UK Food Waste AD Plants Under Pressure
From April 2025, the UK government has increased landfill tax rates by a huge 22%, representing a massive increase compared to previous years. The new standard rate for disposal is £126.15 per tonne, up from £103.70 in 2024.
Anaerobic Digestion represents a proactive solution for converting food waste into renewable energy from biogas, however, rising landfill taxes have hit the sector hard, leaving many plants searching for solutions to reduce landfill disposal costs for packaging waste (starch bags, plastic films, flexible plastics and other non-recyclables).
The graph below indicates changes to the UK’s landfill tax from 2008 through to 2025. With a massive 22% increase in 2025, what will the % rate increase be in 2026? Can you afford to stand still? Read on to learn more.
Note – all figures used in this article are based on 2025 UK standard rate landfill tax.
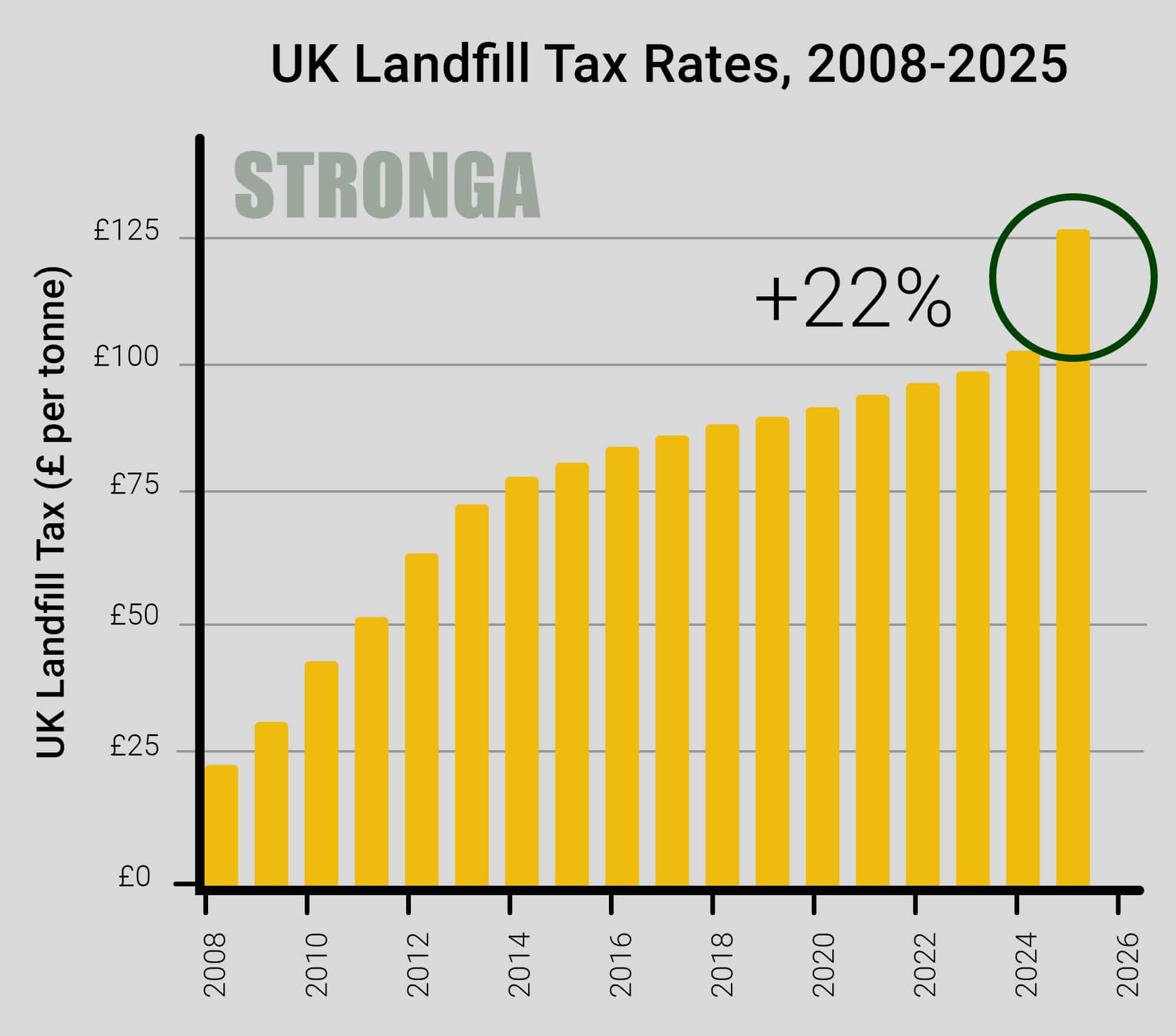
Stronga Collaborate with Food Waste AD Plants
Many food waste AD plants have a stream of plastic packaging and starch bags from the front-end de-packaging process (see photo below). The moisture retention and, resultantly, landfill disposal costs associated with this plastic waste is significant, making it both environmentally and economically burdensome.
