chip floor drying pile.
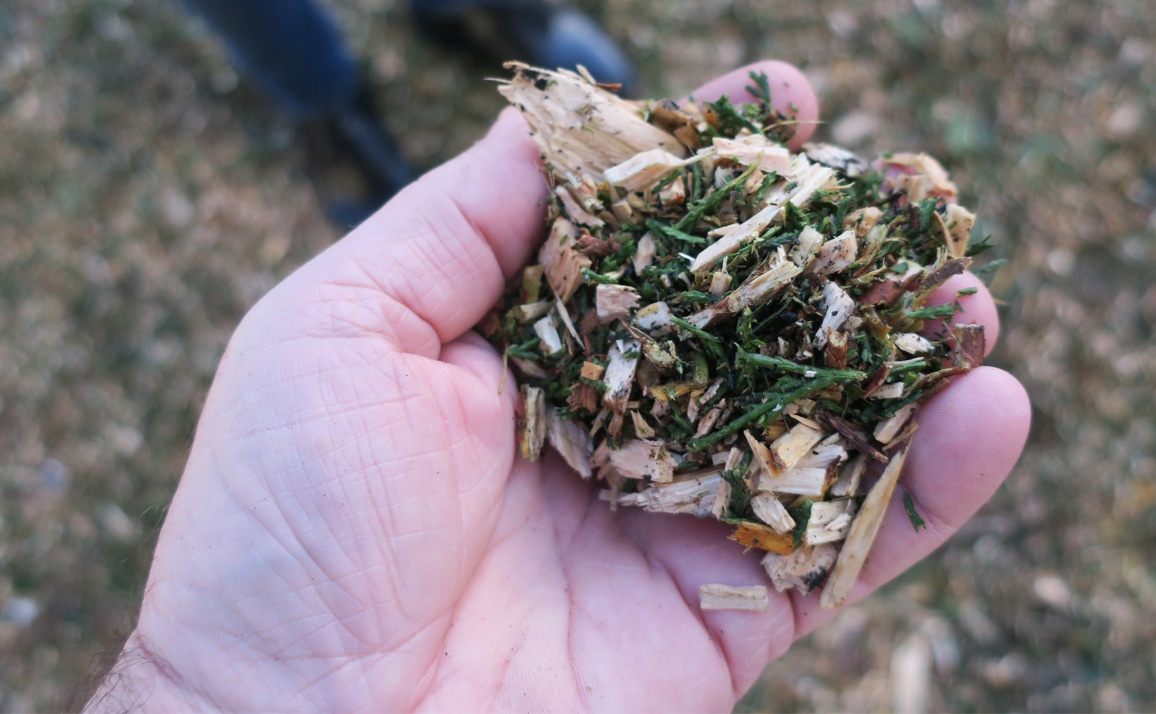
Re-Condensing “Fronts” Effect
This re-condensing “fronts” effect could be reduced by reducing the depth; however that brings large added handling costs. In an on-floor pile, drying and re-condensing can happen several times as the material dries. Invisible “fronts” can occur at 300-400mm depending on a lot of factors such as airflow, air temperature and ambient air humidity.
