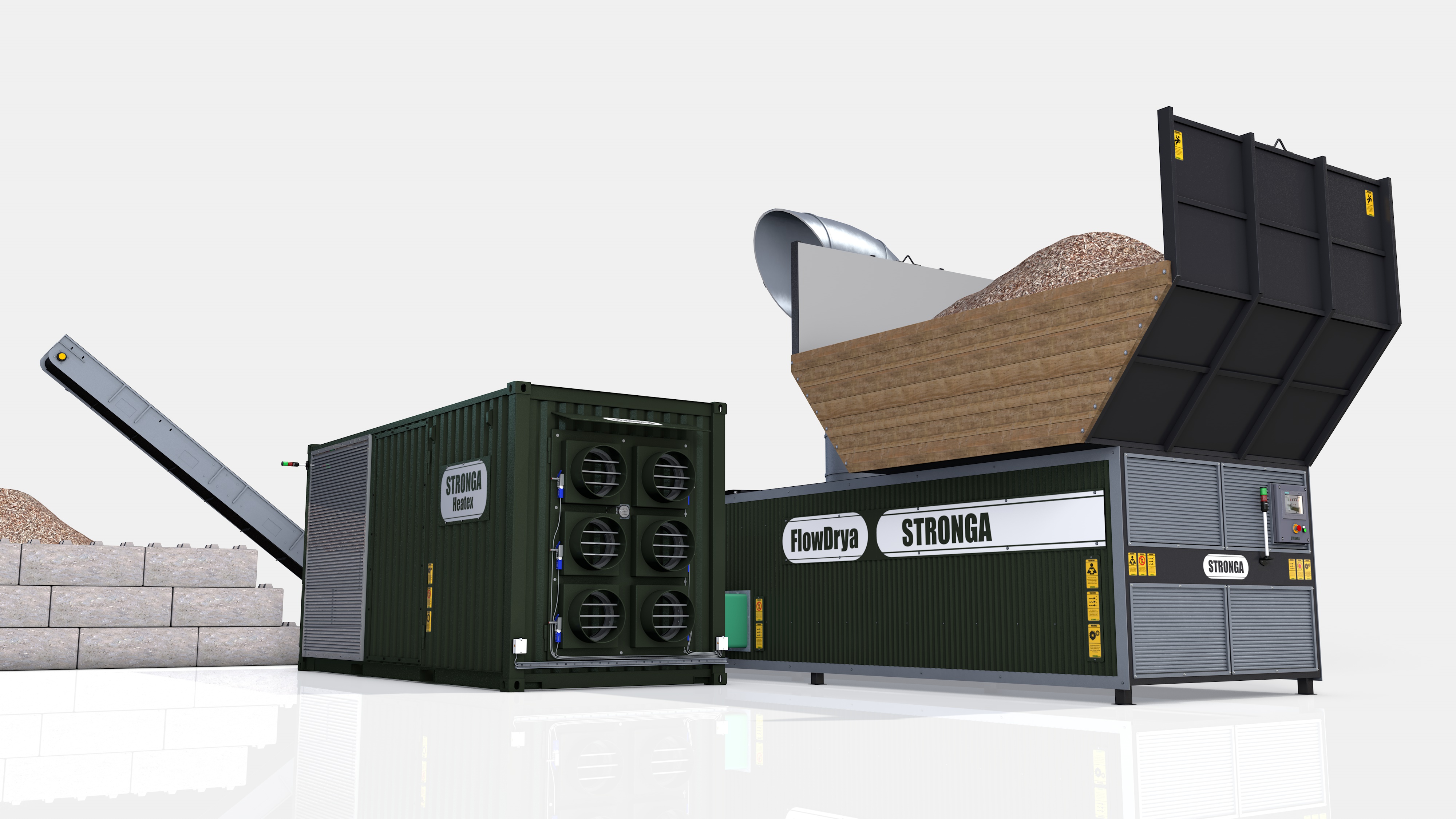
Reliable. Efficient. Well-proven.
FlowDrya drying solutions from Stronga are modern, energy efficient, highly reliable and well-proven in drying a wide range of wet materials. FlowDrya features all the attributes our customers require from a continuous- drying system.
Wide range of models offering high-capacity output ✔; Excellent thermal & electrical efficiency ✔; Long service life ✔; Stunning reliability ✔; Extremely low service costs ✔; Intelligent, easy-to-operate control systems ✔; Uniformly dry output with PulseWave™ mixing motion ✔; High-capacity infeed hopper – minimising labour costs ✔; Ability to dry wood chip, forage, paper pulp & more ✔
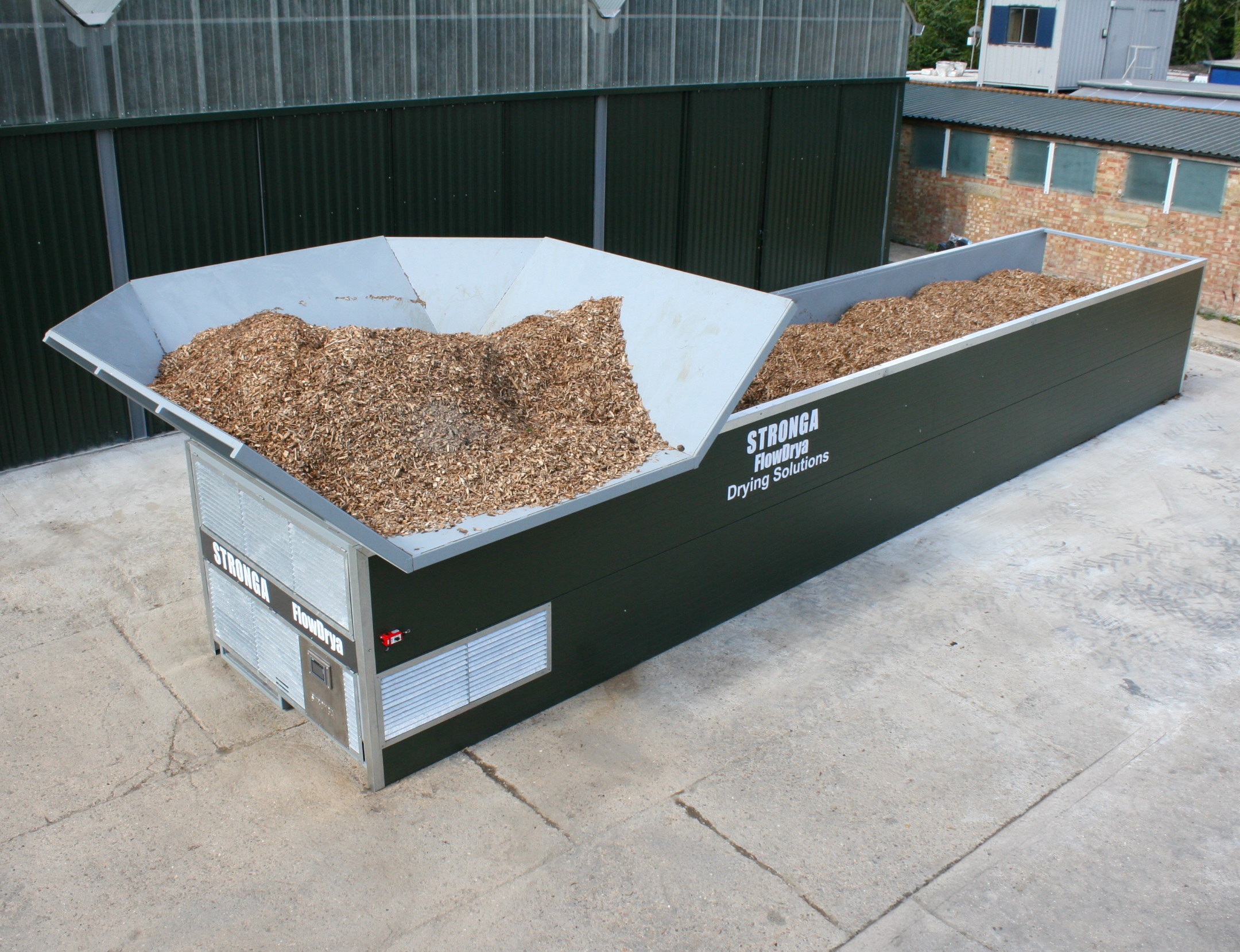
Tailored drying solutions
There are endless lists of wet materials that need to be dried to allow onward processing and utility. Some materials require specific handling during the drying process, others require tight regulation of drying air temperature and the value of others may be increased with minimal cost and by using waste heat only. FlowDrya is one of the only continuous drying solutions available in the market offering the flexibility to cope with the varying properties of different wet materials.
