What a Load of Waste!
Did you know? Over two billion tonnes of waste is generated globally, every single year. Processing facilities are dedicated to sorting, shredding and processing waste, however, in some cases there are not enough facilities and waste is scattered on land and in the oceans, as per the shocking image below. Stronga aim to be part of a sustainable solution, improving waste management and reducing disposal rates through drying SRF fractions. Stronga’s FlowDrya is capable of conditioning SRF fractions for renewable energy production as a highly effective fossil fuel alternative.
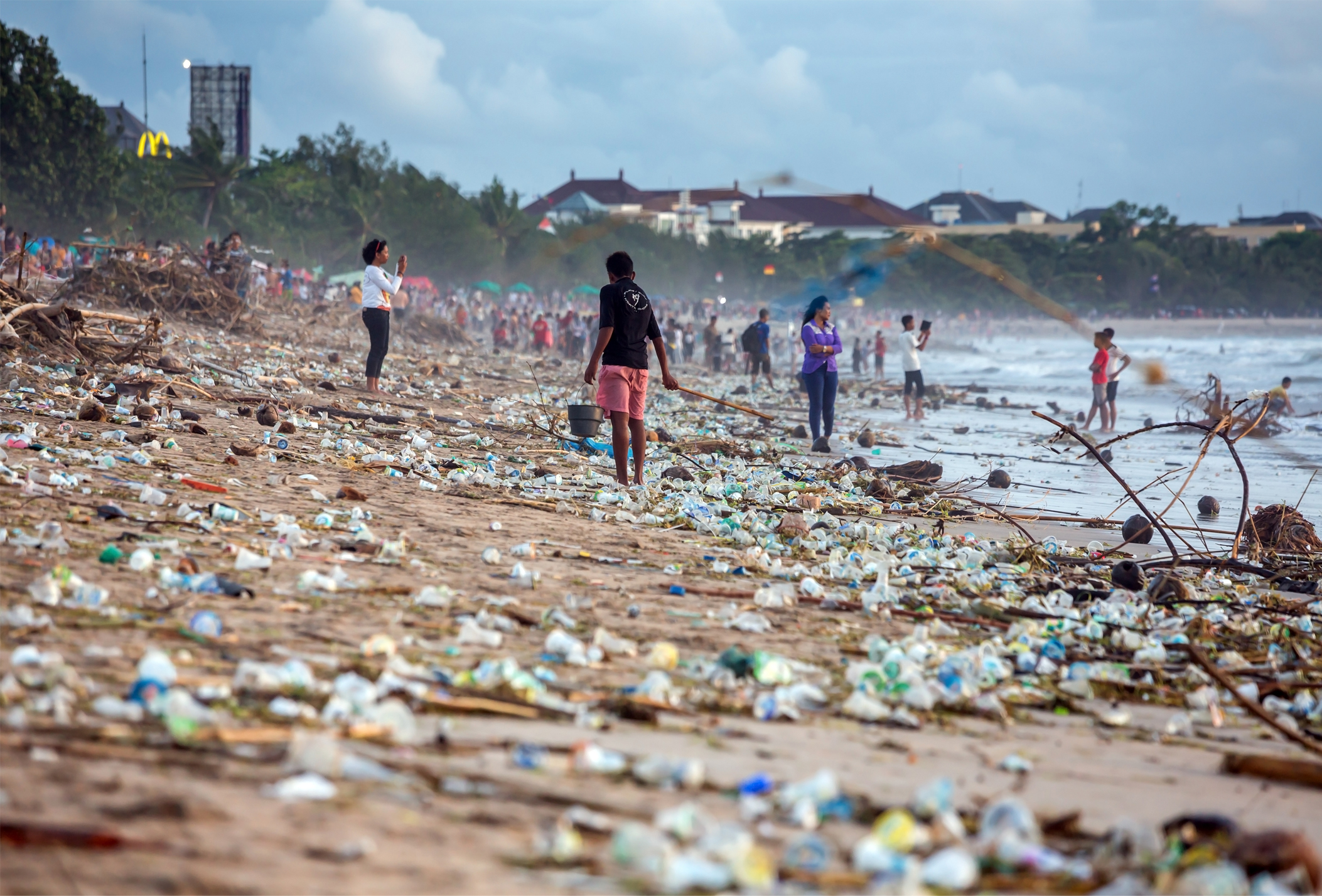
What is SRF?