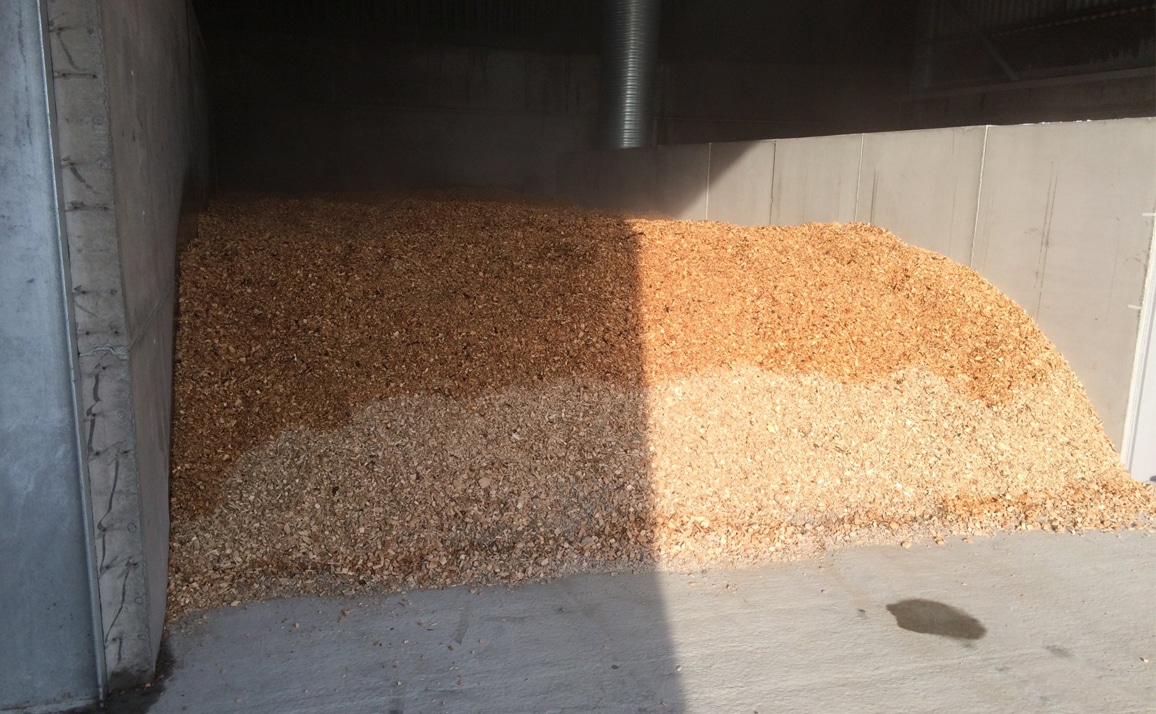
Space Efficiency
Another cost which is not so easy to calculate is space efficiency in drying. This client currently has 4 x 144m² drying bays with 2 additional loading bays. We estimate the drying floor accounts for 720m² of space in total, plus outside yard space for access. In comparison, the modular Stronga FlowDrya can sit outside and occupies only 40m² (depending on model choice) - this is 18X less space for an equivalent scale flow dryer.
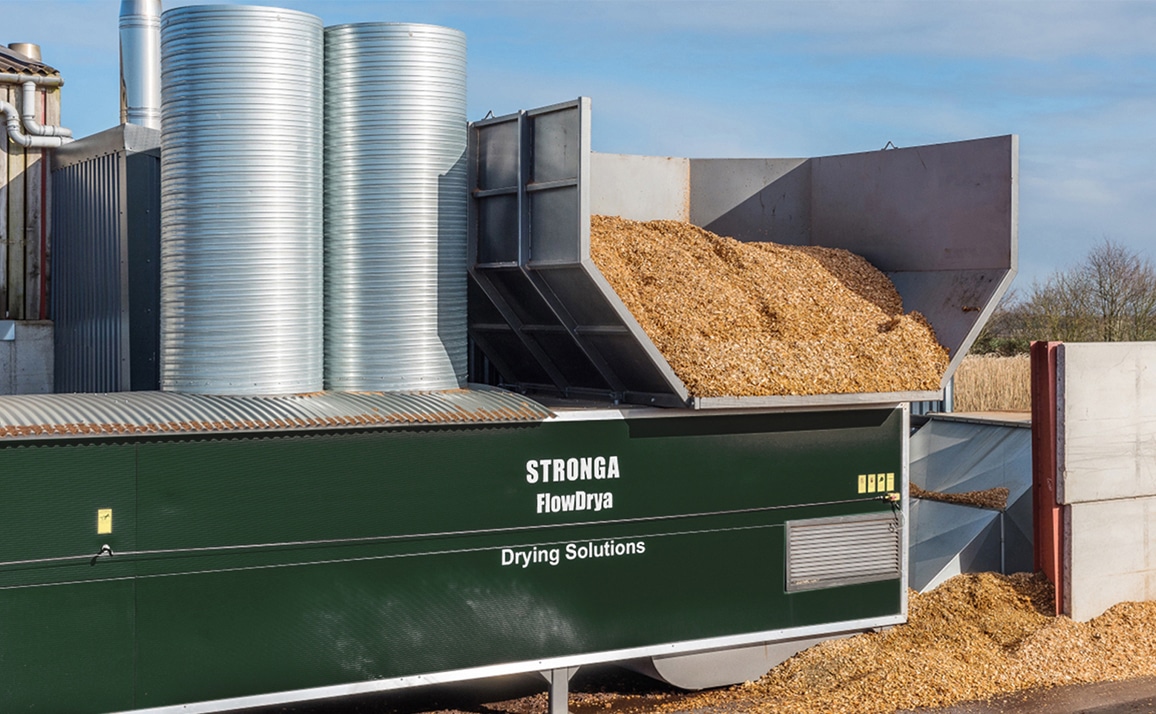
Control of Drying
Another area to consider when choosing your drying solution is the control of drying. With all the issues of uneven drying, on-floor dryers pose a significant issues of when to stop the drying process. This often leads to over or under- drying with the consequent economic issues of:
• Over-drying = wasted energy and time and reduced drying output. Lost potential dry material and income. These costs add up over the years.