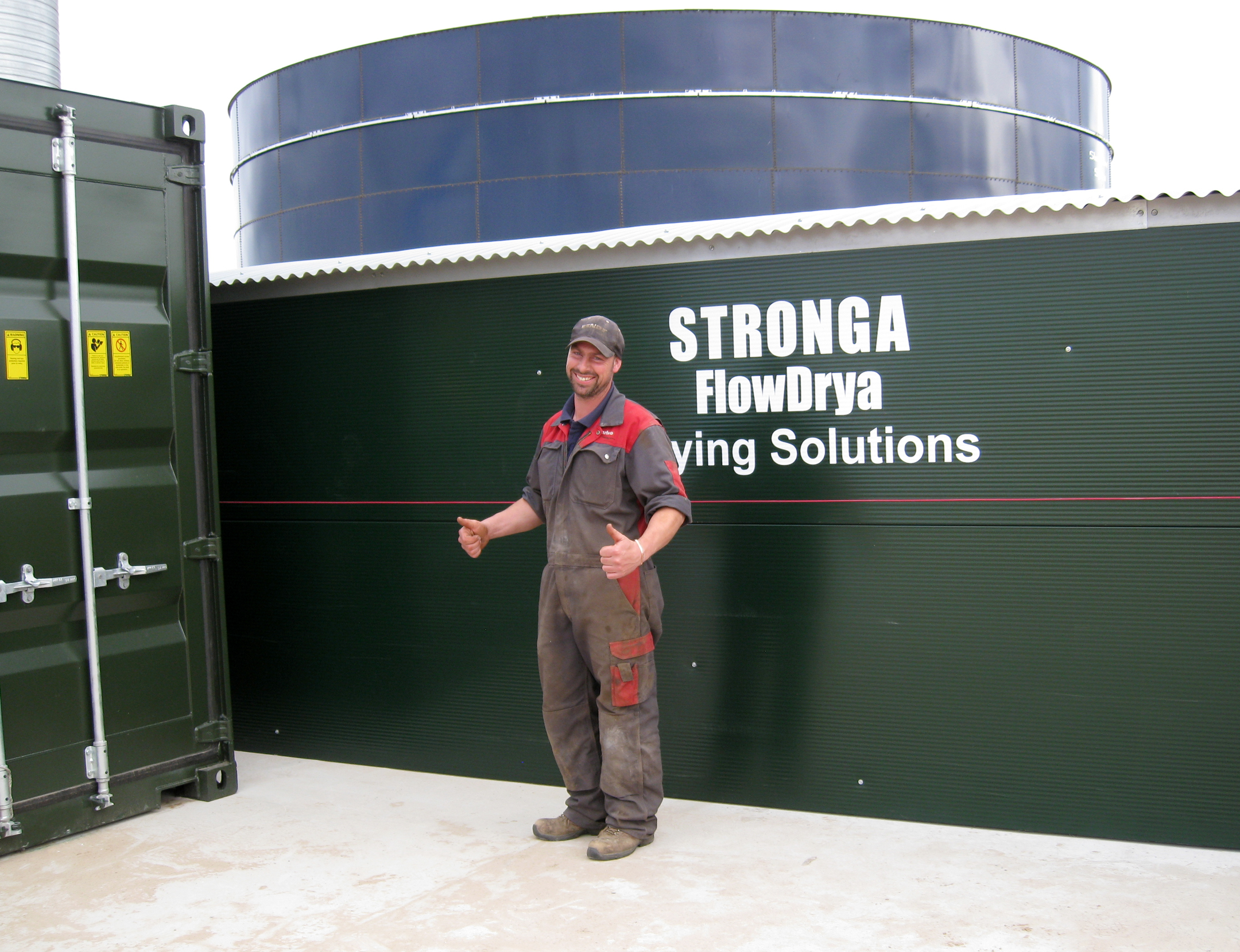
Think flexibility. Think FlowDrya.
With intelligent consideration of your material, location and available heat source, we are able to offer customers optimised solutions to maximise value from the flow drying process. The flexible FlowDrya system enables unlimited drying potential, leading to long term financial profitability and productivity. Operators should be aware that performance variations may occur if they choose to dry materials other than the one agreed in writing at point of purchase.
TIMBER INDUSTRY
AGRICULTURE
PAPER & PULP INDUSTRY
WASTE DISPOSAL & RECYCLING
FEED INDUSTRY
FUEL PELLET INDUSTRY
Simplicity is paramount
Every Stronga product is designed to comply with our core principle of building simple, reliable, easy-to-operate machines. The FlowDrya continuous dryer positively moves wet materials from a hopper (end loaded or top deck), along a hydraulic-powered moving floor and over a flow of temperature-controlled drying quality air, fed from a variety of efficient, optimised heat sources. Simplicity is paramount with FlowDrya.
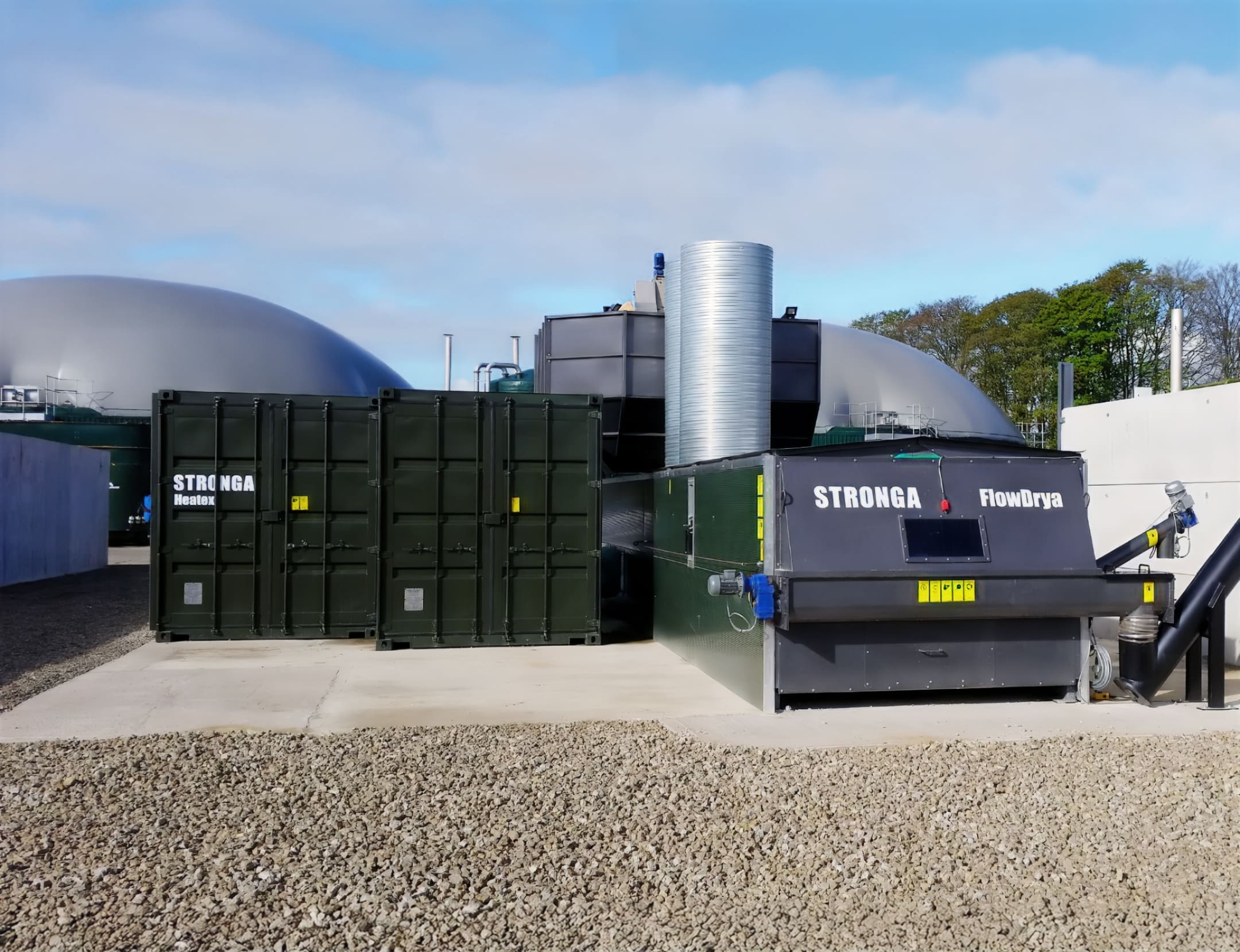
Effortless drying operations
FlowDrya operations are incredibly simple yet extremely effective in helping you achieve your goals.
Processes can be fully-automated with conveying systems and augers regulating the flow of material into the dryer’s hopper and away from the dry output end. This ensures energy-use efficiency is optimised and production is maximised while closely observing the required final moisture content of the dry output.