Recent landfill tax increases in the UK, have added significant disposal costs for plastic packaging waste which ultimately often ends up in landfill. This rise in taxes has increased the urgency of discussions in relation to drying the material using on-site residual heat from the biogas process.
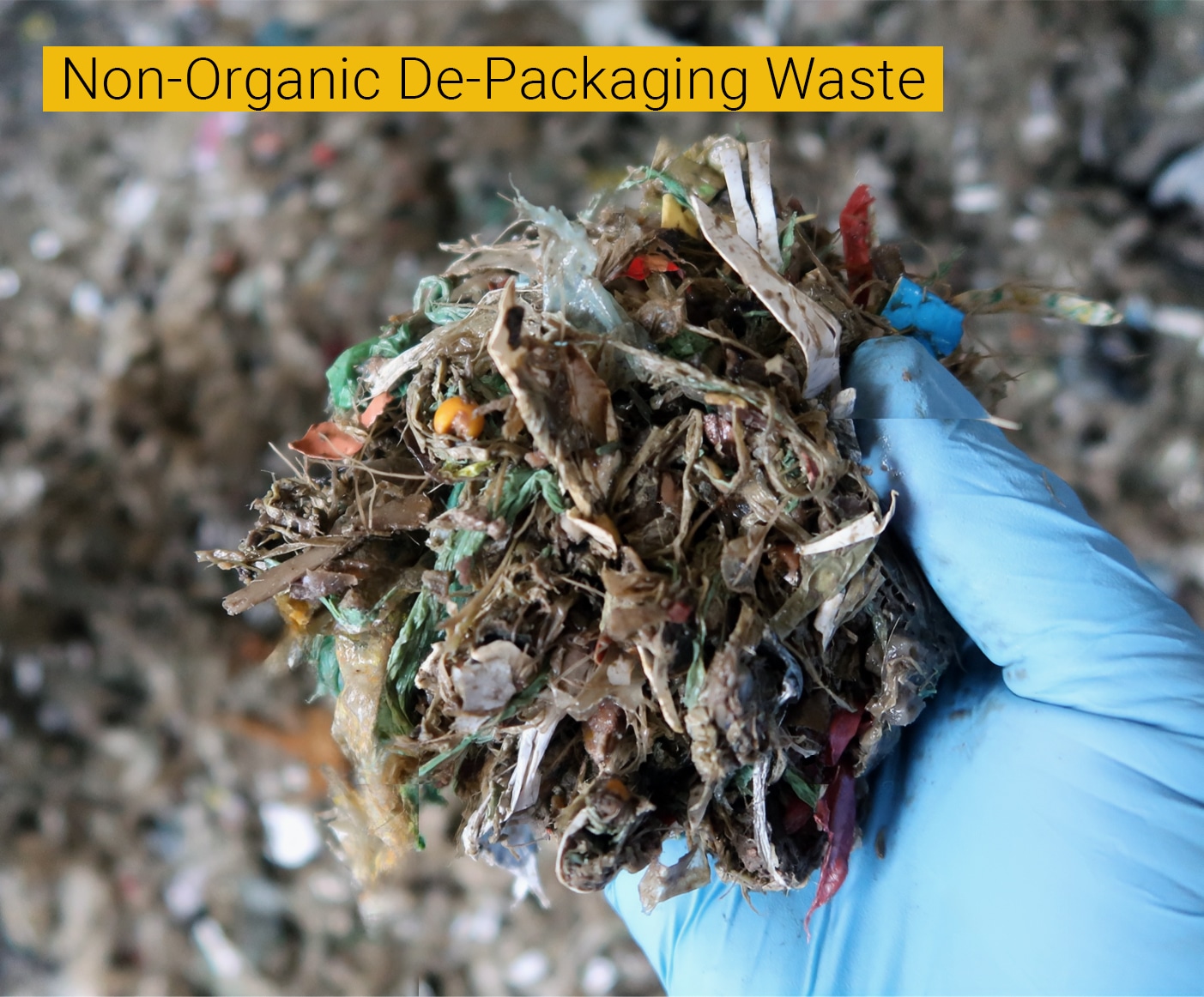
AD Food Waste Process
Step 1. Acquisition of food waste on-site and from supermarkets and retailers, diverting significant levels of food waste from landfill and towards biogas energy production.