• Under-drying = failure to meet the onward client’s moisture % target specification for fuel with the associated costs (this effect can be reduced when selling fuel per kWh).
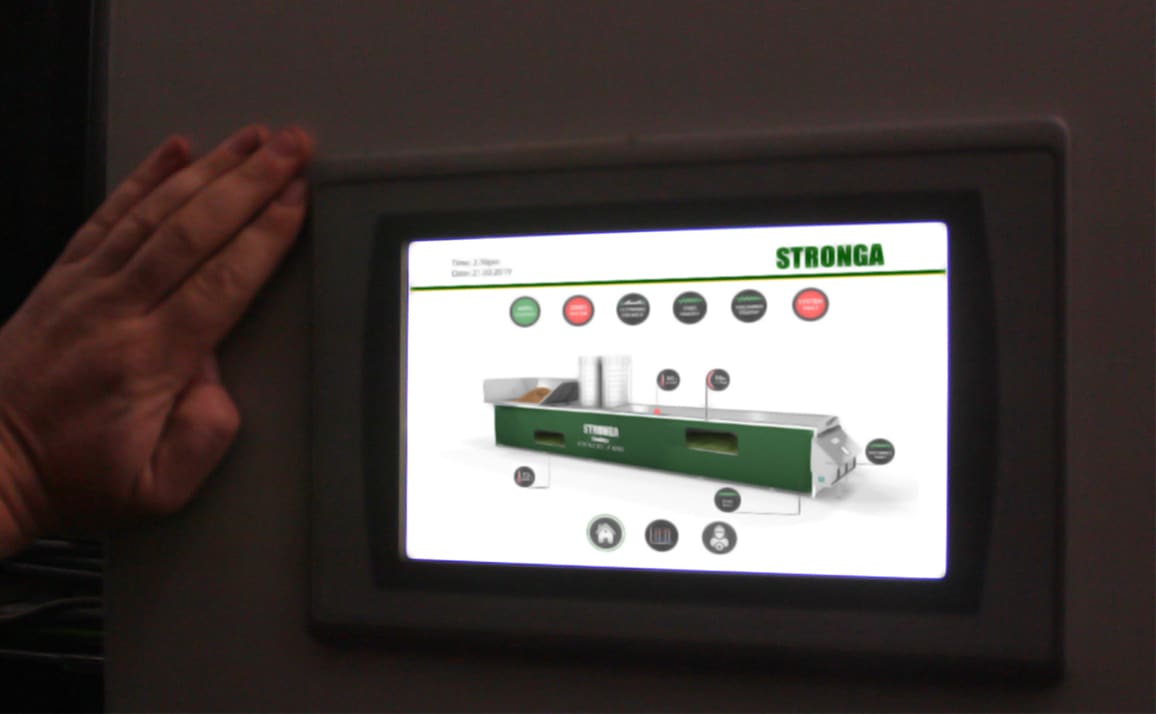
In contrast to the above, the FlowDrya allows much greater control to increase or decrease PulseWave™ drying bed strokes per hour depending on conditions to achieve consistent target moisture output. Drying fronts are avoided with material agitation a key feature of the FlowDrya with the PulseWave™ drying bed. See the video below for more information about material agitation.