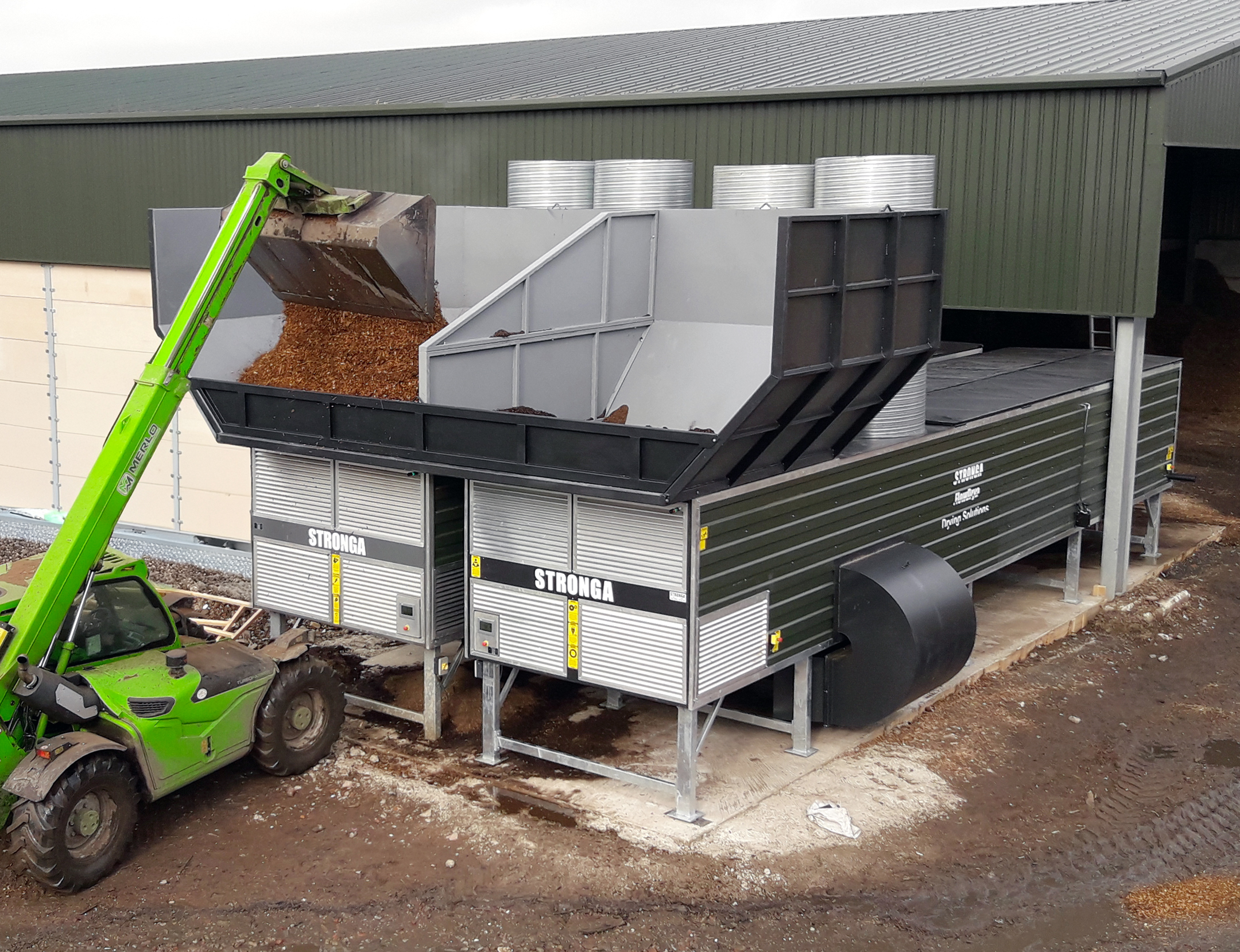
The drying force behind value
Low Capex – FlowDrya offers excellent value for money at point of purchase. The Stronga technical team consider the whole business case for each project to ensure we offer optimised drying solutions for maximum value.
Low Opex – When compared to other solutions, FlowDrya offers the lowest energy cost per operating hour. What’s more, automatic mode controls (with moisture monitoring), automatic discharge and extended periods between refilling minimise expensive labour hours.
Low Ownership costs – FlowDrya offers extremely low ownership costs from fully considered component quality which ensures maximum uptime, optimum productivity and low service costs. Our reputation for quality-built equipment provides customers with strong residual values and a low cost of ownership.
Cost-effective drying solutions
Cost-effective drying solutions
Drying with warm air
FlowDrya is able to rapidly raise materials to an evaporative temperature because drying occurs in 2 ways; through (1) air drying and; (2) thermal conduction. Injecting drying quality air through wet materials as they roll, tumble and flow along the hydraulic bed optimises the evaporative drying process to reduce moisture content evenly to the client’s requirements. Learn the process.
(1) Drying quality air is delivered by the Heatex unit. Heatex can utilise multiple heat sources, including; low grade residual process heat; CHP engine, water jacket and flue gas heat; biomass boiler thermal output; & more.
(2) Warm airflow heats the insulated steel structure of the FlowDrya sub-floor plenum, conducting thermal energy directly into materials on the drying bed to the supplement air drying process.
(3) Warm air rises through the ventilated floor and through the material. Full length diffusion with intelligent zoning of airflow optimises drying efficiency as the material changes state from wet to dry.
(4) Saturated exhaust air dissipates into the atmosphere via suitably-sized flue ducting, or can be recirculated via modern, well-designed energy-recovery systems.
Drying with thermal conduction
FlowDrya’s unique selling point is PulseWave™ - the automatic agitation of materials as they are continuously tumbled along the moving floor. PulseWave™ ensures that every part of the material receives even thermal conductive contact with the hot drying bed, leading to uniformity of output dryness.
During the forward stroke of the moving floor, materials are tumbled forwards by the pushing blade face, causing a larger driving force low to the bed. The driving force is weaker above the pushing blade, causing materials at the wave’s crest to lag and tumble backwards. In the return stroke, materials are lifted over the tilted axis of the blade to form another wave. As the crest height grows, the wave becomes unstable, causing materials to tumble forwards and backwards, ensuring full agitation on every stroke. Each stroke, materials are displaced from their position which doesn’t occur in belt drying situations; this means that each particle receives equal access to warm airflow and thermal conduction during the process.
DryStation™ control system
Stronga optimise drying outcomes through intelligent and intuitive controls coupled with comprehensive operator training. FlowDrya is designed for continuous operation but drying conditions may change depending on the input material wet basis moisture content, ambient temperature and humidity. Some heat loads also fluctuate in the supply of thermal energy due to various factors.
The DryStation™ control system allows operators to configure set points, incorporating automatic modes which adjust operational factors in line with changing conditions. With the remote access option included, the entire control system can be monitored and controlled remotely using an iPad, iPhone, Android or desktop.
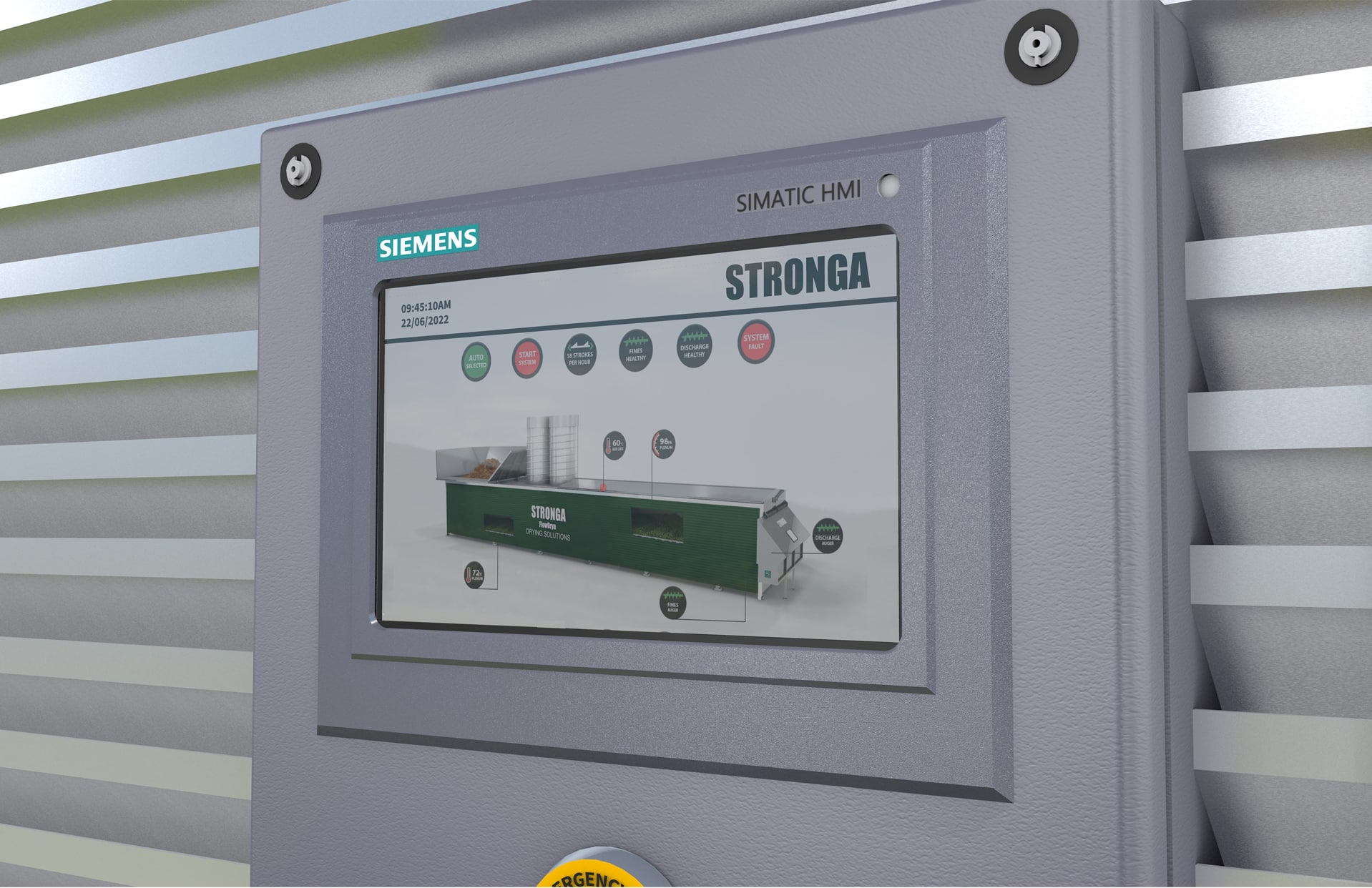
Performance, maintenance & insight
FlowDrya operations are managed by an integrated Programmable Logic Controller which, working in total synergy, maximises efficiency and reliability while reducing management costs. Robust PLC systems, integrated and sealed within the dryer, have durable infrastructures designed to withstand local operating temperature variations. What’s more, FlowDrya’s control systems offer data logging of key parameters, enabling operators to analyse factors and optimise drying operations.