Step 2. Separation of the organic fraction material from non-digestible packaging materials (starch bags etc.) using de-packaging equipment, creating a fraction of wet, non-organic packaging that can only be sent to landfill, until now.
Step 3. Organic fraction delivered to AD tanks to produce biogas (CHP etc. used on-site for electric power) and digestate fibre for the production of high-value compost.
Step 4. Drying the wet packaging material using FlowDrya equipment, to not only significantly reduce the weight by 300kg/m₃*, but also reduce the amount of waste remaining. This residual dry plastic waste can then be diverted from landfill and used as a valuable, in-profile alternative fuel. FlowDrya significantly reduces transport, gate fee and landfill tax costs. More on this below.

FlowDrya Eliminates Disposal Costs of “Non-Digestibles”
Investing in FlowDrya equipment enables food waste AD plants to dry their de-packaged mixed starch bags and plastic film, which not only reduces the weight of packaging waste, but offers an economic opportunity, where plants can divert all the remaining plastic waste from landfill and sell the dry waste as alternative fuel. The FlowDrya process not only significantly reduces taxation costs (circa. £500,000), it also creates an added income stream.
The cost savings calculated below are based on 200 tonnes of wet waste disposal a month in the UK. FlowDrya is able to dry the non-organic, de-packaged, starch-bag waste from 400kg/m₃ at 70% moisture content to 100kg/m₃ at 20%. That’s a 75% reduction in bulk density, enabled by the FlowDrya.
Drying the 200 tonnes of packaging waste each month enables the UK plant to divert the waste that would usually go to landfill while the remaining 50 tonnes of residual plastic, that remains after drying, no longer has to be landfilled, creating a valuable income stream from an alternative fuel.
The graphic below uses the 200-tonne metric and the 2025 UK standard rate landfill tax of £126/tonne and shows the huge savings possible with FlowDrya.
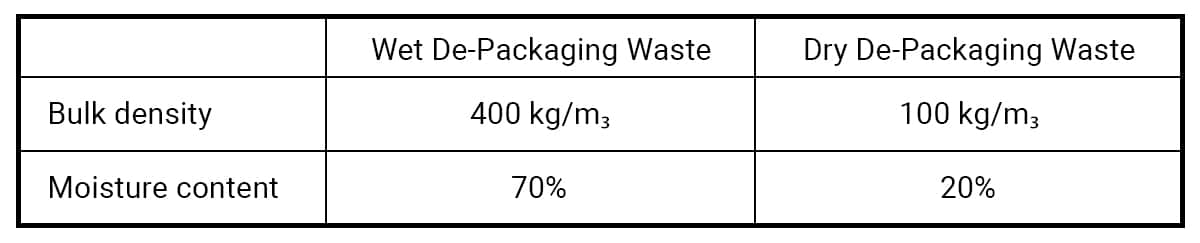
Based on UK rates, taking into account gate fees (£30/tonne), landfill transport costs (£20/tonne) and UK landfill tax savings, FlowDrya is able to divert 200 tonnes from landfill – enabling AD plants to eliminate all landfill disposal costs. Based on the cost of 200 tonnes landfill disposal in the UK, this offers an overall saving of £35,200 every single month – that’s a return on capital of the dryer, delivered within months.
*Figures used are based on a Stronga customer from the UK. We encourage customers to get in touch to obtain figures specific to your project.