Solid Recovered Fuel (SRF) is the non-hazardous energy fuel source recovered from waste paper, wood and plastics. It has the potential to have higher calorific values than other fuel from waste (RDF) and produces fewer harmful emissions when used in the right conditions.
Higher production rates of dry SRF at waste to energy plants and cement kilns has the potential to reduce the amount of waste sent to landfill. Using dry SRF as a fuel input for on-site processes reduces the usage of highly taxed, non-renewable fossil fuels whilst also producing ‘cleaner’ renewable energy which can be captured for energy production (CHP).
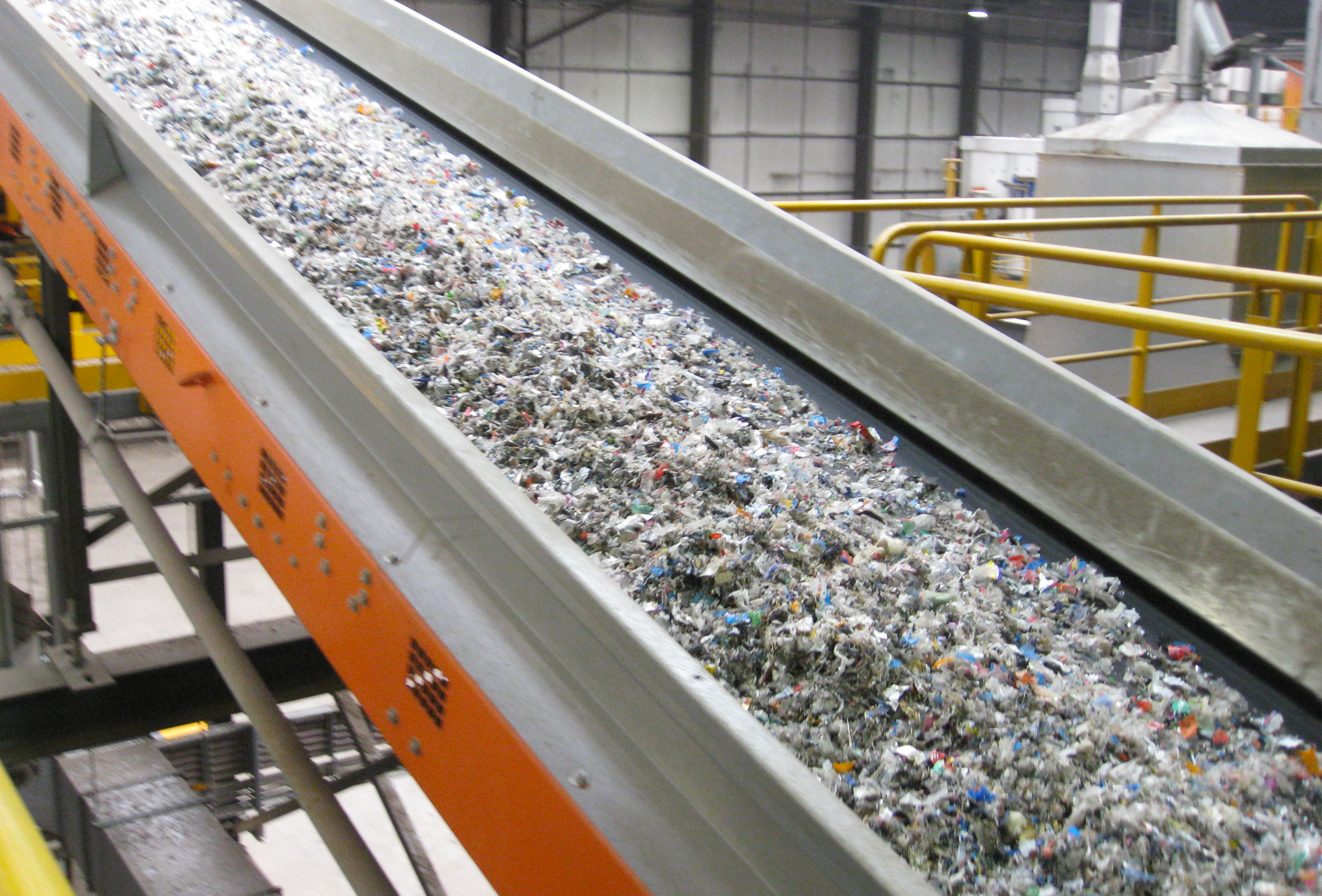
Why Does SRF Need to be Dried?