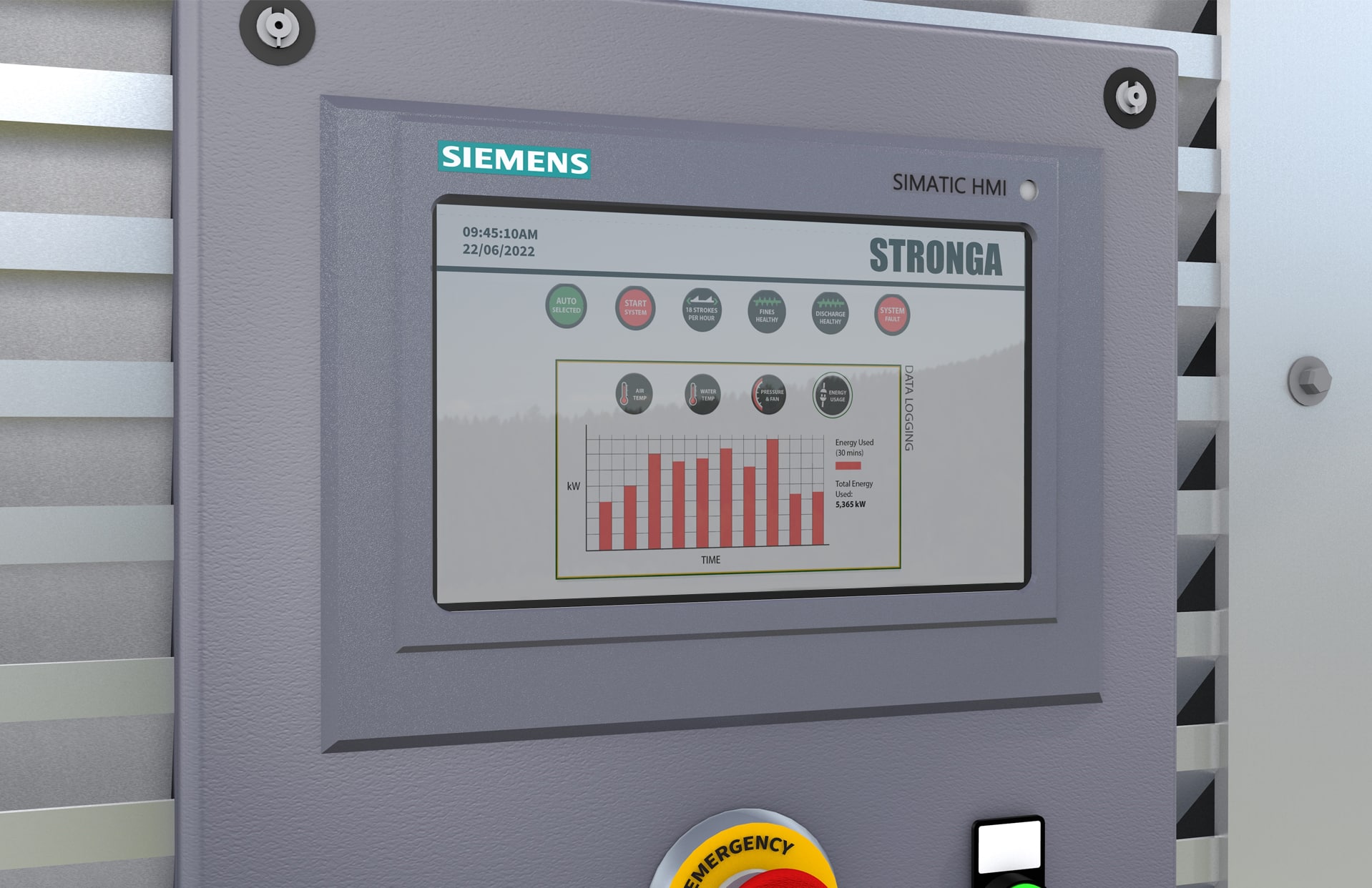
HMI touchscreen interface
FlowDrya’s illuminated DryStation™ HMI touchscreen is the user’s graphical interface between the PLC system and the dryer. The HMI enables instant visual access to the controls, operating and safety parameters, incorporating the following equipment:
High resolution wide-screen colour display ✔; Easy-to-operate graphical user interface ✔; 3D imaging of your dryer with key parameter icons ✔; Energy usage monitoring ✔; Remote access potential (stand-alone control or SCADA integration) ✔; Modern soft-start technology ✔; Explanative fault-finding notifications ✔; Time-stamped data recording for operational analysis ✔
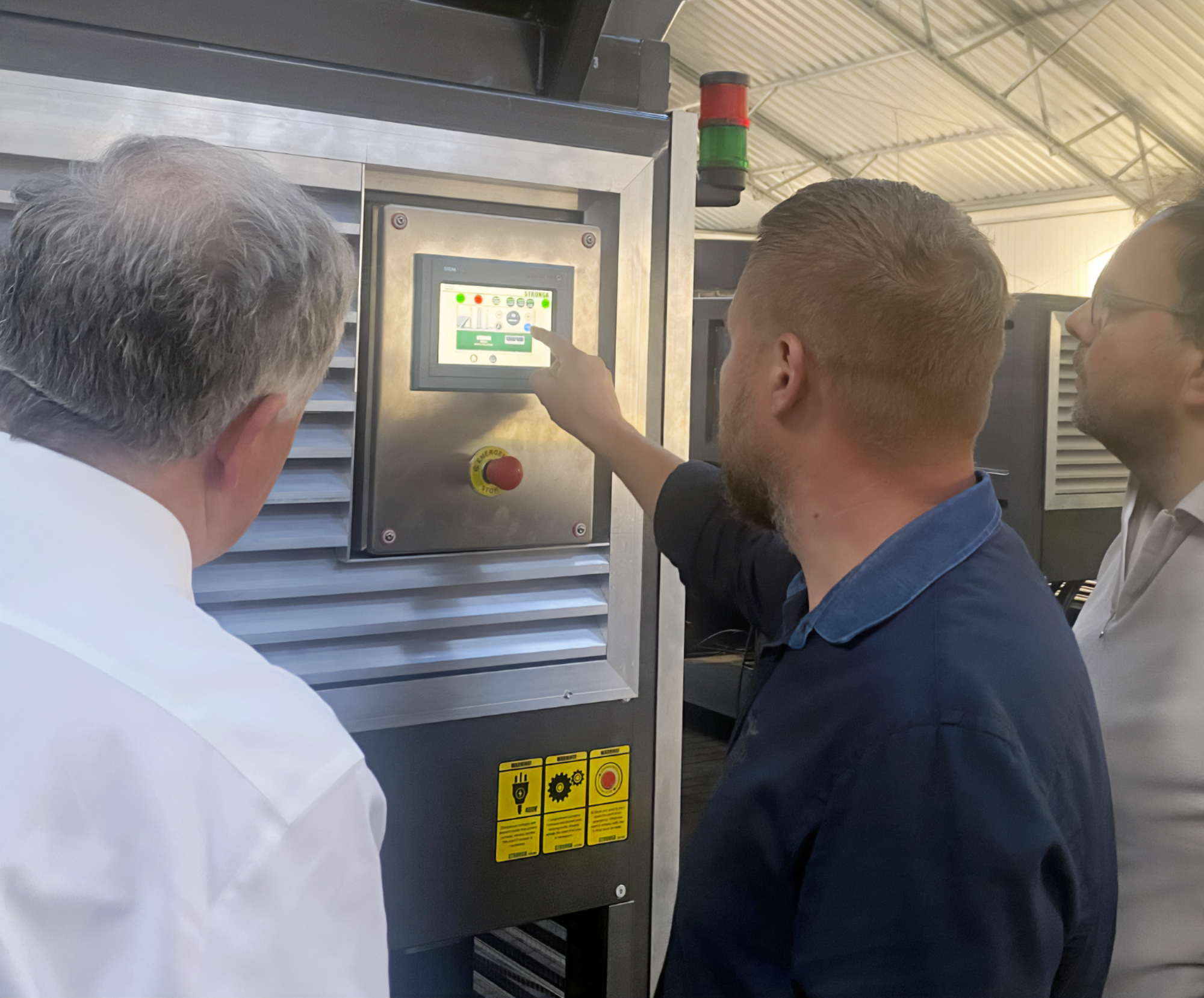
Comprehensive operator training
During the commissioning phase, Stronga work with the designated operator(s) to ensure they are fully trained with the controls, safety, service and maintenance. The comprehensive training procedure is led by an experienced Stronga engineer, ensuring the operating team feel confident to take charge of the continuous flow drying process. What's more, our technical team remain on-hand post-sale to provide expert remote support, if required.
