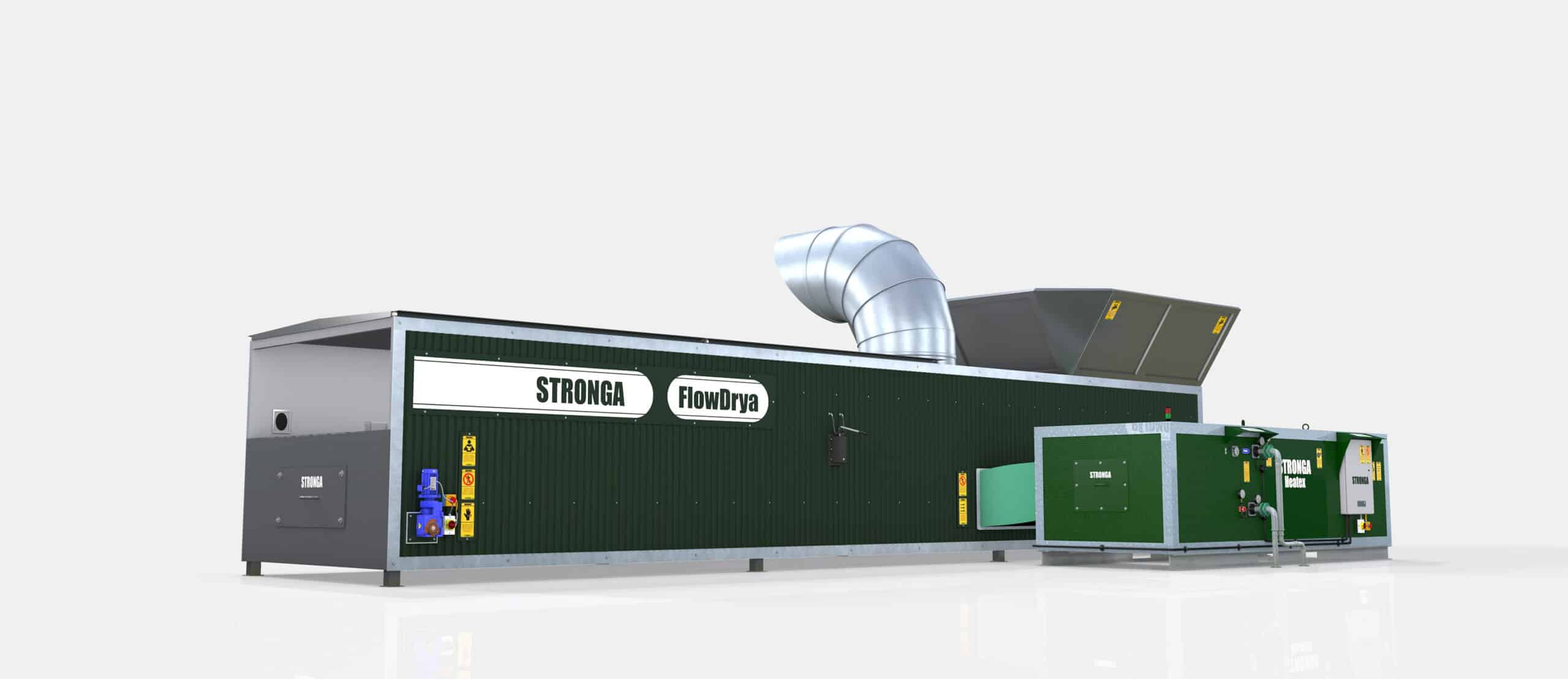
Reliable. Efficient. Well-proven.
FlowDrya continuous drying technology is modern, energy efficient, highly reliable and well-proven in drying a wide range of wet materials. FlowDrya features all the attributes our customers require from a modular, continuous-flow drying system.