SRF fractions go through several processing phases to ensure the material meets size and type specifications; processes include mechanical separation, shredding, sorting and screening. Due to rain, imported waste streams can have extremely high moisture content which naturally leads to a wetter SRF fraction with higher bulk density, increasing transport costs whilst leading to mould and decomposition in storage and higher ash and volatile matter content.
Cement works impose penalties on recycling companies for SRF that arrives ‘out of profile’ in regard to moisture content, given the negative affect it has on calorific value. Our team were recently informed by a cement works that using consistently dry SRF feedstock in the cement kiln (shown below) approximately doubled the energy output, highlighting the importance of the SRF dryer in the overall process. Waste to energy and thermal digestion plants also require fuels with consistently low moisture content to produce high calorific energy with less volatile organic compound emissions (VOC).
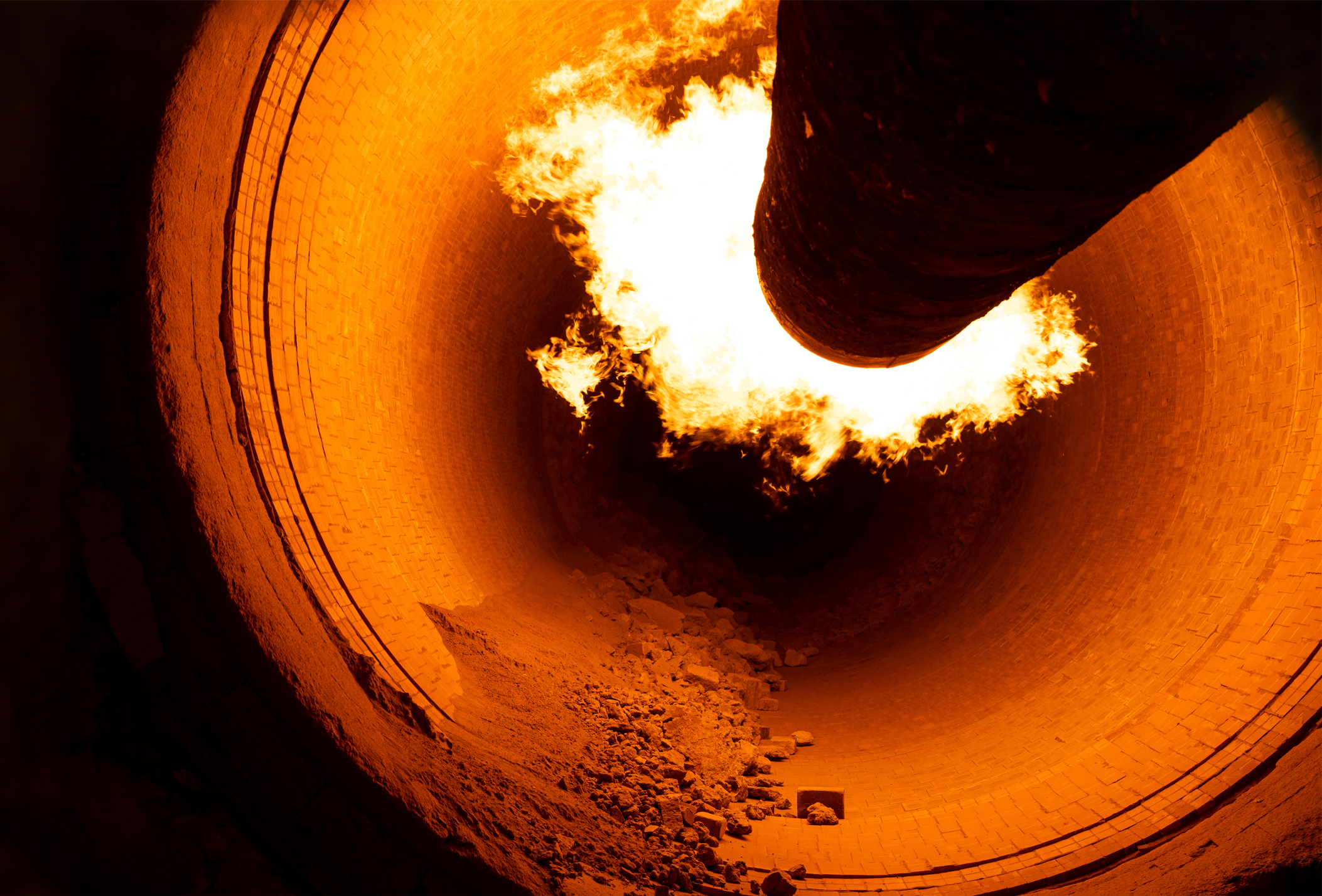
Depending on the client’s process, SRF moisture content should be between 10-20%. If the input fraction hasn’t been adequately dried, the thermal WTE process (pyrolysis, gasification, carbonisation, incineration) will be subject to steam/syngas/energy output inefficiencies, higher maintenance costs and environmentally-damaging emissions.