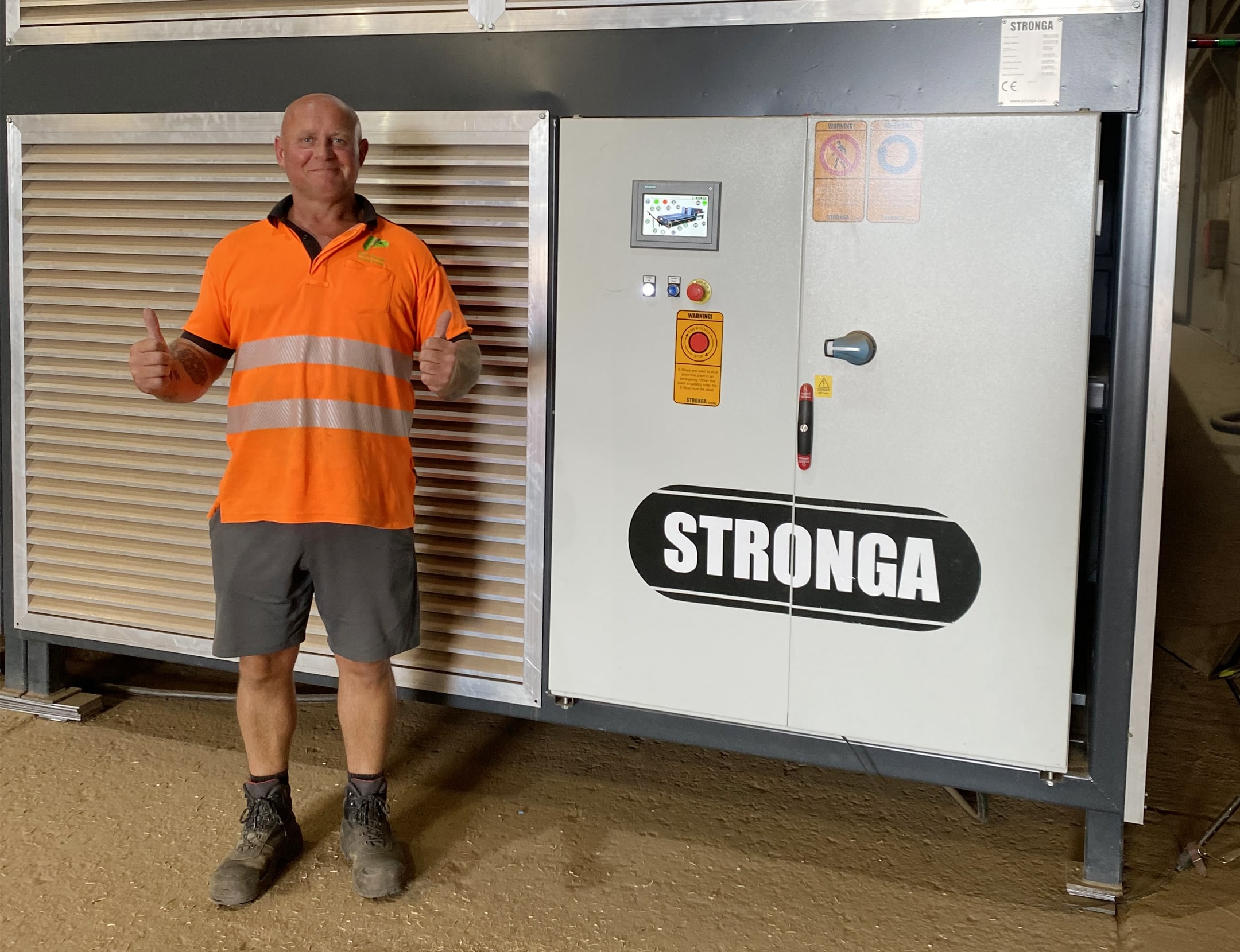
FlowDrya vs. ‘The Other Guys’
Comparing in-feed hopper capacity
FlowDrya has several in-feed hopper arrangements with capacities to the suit the material, customer's requirements, bulk density and moisture to be removed. Through thermal conduction, the in-feed hopper raises material towards evaporative temperature before they reach the drying bed while large cubic capacities maximise loading intervals. ‘The Other Guys’ require complex in-feed conveyor arrangements which make the process labour-intensive and expensive.
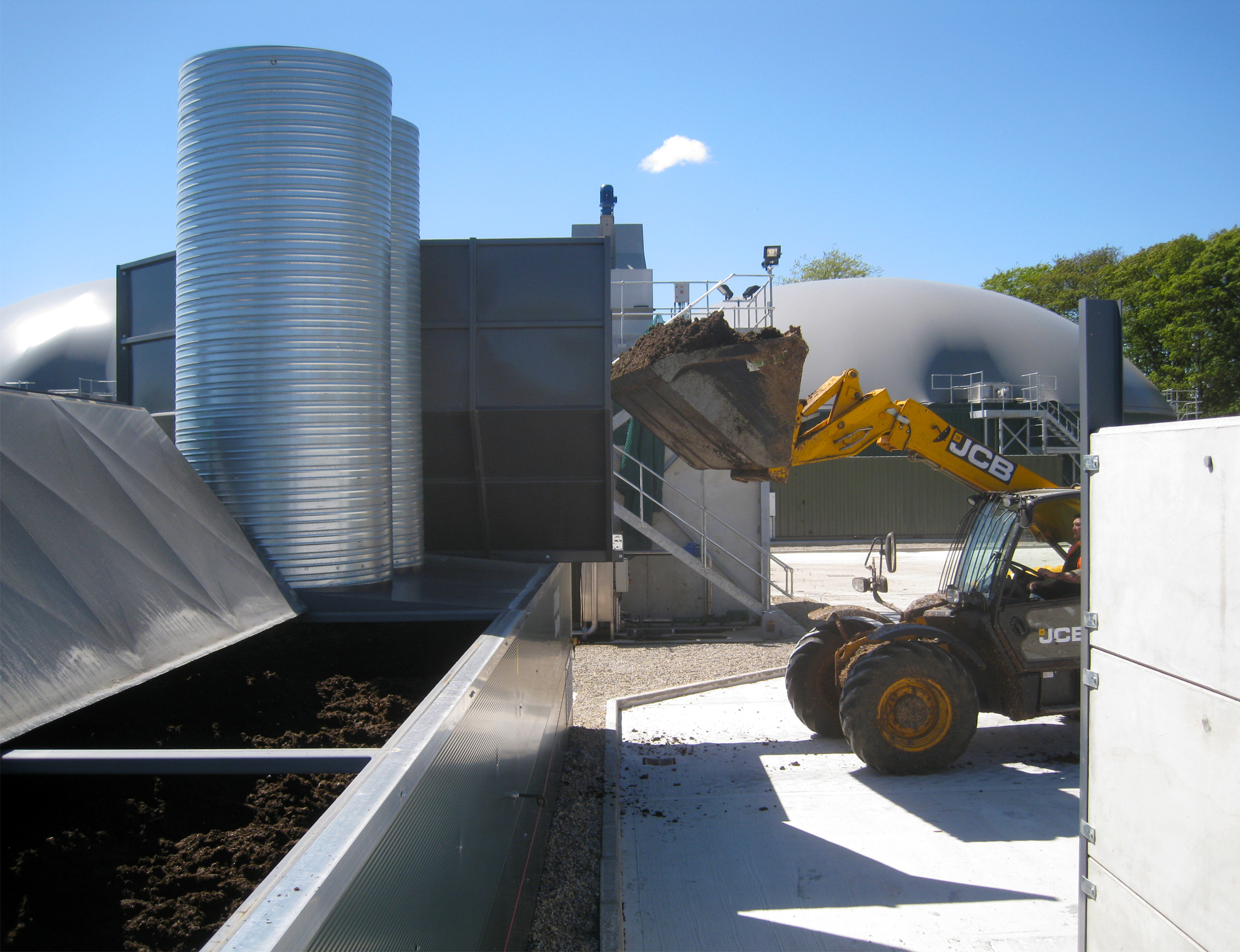
Comparing dry output discharge
FlowDrya actively pushes dry output from height, enabling amble space for above-ground discharge onto conveyors, cross augers or bunkering into a suitably-sized dry store. Simple discharge arrangements aren’t possible with belt dryers which generally discharge very low to the ground.