Highly Economic Drying Solution
With all things considered, the FlowDrya continuous dryer offers a highly economic drying solution, bringing multiple benefits to various drying operations compared to on-floor systems.
• Significantly reduced handling time costs compared to on-floor drying.
• Reduced fuel and loader operating hours compared to on-floor drying filling and emptying.
• Ability to locate the modular drying operation close the chipping and screening operation and bunker housing as part of the reduction in handling cost.
• 2-3X increased output from the same thermal energy and electrical use.
• More even dry output compared to the on-floor drying re-condensation “fronts”.
• PulseWave™ agitation of the material, every single stroke, offering uniformly dry output, every single day.
• Far better control of dry output using intelligent, integrated control systems, optimising the capacity of the dryer.
• Opportunities to automate onwards processes via conveyor handling dry material off the FlowDrya plus potential for automated screener loading and bunker loading.
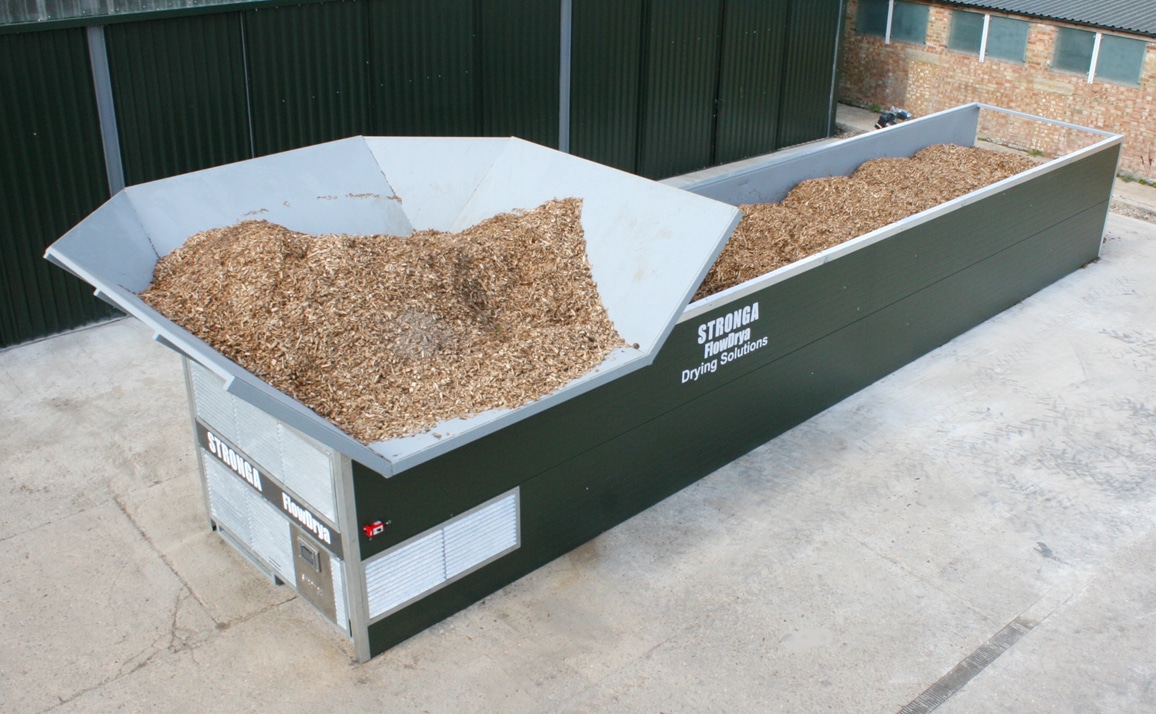
Respect the Resource
When compared to on-floor drying, the business case for FlowDrya is highly compelling for many woodchip drying operations and applications. Contact our technical today for more information. We look forward to hearing from you.
Email – sales@stronga.co.uk or call – 01992 519000
Share this post