Waste management businesses that sell SRF not complying with strict moisture content parameters are hit with high penalties, often applied per tonne of material. Waste management facilities should consider that their SRF fraction is tested in accordance with EU standards and produced under a quality assurance scheme, which hold the SRF producer responsible.
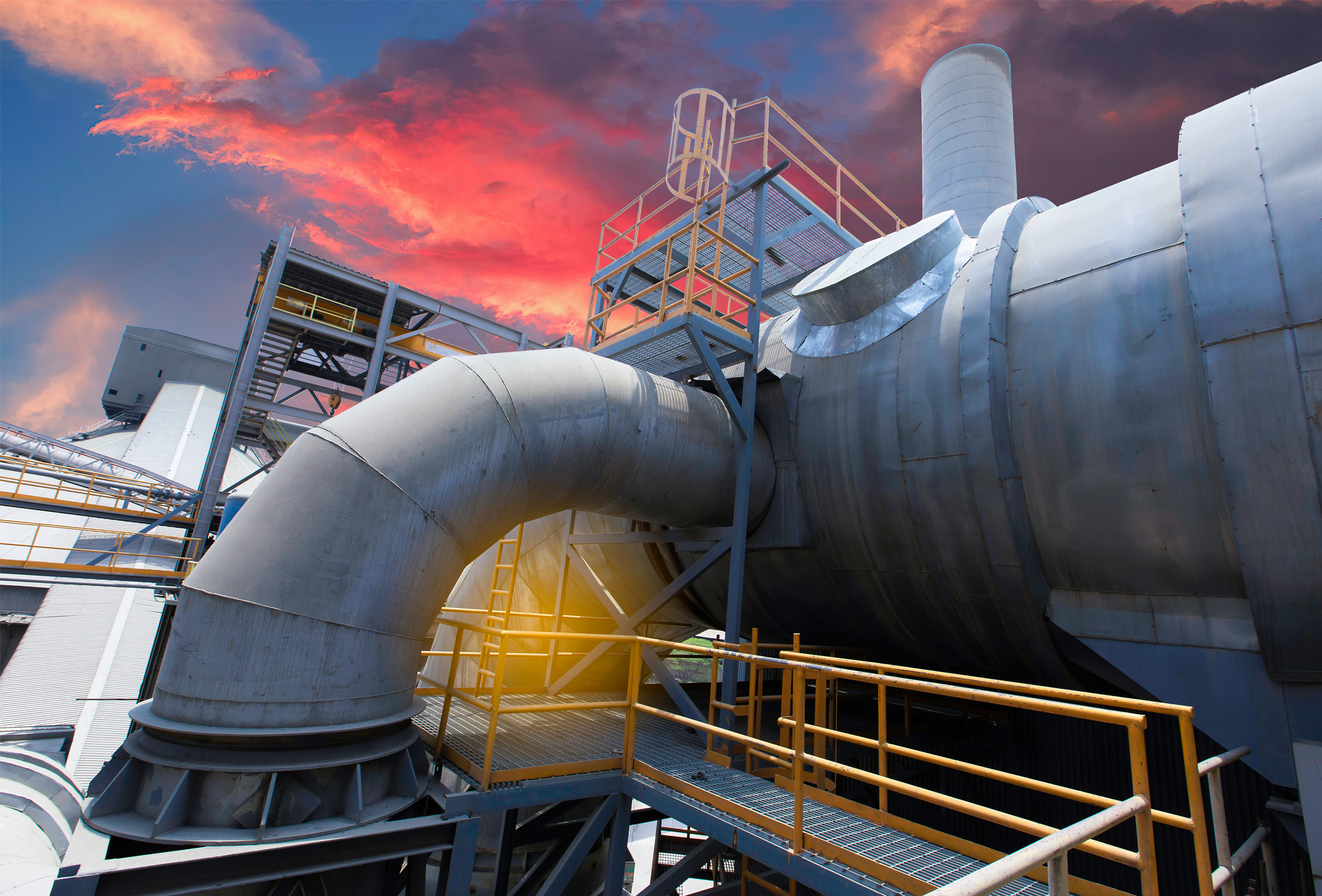
“Will drying increase the electrical and energy consumption costs on my recycling plant?”