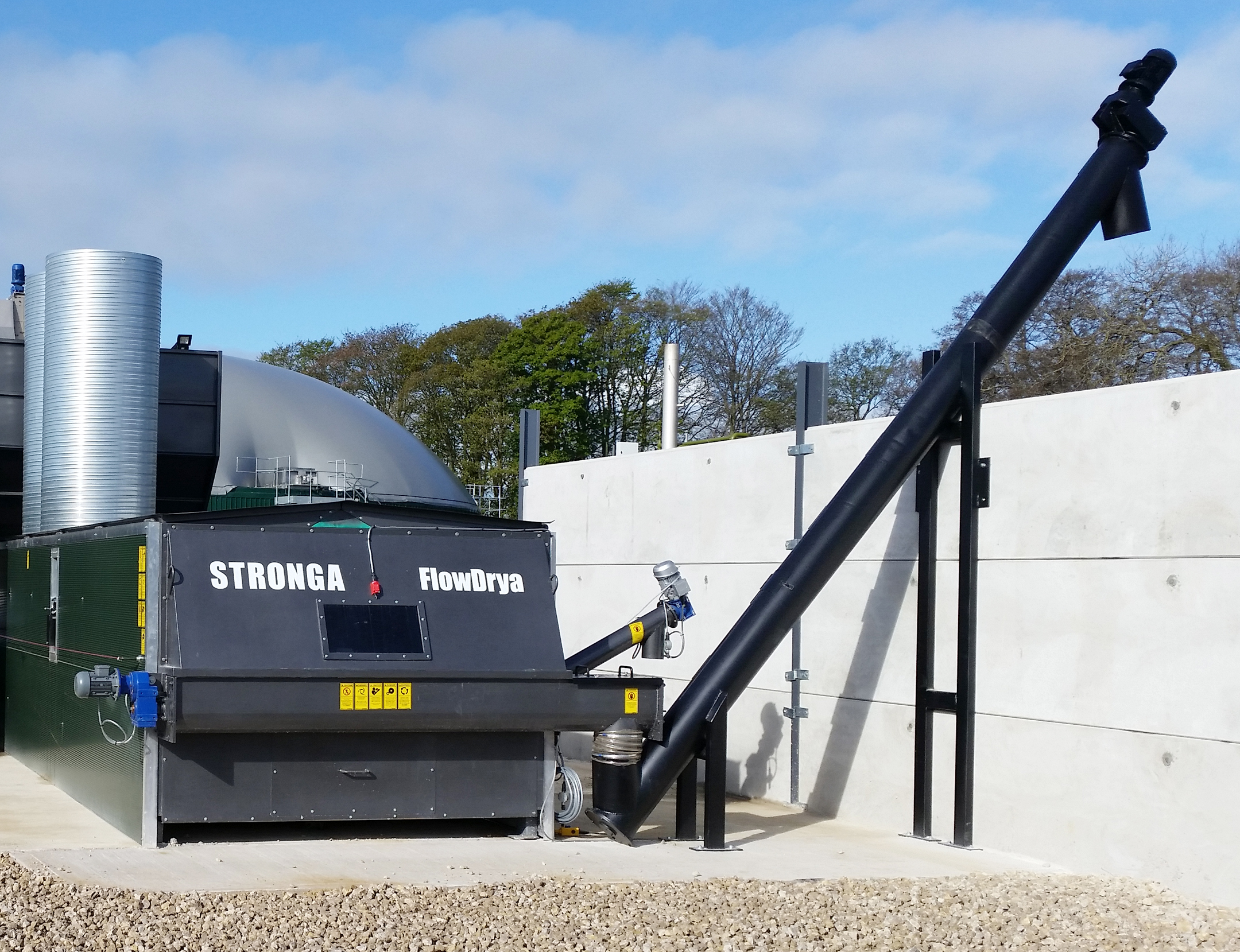
Comparing electrical energy requirement
FlowDrya requires 4-8X less electrical energy than a conventional belt dryer. This adds up to 10s of thousands of pounds / Euros saved every year in electrical energy only. With FlowDrya, the owner can normally use the on-site energy supply whereas belt dryers typically require an expensive extra energy supply to be installed. As well as the substantial extra electrical expense, this is all hassle and logistical hard-work.
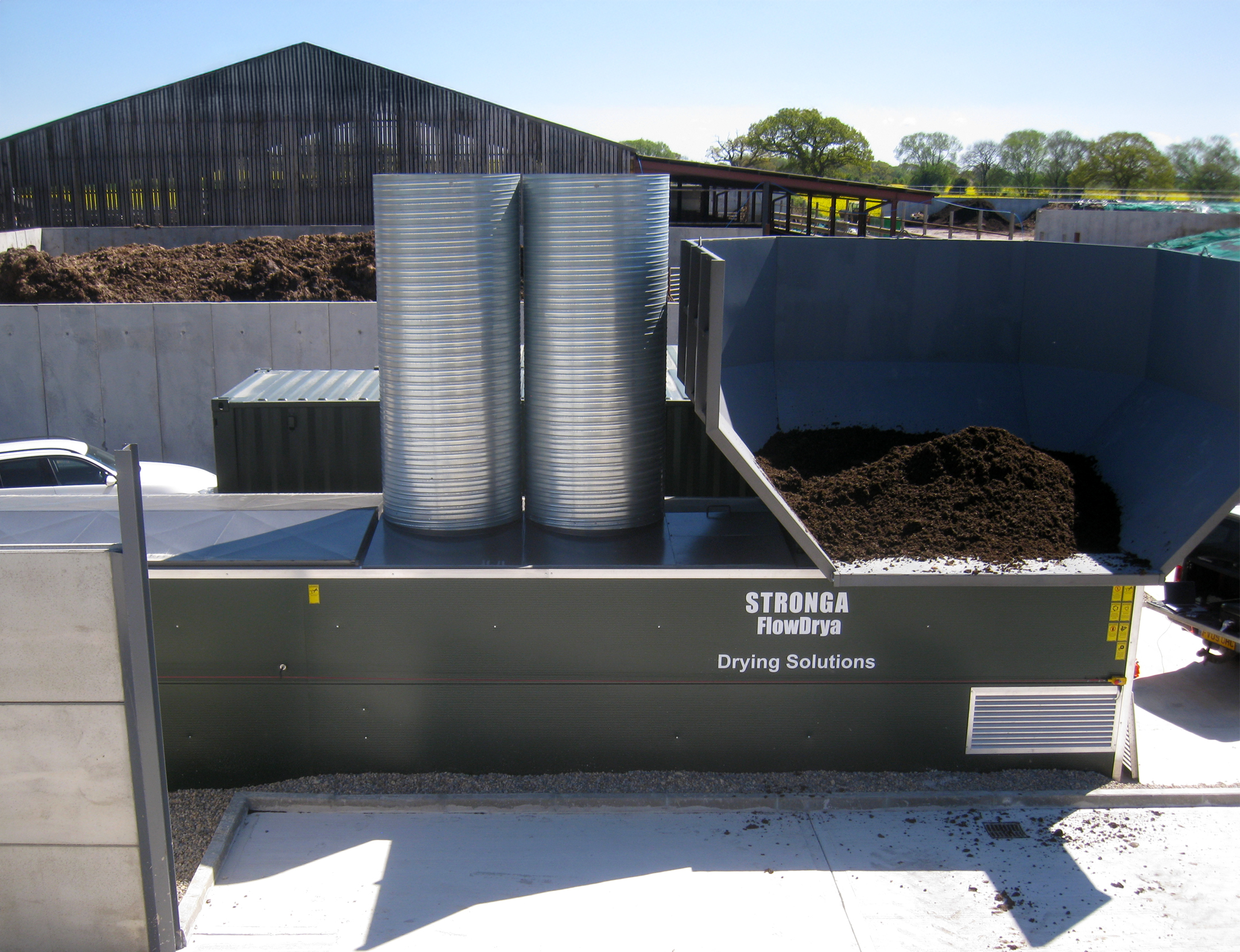
Comparing hydraulic moving floor vs. Moving belt
FlowDrya’s powerful hydraulic moving floor pushes materials of all densities and moistures. Stronga create “airflow zones” to reduce back pressure and minimise dust which improves drying outcomes. In a moving belt situation, the belt has to be constantly cleaned using air, water or mechanical brushes. The belt can slip, stretch and be damaged by certain objects, leading to costly downtime. Air zoning is only possible by adding complexity, maintenance, energy and cost with even more fans.