Wide range of models offering high capacity output ✔; Excellent thermal & electrical efficiency ✔; Long service life ✔; Stunning reliability ✔; Extremely low service & maintenance costs ✔; Intelligent, easy-to-operate control systems ✔; Uniformly dry output with PulseWave™ mixing motion ✔; High capacity infeed hopper – minimising labour costs ✔; Ability to dry wood chip, forage, paper pulp & more ✔
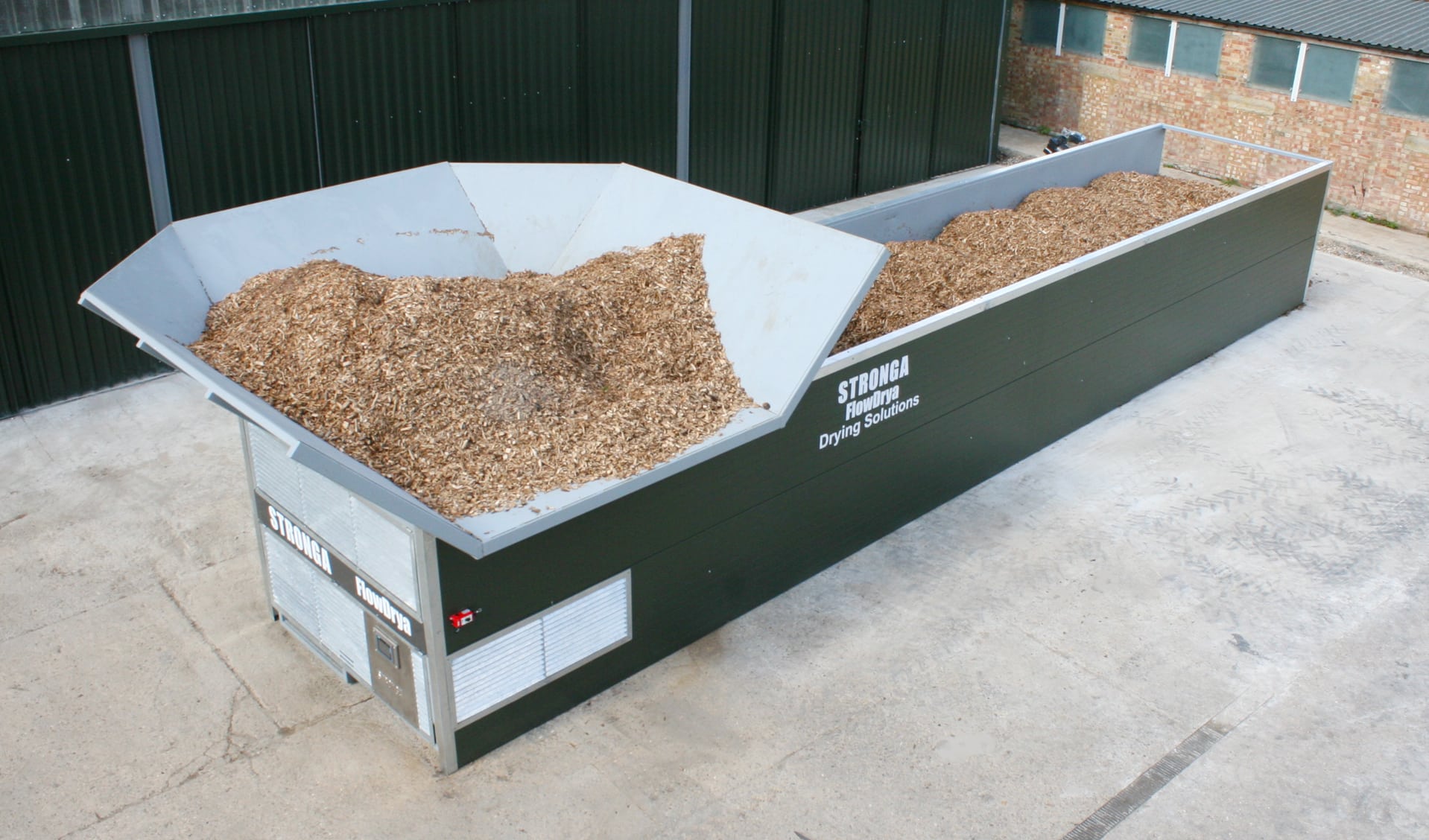
Tailored drying solutions
There are endless lists of wet materials that need to be dried so they can be further processed, stabilised and utilised. Some materials require specific handling during the drying process, others require tight regulation of drying air temperature and the value of others may be increased with minimal cost and by using waste heat only. FlowDrya is the only drying solution available in the market offering the flexibility to cope with the varying properties of different wet materials.