Recycling plants rely heavily on diesel generators to power onsite equipment. Even smaller recycling yards have trommels, electrically-powered shredders and sorters, all requiring electrical power which can exceed local grid supply capacity. Historically, businesses have used lower-duty red diesel to combat grid issues and meet on-site power requirements. However, recent changes to laws in the UK mean that red diesel can no longer be used in recycling operations, forcing operators to use derv which is increasing their fuel costs by up to 90%.
Diesel electrical generation produces significant waste heat. On average, over half of diesel energy is wasted, mostly as residual heat outputs from engines, water jacket and exhaust gases. Recent inflation in fuel and grid electricity prices has made operators focus on energy costs - can they continue to waste the heat generated by diesel electrical generation as it becomes ever more costly? Stronga’s FlowDrya and Heatex systems help recycling businesses utilise this wasted thermal heat toward direct added value - drying SRF for valuable outputs whilst avoiding the need for additional on-site energy consumption to run the dryer.
As the animation below demonstrates, making the smart investment in FlowDrya allows waste management operations to stay one step ahead of the competition through drying SRF using already-available residual heat from ‘GenSets’, for example.
“SRF fractions are bulky and light – can FlowDrya handle my specific m₃ volume, continuously and efficiently?”
Stronga have designed a variant of the standard FlowDrya model which has been specially-adapted for productive, efficient and low-cost drying of bulky SRF fractions. Special modifications are made to the design of the moving floor, airflow and infeed hopper in order to suit the unique properties of SRF loads.
FlowDrya has proven to be reliable, robust and simple-to-operate with high-duty operation, often up to 8,000 hours a year. Variable bed depth control, airflow zoning, excellent thermal conduction and the unique ‘PulseWave™’ agitation system, which is visualised in the animation below, all contribute to uniformly dry output SRF. Contact our team to learn more about the features of our SRF drying solutions – info@stronga.co.uk.
“Why should I choose Stronga’s FlowDrya rather than alternative drying solutions”?
One of the features of FlowDrya which our existing SRF drying customers love most is its simple design which has no belt, chains or sprockets, and very few moving parts – making it particularly well suited to the light and bulk nature of SRF fractions. The data logging function on the DryStation™ HMI control panel is also extremely useful, allowing operators to review key parameters and export data to CSV for long-term record-keeping. What’s more, the ‘stop-start’ feature of the hydraulic drying bed means electrical energy used is extremely low because the FlowDrya sleeps in between floor strokes.
All of these key features contribute to overall successful outcomes in SRF drying projects.