Comparing drying efficiency
Material in belt dryers is typically slower to reach evaporative temperature because air is the only method of drying while the belt provides high air resistance which is detrimental to the drying process. FlowDrya offers both thermal hot air and conductive drying via the warm stainless steel drying bed. Conductive drying is accelerated by PulseWave™ agitation of the material. All of this means that FlowDrya accelerates material to the evaporation phase faster while the combination of agitation and conductive heat optimises drying efficiency.
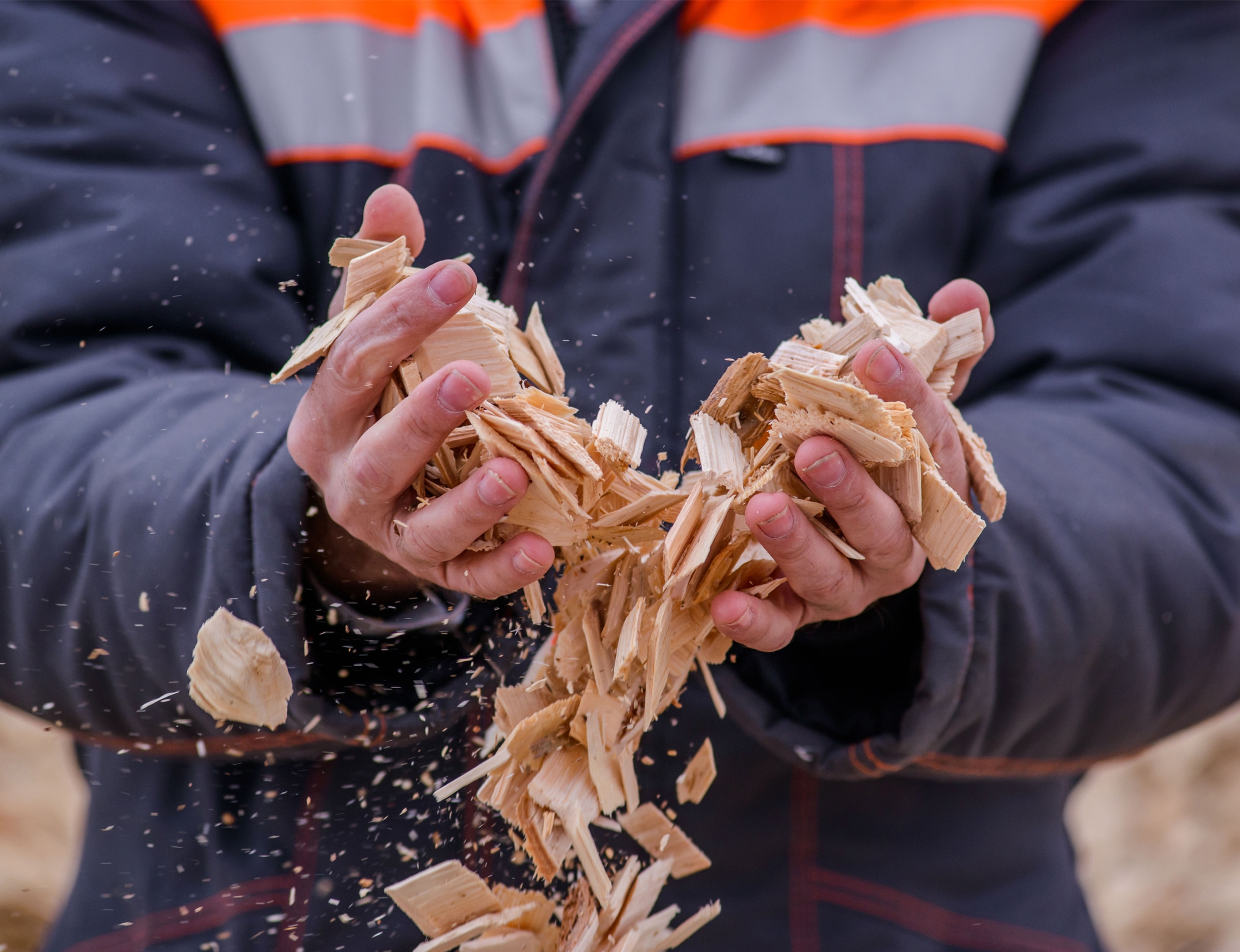
Comparing material agitation
Fully agitating the material during the continuous flow process is vital for uniformity of output dryness. FlowDrya’s PulseWave™ moving floor agitates material every single stroke, without the costs associated with the belt dryer’s separate agitation paddles. Each belt dryer paddle has an associated cost in capital and maintenance terms. They have bearings, shafts, gearboxes and motors which add to the electrical cost, plus they often need replacing in high-duty situations.
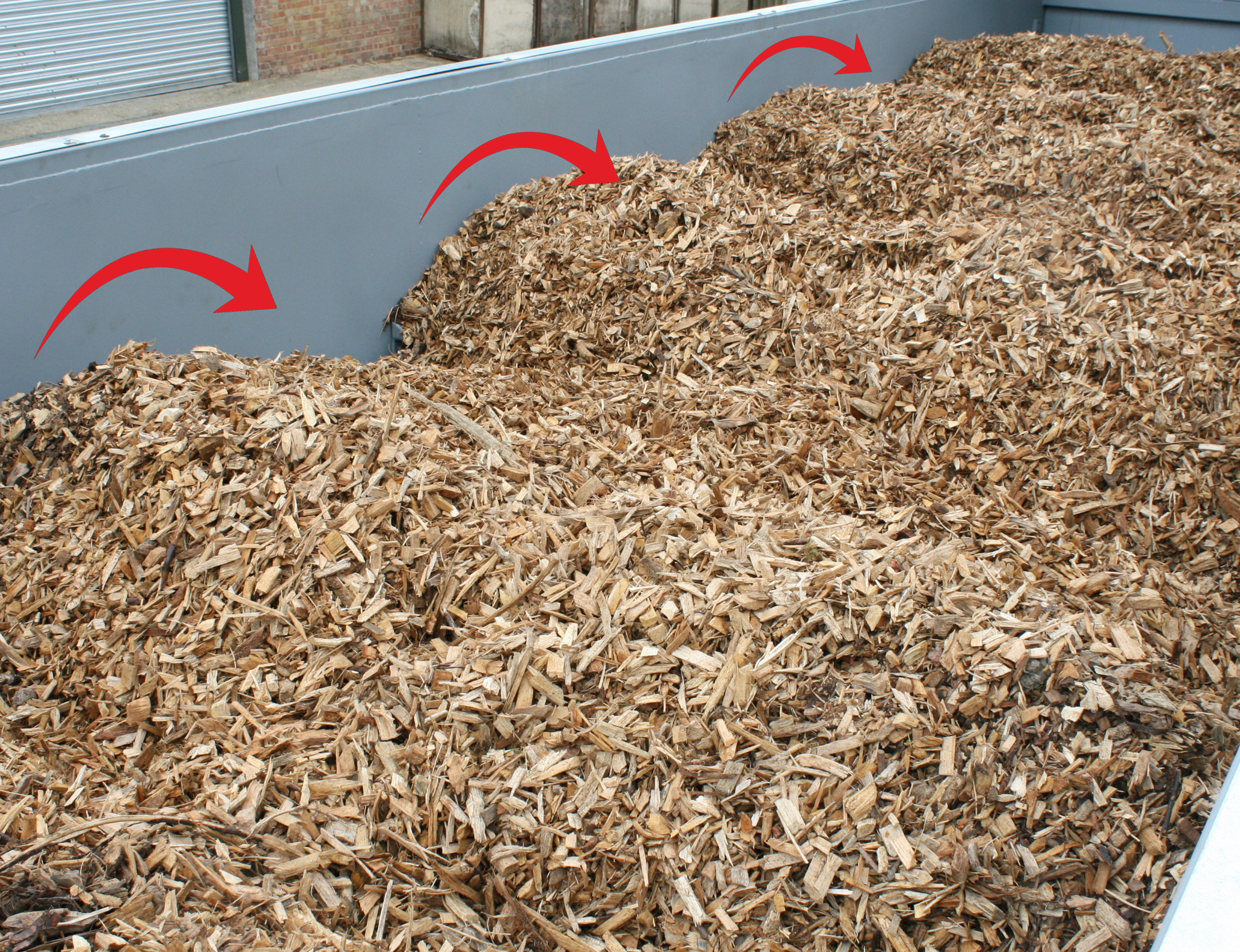
Committed to working with you
Value-driven approach to projects ✔; Individual & communicable ✔; Highly experienced & knowledgeable across a wide range of materials ✔; Attentive to the customer’s best outcomes ✔; Practical, long-life equipment ✔; Simple, reliable, easy-to-use solutions ✔; Environmentally conscientious approach ✔
Stronga have clear product values of building long life machines with excellent reliability while delivering high performance. Our vision is based on long-term values dedicated to adding value for our clients while eliminating waste, improving efficiency, striving for innovation and evolution. Our goal is to be close to the customer, building mutual trust throughout the whole process.