Think flexibility. Think FlowDrya.
With intelligent consideration of your material, location and available heat source, Stronga are able to offer optimised solutions to maximise value from the flow drying process. The flexible FlowDrya system enables unlimited drying potential, leading to long term financial profitability and productivity. Each FlowDrya is tailor-made for the material to be dried, location, climate and so on. Operators should be aware that performance variations may occur if they choose to dry materials other than the one initially specified.
TIMBER INDUSTRY
AGRICULTURE
PAPER & PULP INDUSTRY
WASTE DISPOSAL & RECYCLING
FEED INDUSTRY
FUEL PELLET INDUSTRY
Simplicity is paramount
Every Stronga product is designed to comply with our core principle of building simple, reliable, easy-to-operate machines. The FlowDrya continuous dryer positively moves wet materials from a hopper (end loaded or top deck), along a hydraulic-powered moving floor and over a flow of temperature-controlled drying quality air, fed from a variety of efficient, optimised heat sources. Simplicity is paramount with FlowDrya.
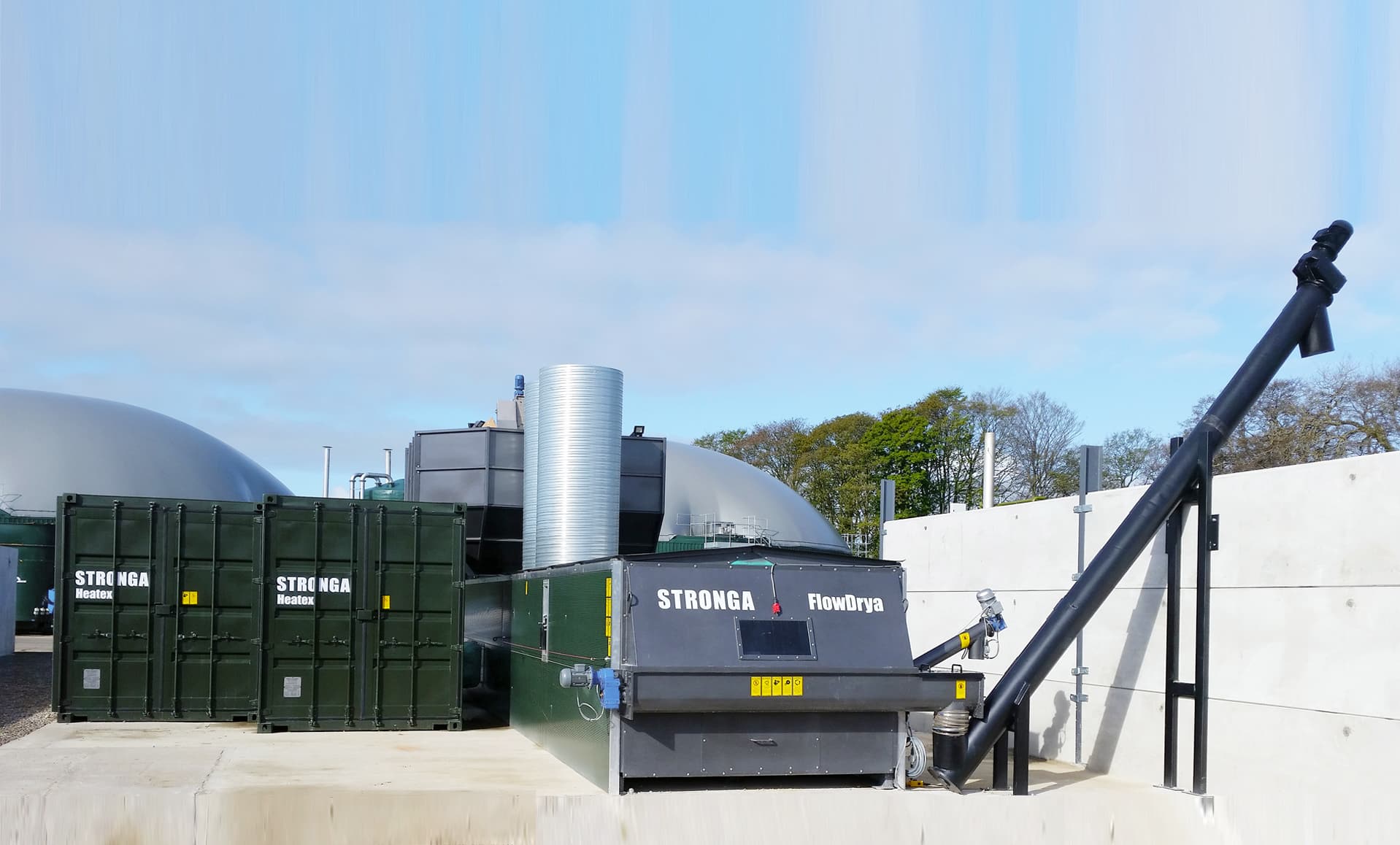
Effortless drying operations