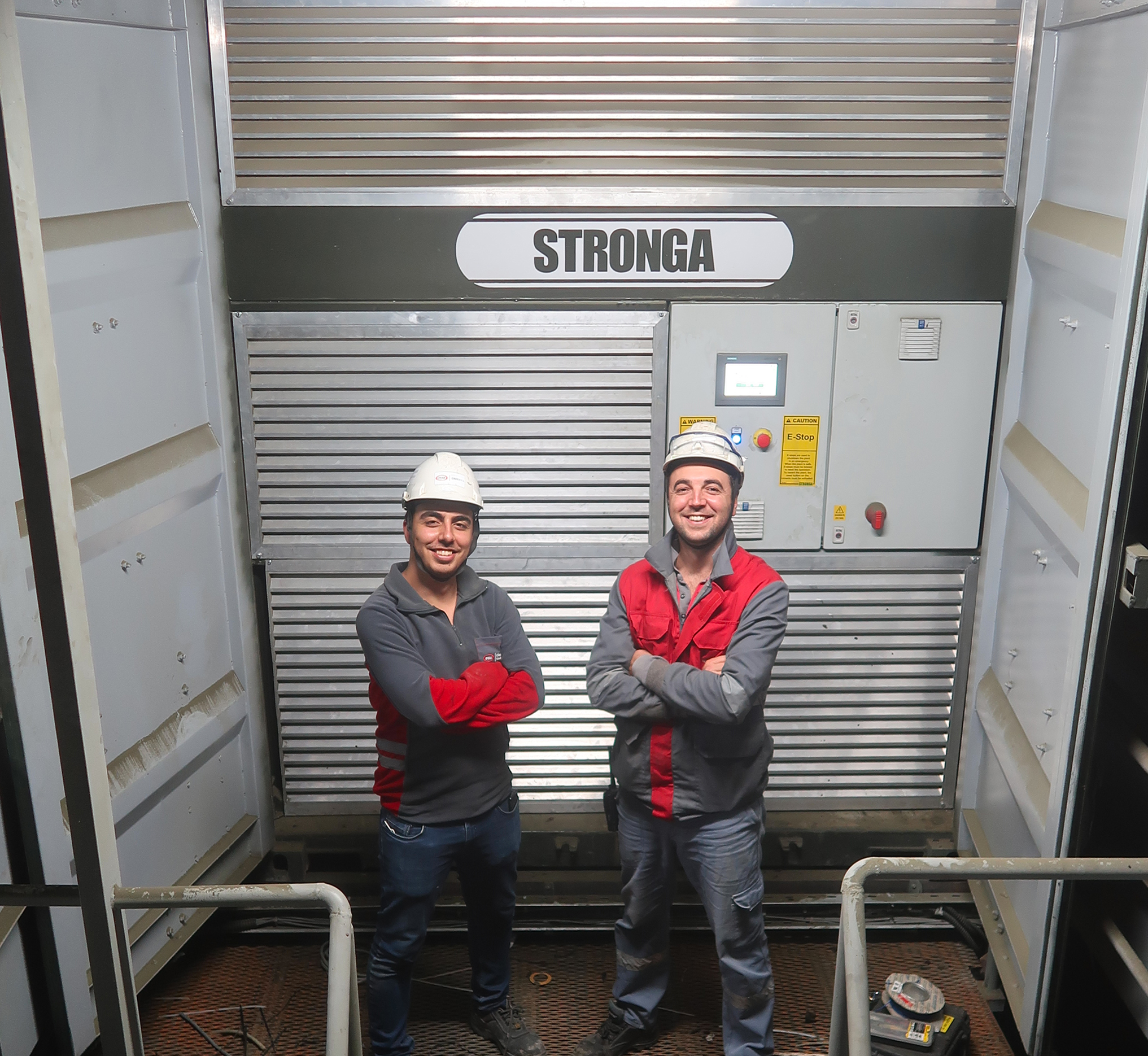
The Key Benefits of Stronga’s SRF Drying Systems, Summarised
FlowDrya is a step-ahead of the other SRF drying solutions available on the market. Discover a summary of the key benefits:
- FlowDrya enables clients to use spare residual thermal heat from cement kiln and energy production operations.
- Stronga specify, scale and design the FlowDrya on a project-by-project basis to perfectly fit your individual requirements.
- FlowDrya has an energy-efficient design with 4x less electrical energy required than other available SRF drying solutions.
- Stronga take the operator(s) through comprehensive training to ensure they are able to control and maintain the dryer for optimum SRF drying outcomes.
- FlowDrya has the lowest maintenance and ownership costs in the SRF drying market thanks to the simple design.