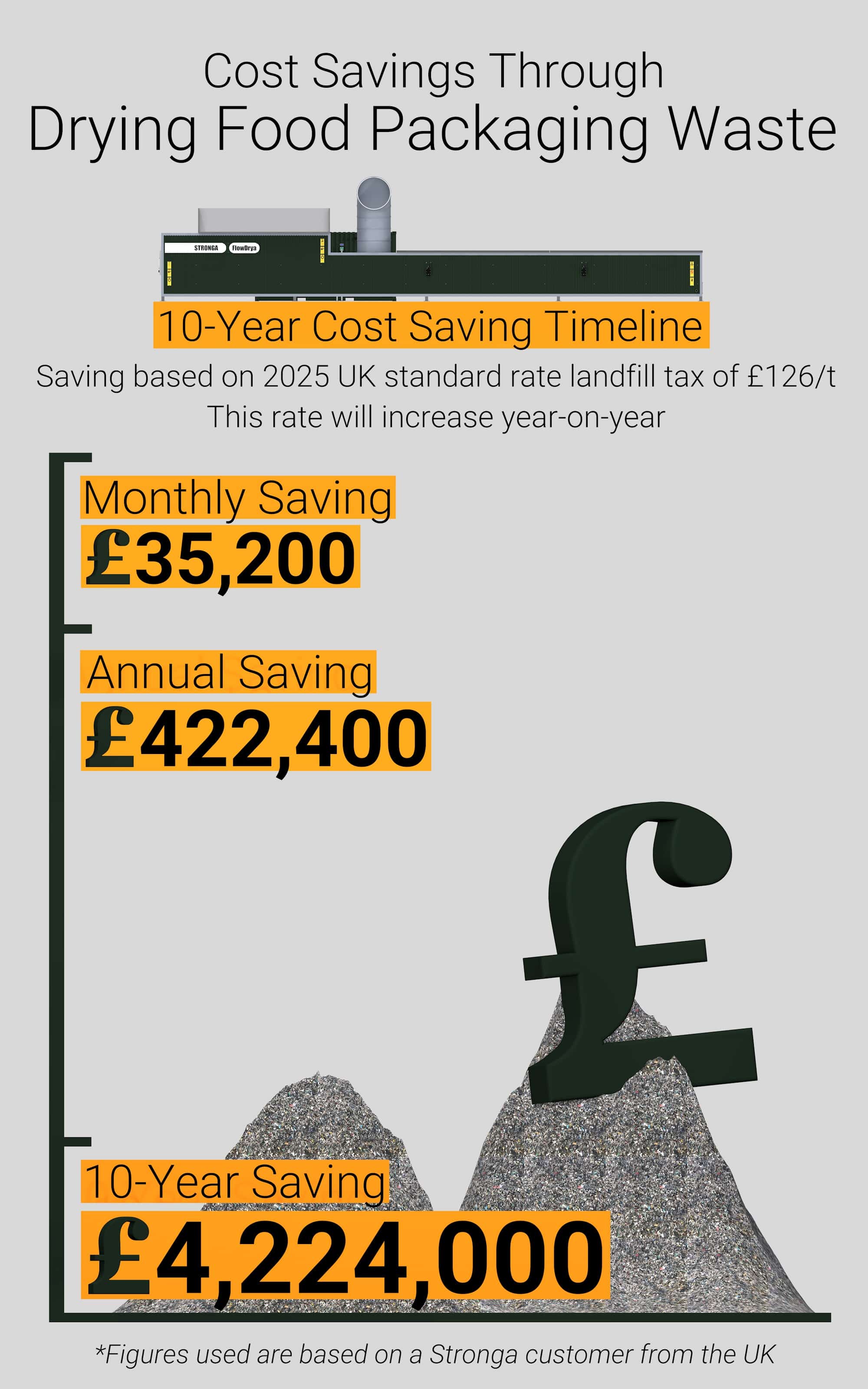
Convert Cost into Income with FlowDrya
Investing in FlowDrya equipment enables food waste AD plants to enjoy huge financial savings while also enhancing the calorific value of the remaining plastic waste residue, because, when moisture is removed, the proportion of combustible material per kg increases. The inherent energy in the plastic waste itself doesn’t change, but through drying, you actively remove the non-energy contributing mass and improve the calorific energy efficiency.
Instead of being landfilled, plastic packaging waste is converted into a dry in-profile fuel that can be sold to cement plants, creating a new revenue stream for food waste AD plants.