Continuous FlowDrya operations are incredibly simple yet extremely effective in helping you achieve your goals.
Processes can be fully-automated with conveying systems and augers regulating the flow of material into the dryer’s hopper and away from the dry output end. This ensures energy-use efficiency is optimised and production is maximised while closely observing the required final moisture content of the dry output.
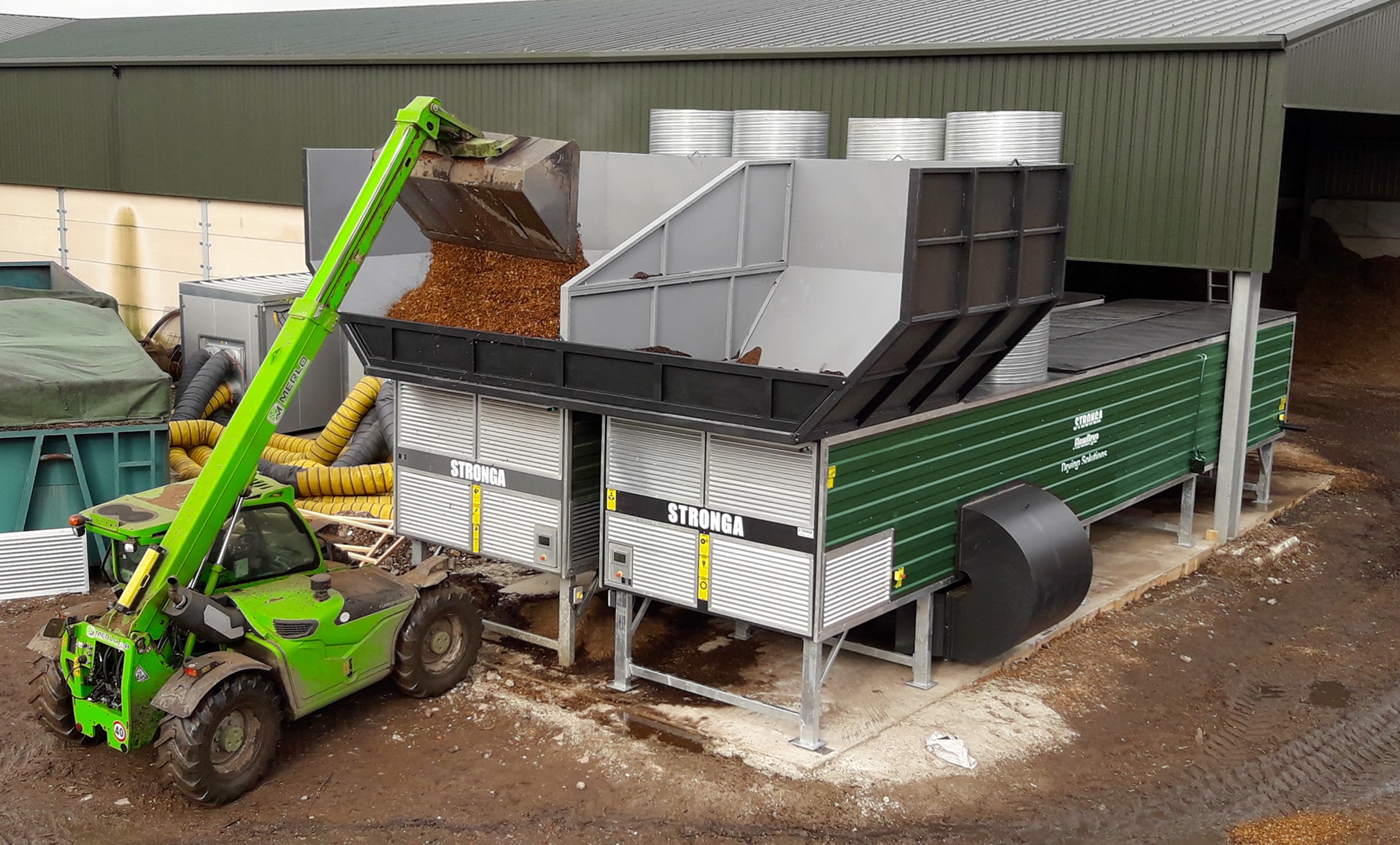
Economic drying solutions
Low Capex – FlowDrya offers excellent value for money at point of purchase. The Stronga technical team consider the whole business case for each project to ensure we offer optimised drying solutions for maximum value.
Low Opex – When compared to other solutions, FlowDrya offers the lowest energy cost per operating hour. What’s more, automatic mode controls (with moisture monitoring), automatic discharge and extended periods between refilling minimise expensive labour hours.
Low Ownership costs – FlowDrya offers extremely low ownership costs from fully considered component quality which ensures maximum uptime, optimum productivity and low service costs. Our reputation for quality-built equipment provides customers with strong residual values and a low cost of ownership.
Cost-effective drying solutions
Cost-effective drying solutions
Drying with warm air
FlowDrya is able to rapidly raise materials to an evaporative temperature because drying occurs in 2 ways; through (1) air drying and; (2) thermal conduction. Injecting drying quality air through wet materials as they roll, tumble and flow along the hydraulic bed optimises the evaporative drying process to reduce moisture content evenly to the client’s requirements. Learn the process.
(1) Drying quality air is delivered by the Heatex unit. Heatex can utilise multiple heat sources, including; low grade residual process heat; CHP engine, water jacket and flue gas heat; biomass boiler thermal output; & more.
(2) Warm airflow heats the insulated steel structure of the FlowDrya sub-floor plenum, conducting thermal energy directly into materials on the drying bed to the supplement air drying process.
(3) Warm air rises through the ventilated floor and through the material. Full length diffusion with intelligent zoning of airflow optimises drying efficiency as the material changes state from wet to dry.
(4) Saturated exhaust air dissipates into the atmosphere via suitably-sized flue ducting, or can be recirculated via modern, well-designed energy-recovery systems.