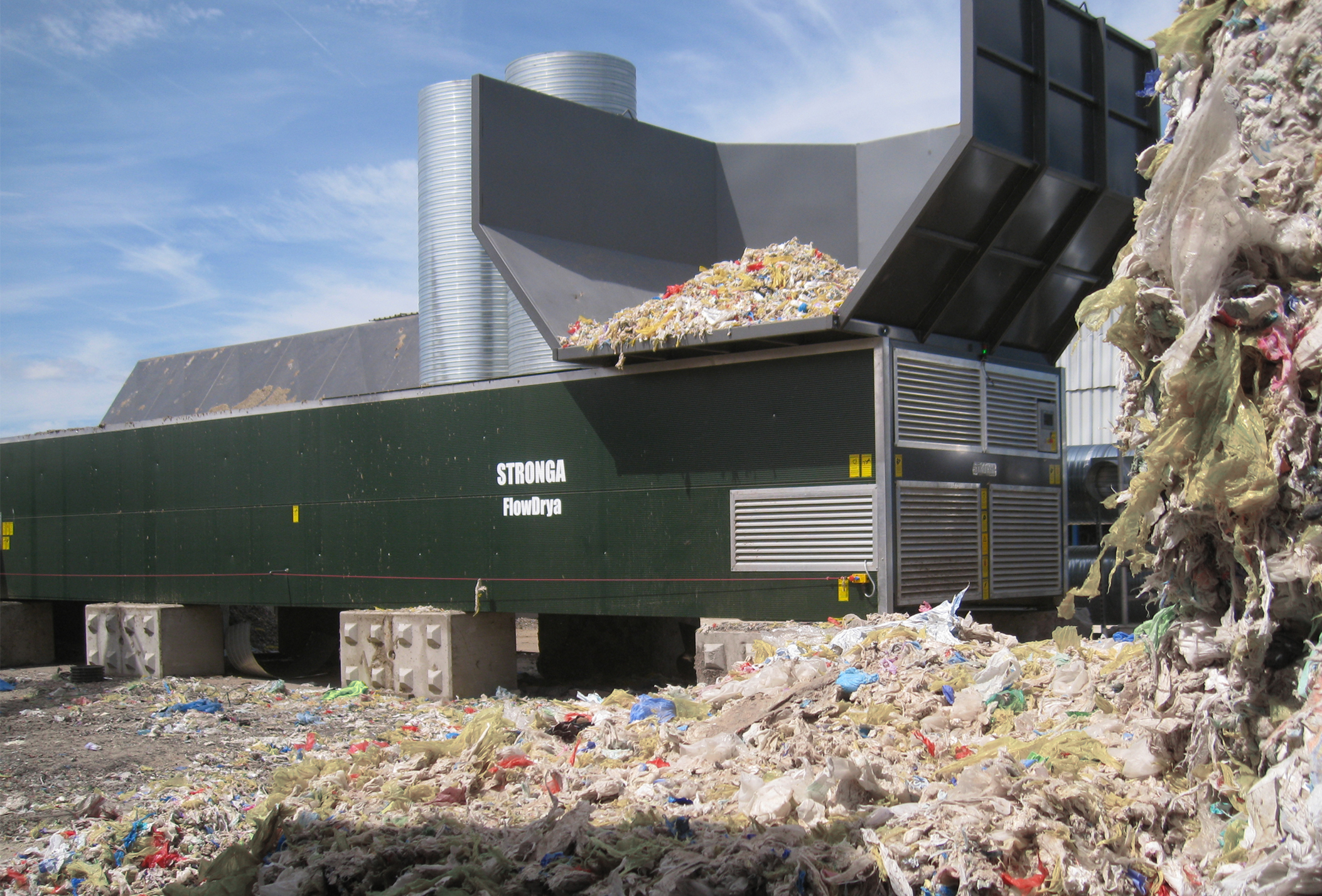
So, Are You Thinking About Selling Dried SRF?