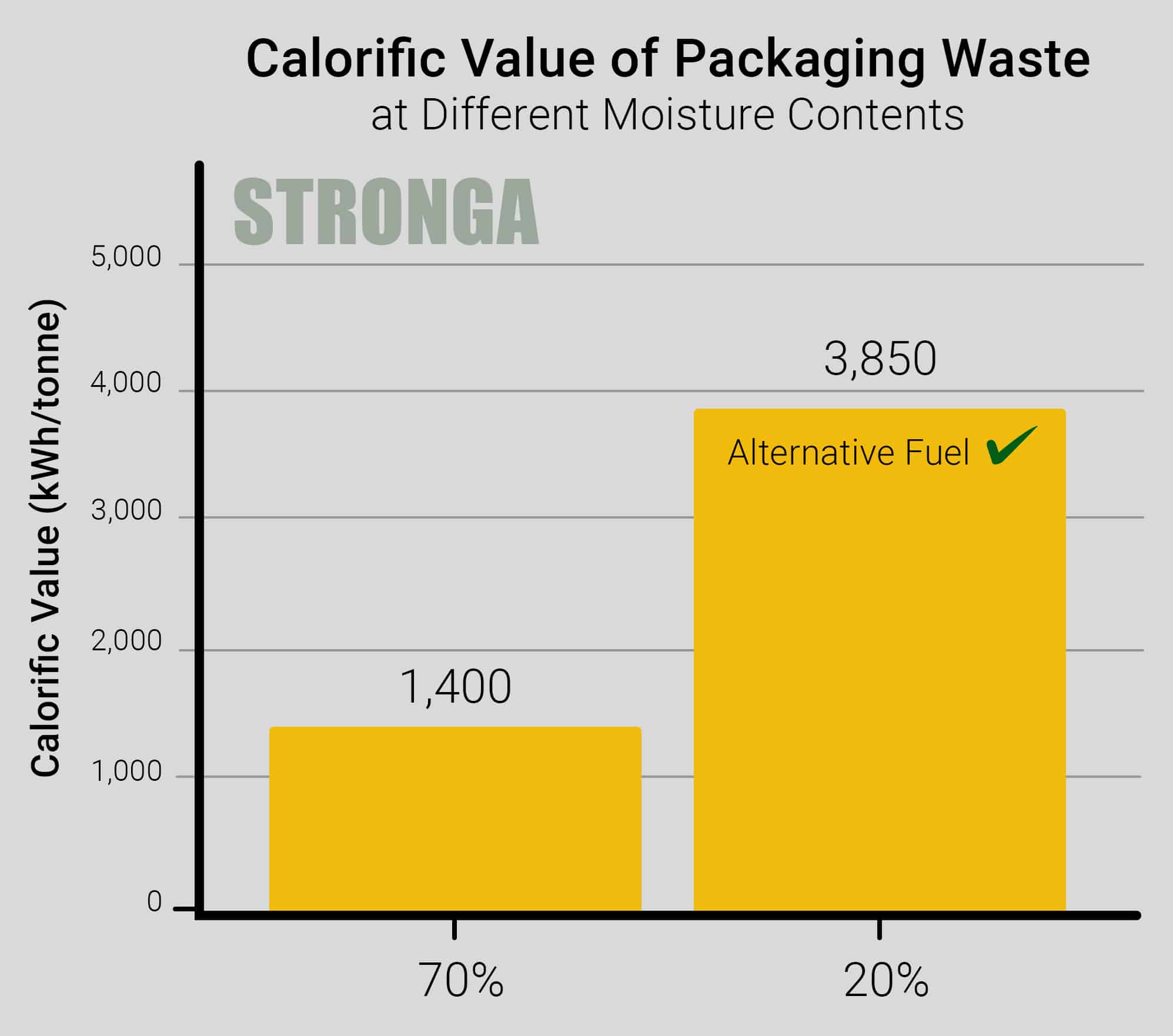
Command Higher Market Prices
Alternative fuel with higher calorific value (delivered by the FlowDrya) is significantly more valuable than fuel with a higher moisture content, commanding higher prices in the market – making the 50-tonne leftover residue more valuable.
If you were to sell the 50 tonnes of plastic waste residue as alternative fuel at £30/tonne – the total combined financial benefits would look like this.