Drying with thermal conduction
FlowDrya’s unique selling point is PulseWave™ - the automatic agitation of materials as they are continuously tumbled along the moving floor. PulseWave™ ensures that every part of the material receives even thermal conductive contact with the hot drying bed, leading to uniformity of output dryness.
During the forward stroke of the moving floor, materials are tumbled forwards by the pushing blade face, causing a larger driving force low to the bed. The driving force is weaker above the pushing blade, causing materials at the wave’s crest to lag and tumble backwards. In the return stroke, materials are lifted over the tilted axis of the blade to form another wave. As the crest height grows, the wave becomes unstable, causing materials to tumble forwards and backwards, ensuring full agitation on every stroke. Each stroke, materials are displaced from their position which doesn’t occur in belt drying situations; this means that each particle receives equal access to warm airflow and thermal conduction during the process.
DryStation™ control system
Stronga optimise drying outcomes through intelligent and intuitive controls coupled with comprehensive operator training. FlowDrya is designed for continuous operation but drying conditions may change depending on the input material wet basis moisture content, ambient temperature and environment humidity. Some heat loads also fluctuate in the supply of thermal energy due to various factors.
The DryStation™ control system allows operators to configure set points, incorporating automatic modes which adjust operational factors in line with changing conditions. With the remote access option included, the entire control system can be monitored and controlled remotely using an iPad, iPhone, Android or desktop.
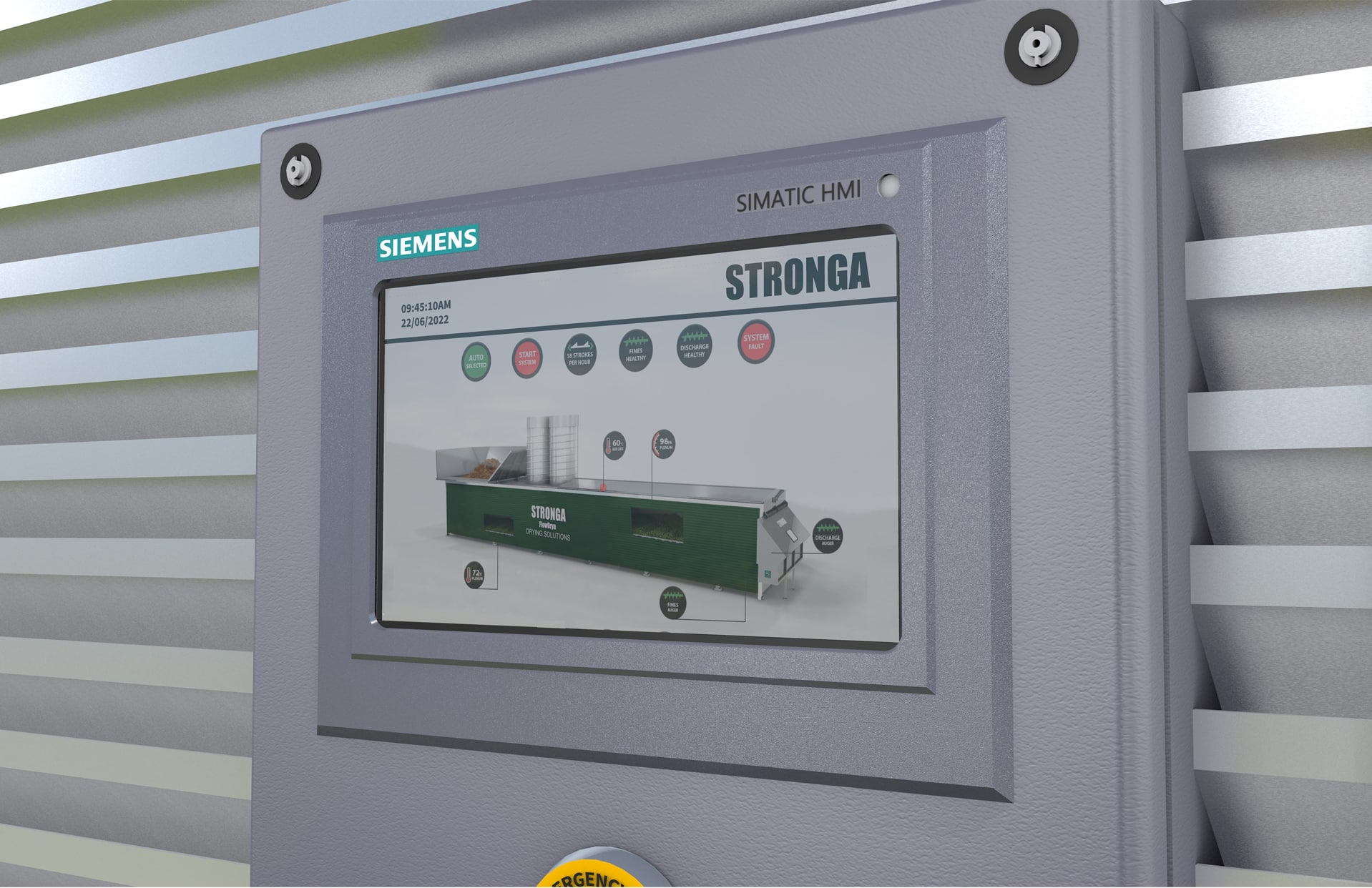
Performance, maintenance & insight
FlowDrya operations are managed by an integrated Programmable Logic Controller which, working in total synergy, maximises efficiency and reliability while reducing time and management costs. Low maintenance, robust PLC systems integrated and sealed within the dryer have durable infrastructures designed to withstand local operating temperature variations. Next-gen FlowDrya controls optimise drying processes to give you peace of mind while improving drying efficiency and outcomes. FlowDrya’s automation control systems offer safe and secure data logging, enabling operators to analyse key factors and optimise drying operations.
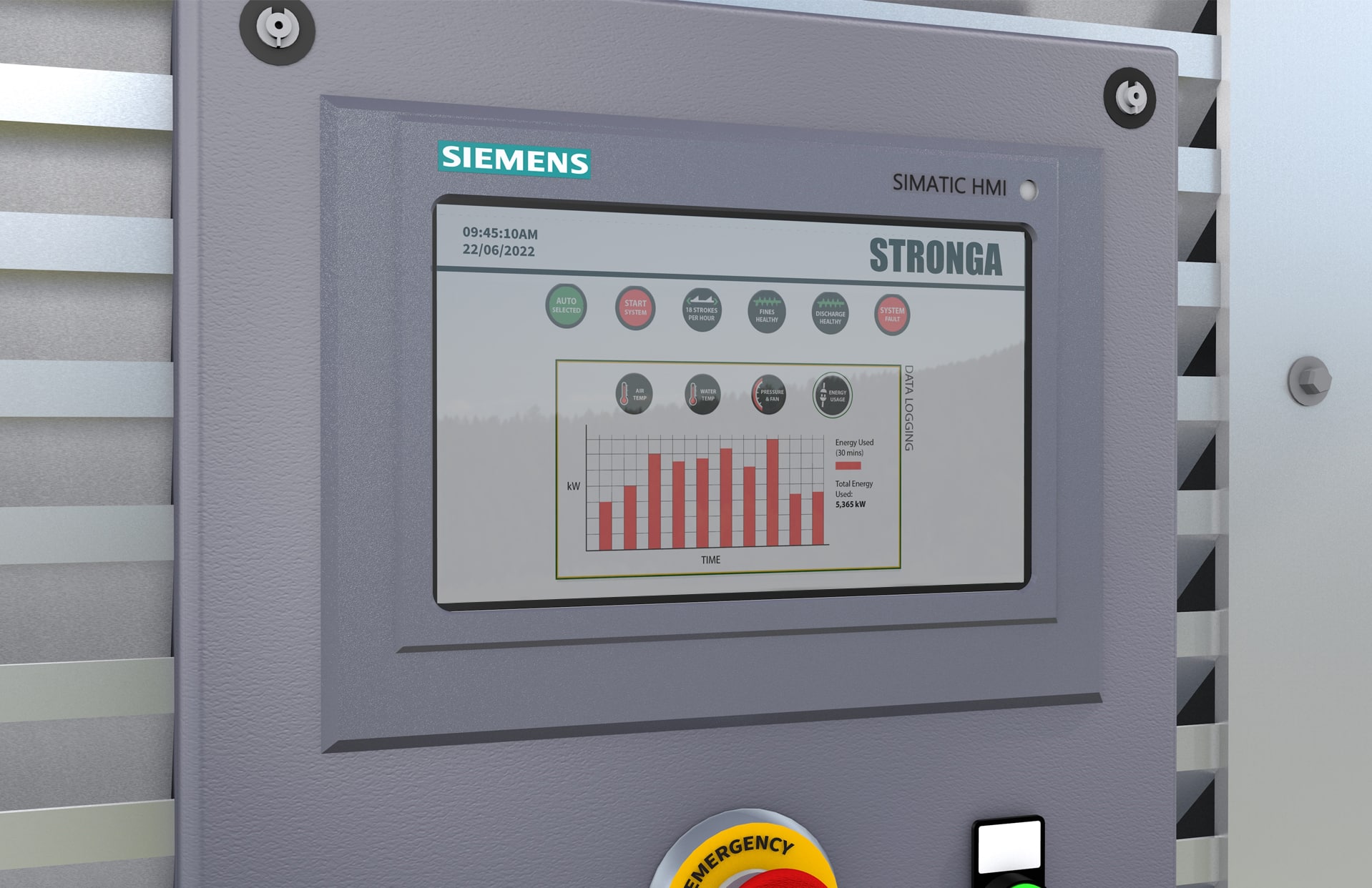
HMI touchscreen interface