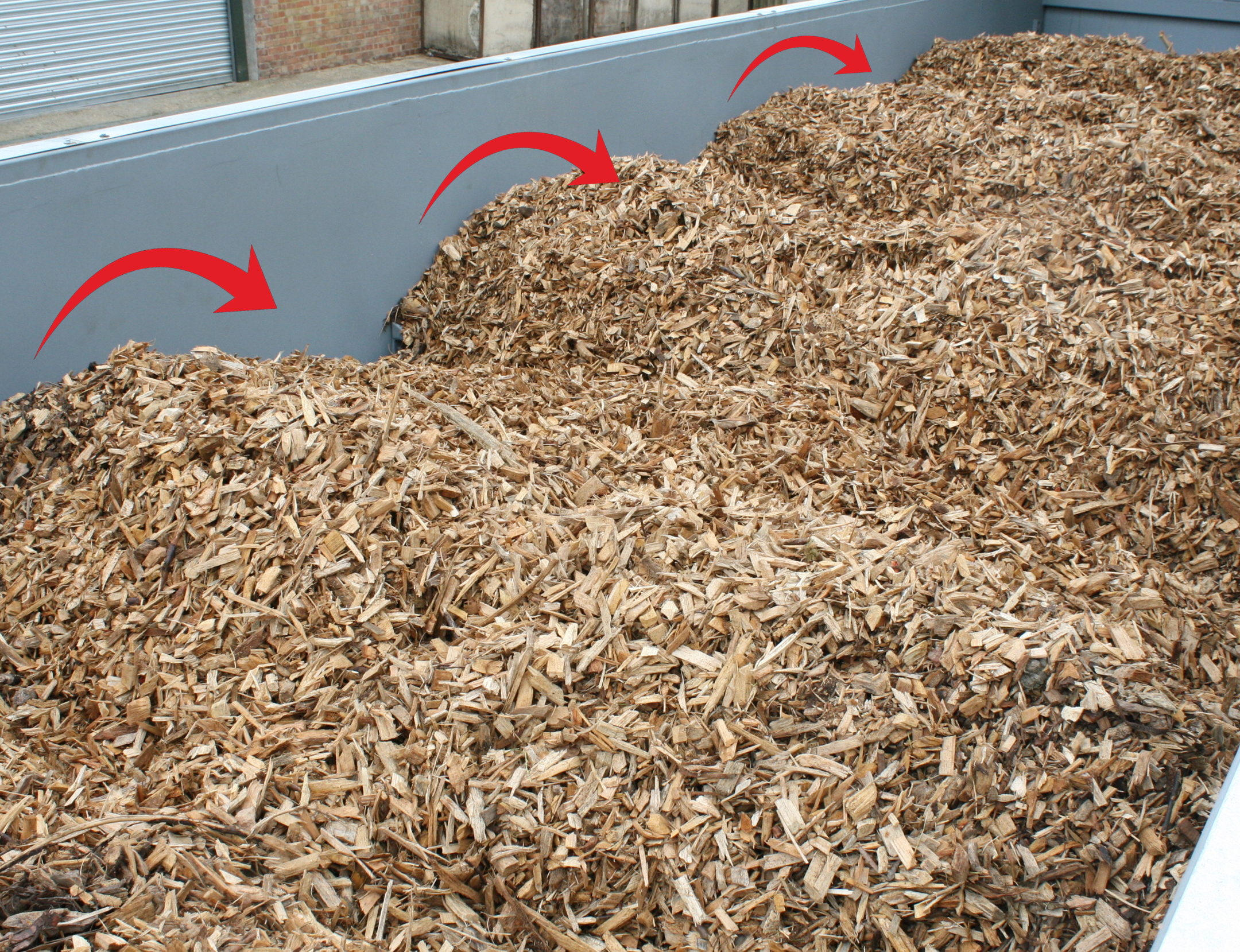
Wir arbeiten mit Ihnen zusammen
Wertorientierter Ansatz für Projekte ✔; Individuell & kommunizierbar ✔; Äußerst erfahren und sachkundig in einem breiten Spektrum von Materialien ✔; Aufmerksam auf die besten Ergebnisse des Kunden ✔; Praktische, langlebige Ausrüstung ✔; Einfache, zuverlässige und benutzerfreundliche Lösungen ✔; Umweltverantwortliches & gewissenhaftes Vorgehen ✔
Stronga hat klare Produktwerte, nämlich langlebige Maschinen mit ausgezeichneter Zuverlässigkeit bei gleichzeitig hoher Leistung zu bauen. Unsere Vision basiert auf langfristigen Werten, die darauf ausgerichtet sind, Mehrwert für unsere Kunden zu schaffen und gleichzeitig Verschwendung zu eliminieren, die Effizienz zu verbessern und nach Innovation und Evolution zu streben. Unser Ziel ist es, nahe mit dem Kunden zusammenzuarbeiten und während des gesamten Prozesses gegenseitiges Vertrauen aufzubauen.
Standard Specifications
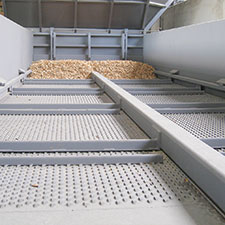
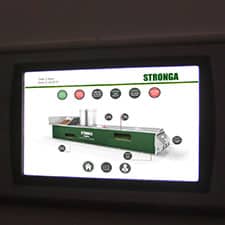
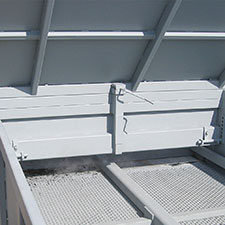
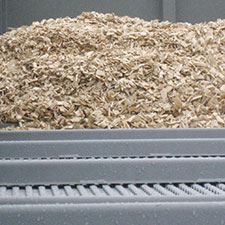
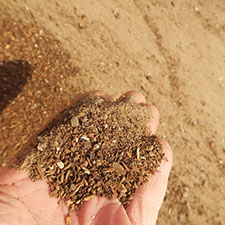
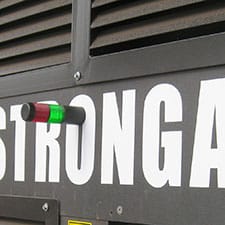
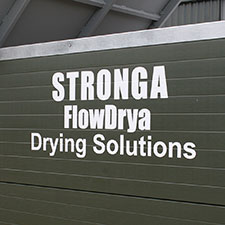
Optional Equipment
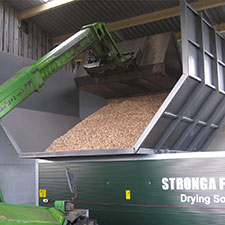
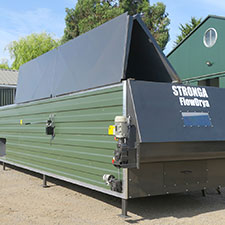
Hydraulic folding roof with hand pump operation and roof-mounted flues.
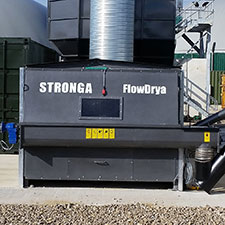
Enclosed cross auger with geared motor and inspection hatch. Integrated with DryStation™. Various sizes available. Watch video >
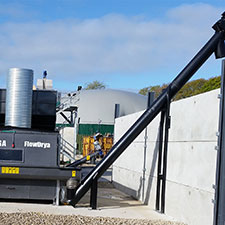
Inclined discharge auger with gear drive and gearbox. Integrated with DryStation™. Lengths and diameters on request.
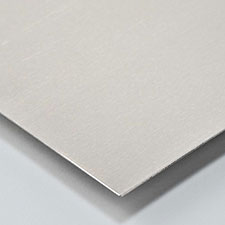
Anti-corrosion stainless steel package, designed for digestate, sewage cake and other corrosive materials.
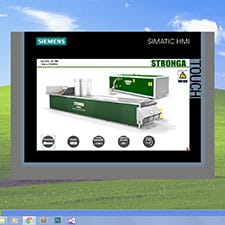
Remote access via Ethernet to desktop or mobile. Various packages available such as viewing access, standalone control or SCADA integration.
FlowDrya is a modular, scalable, individualised continuous drying solution. Please enquire using the form below to discuss a suitably scaled solution for your project.