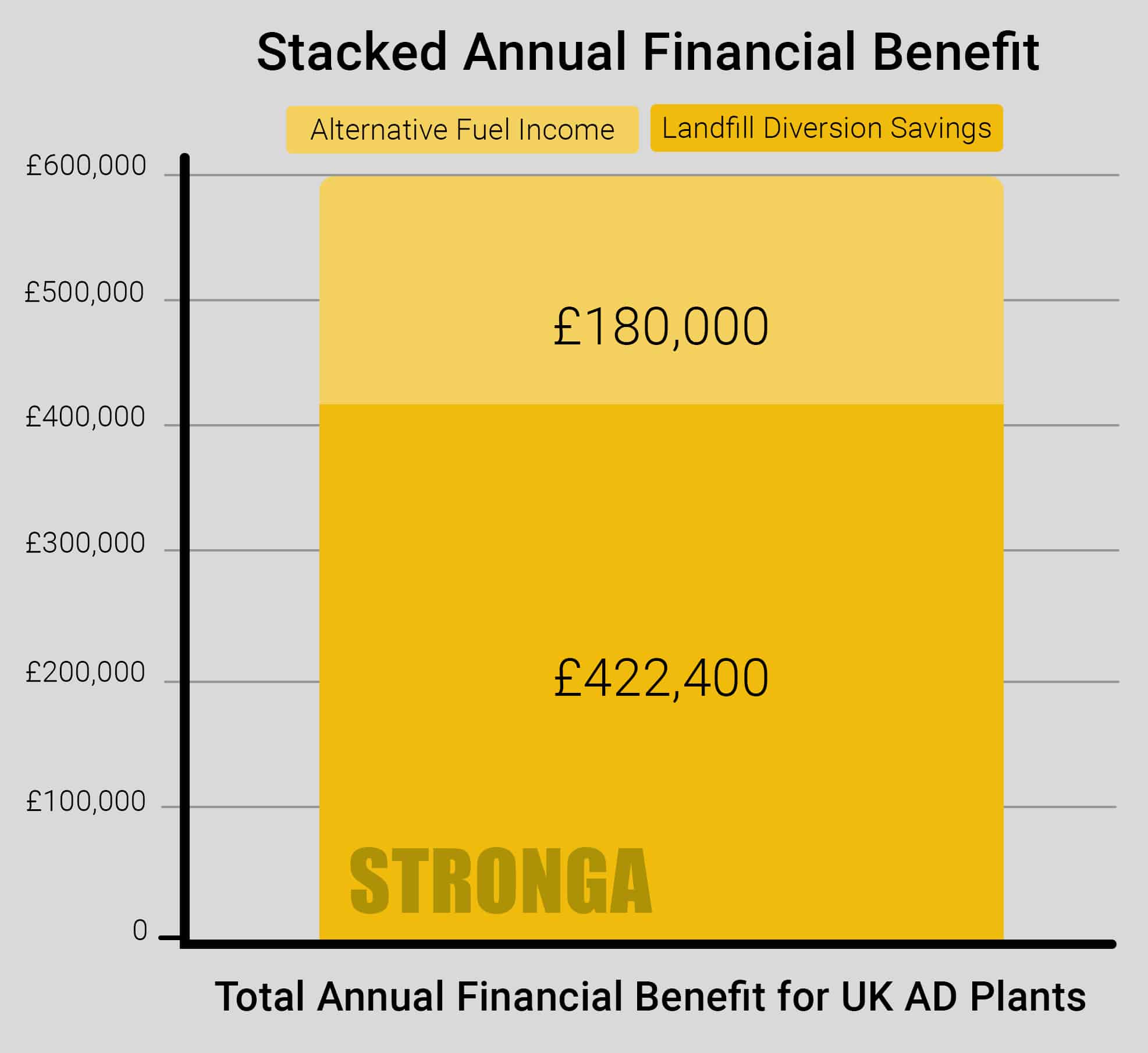
Stronga Packaging Drying Solutions for the AD Sector
Across a wide range of plastic waste fractions, FlowDrya offers the most effective and economic drying solution available in the market. For the non-organic, de-packaging waste fraction (non-digestible packaging) FlowDrya:
• Reduces the volume of waste transported to landfill, thus reducing transport fees.
• Reduces the amount of water sent to landfill, significantly lowering the volume of waste and thus, lowering gate fees and weight-based landfill disposal costs.
• Allows the plastic packaging waste to be more easily further processed for alternative energy fractions, creating income streams and removing landfill reliance.
• Uses on-site residual heat to dry the material. Most food waste AD plants use return water from on-site pasteurisation systems as the heat source for the FlowDrya via Stronga Heatex equipment.
• Returns the capital of purchasing the packaging drying equipment within months, when the cost savings from the landfill tax are calculated.