Drying incoming waste steams allows more SRF to be extracted ✓
Drying SRF fraction increases calorific value, enabling higher export sales ✓
Drier fractions are easier to separate and sort, reducing labour costs and machinery operation hours ✓
Drying SRF enables businesses to comply with moisture profiles for WTE reactors and cement kilns ✓
Drying SRF reduces VOCs and harmful smoke emissions emitted when incinerating wet fuel ✓
Overall greater offsetting of expensive fossil fuel consumption ✓
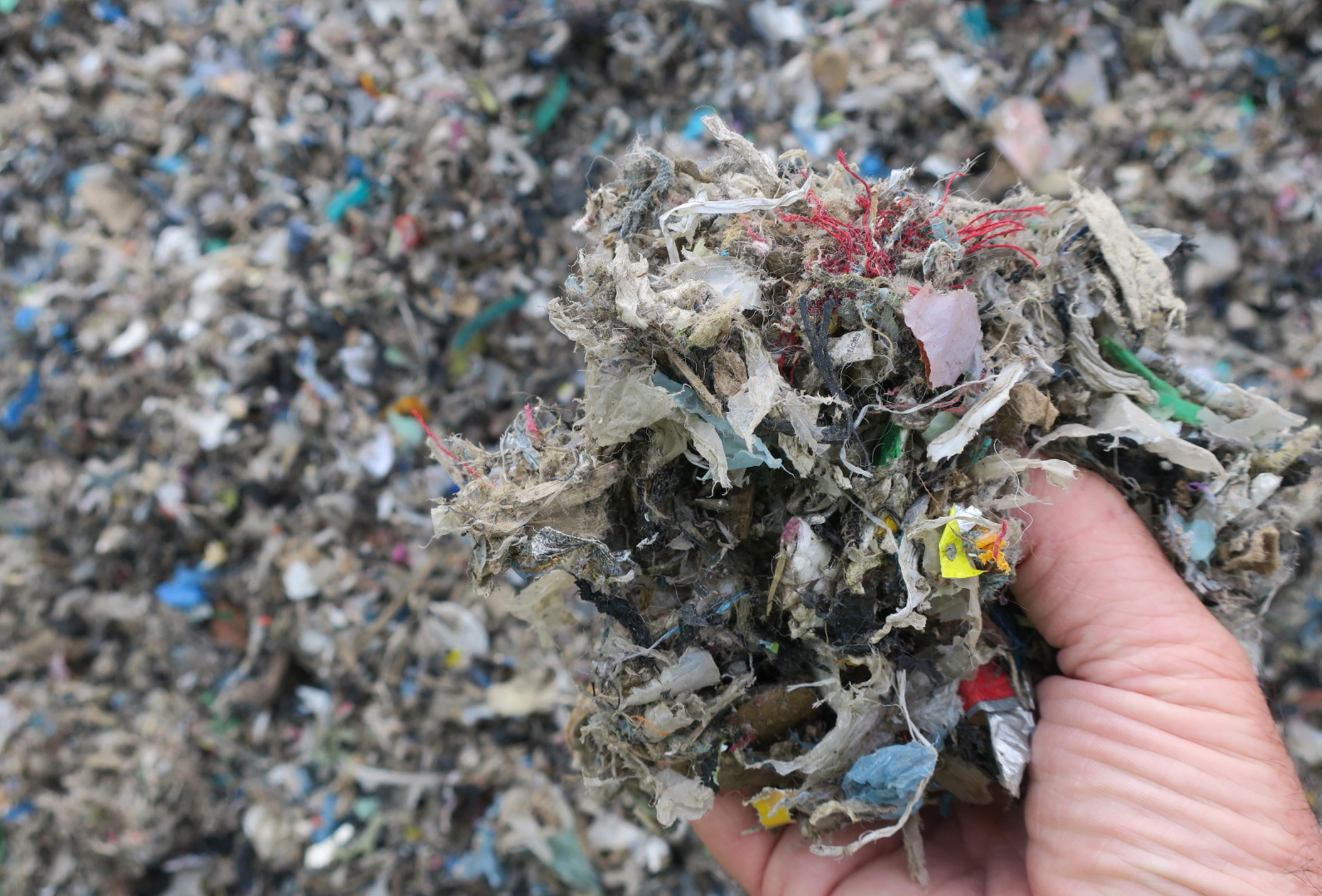
Tell Us Your Requirements
Stronga understands that no two projects are the same; the varying factors involved include the unique properties of the waste material, the client’s location, local climate and more. That’s why we ensure the client’s proposal is viable as we design each FlowDrya to individual requirements. FlowDrya is quickly becoming an industry-favourite drying solution for SRF fractions. We’d love to be a part of your waste to energy journey – email info@stronga.co.uk to take your first step.
Share this post