Watch the plastic packaging waste drying video below. Or click here to learn more about FlowDrya >
Take The Initiative
Working together with Stronga, AD plants across the country have gained a highly-effective resource recovery system, making significant taxation savings which have opened up new and exciting revenue opportunities.
We encourage other food waste AD plants across the globe to speak to our friendly team today to discuss your potential cost savings – enquiries@stronga.com
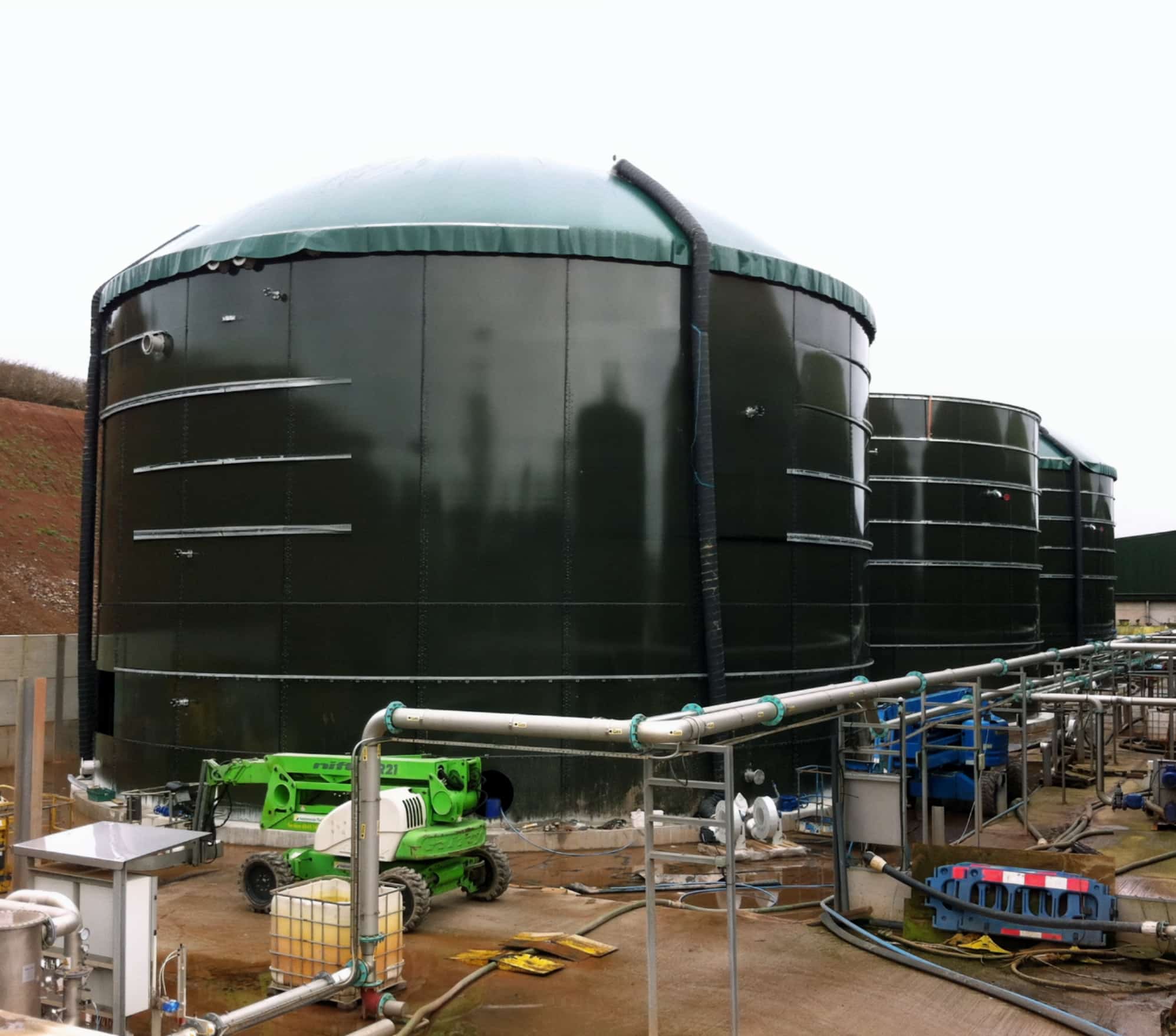
Share this post