The illuminated DryStation™ HMI touchscreen is the user’s graphical interface between the PLC system and the dryer. The DryStation™ console enables instant visual access to the controls, operating and safety parameters. FlowDrya’s control system incorporates the following equipment:
High resolution wide-screen colour display ✔; Innovative graphical user interface ✔; Easy-to-operate usability ✔; 3D imaging of your dryer with key parameter icons ✔; Energy usage monitoring ✔; Remote access potential (stand-alone control or SCADA integration) ✔; Modern soft-start technology ✔; Intelligent and explanative fault-finding notifications built-in, on-screen ✔; Time stamped data recording for operational analysis & comparison; enabling constant user learning ✔
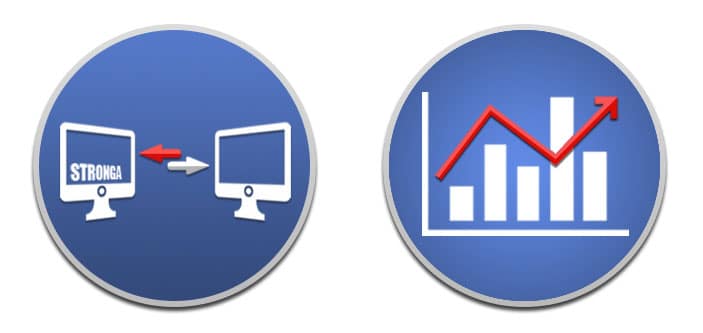
Comprehensive operator training
During the commissioning phase, Stronga work together with the designated operator(s) to ensure they are fully trained with the flow dryer controls, safety, service and maintenance. The comprehensive training procedure is led by an experienced Stronga engineer, ensuring the operating team feel fully confident to take charge of the continuous flow drying process. What's more, our technical team remain on-hand to provide expert remote support, if required.
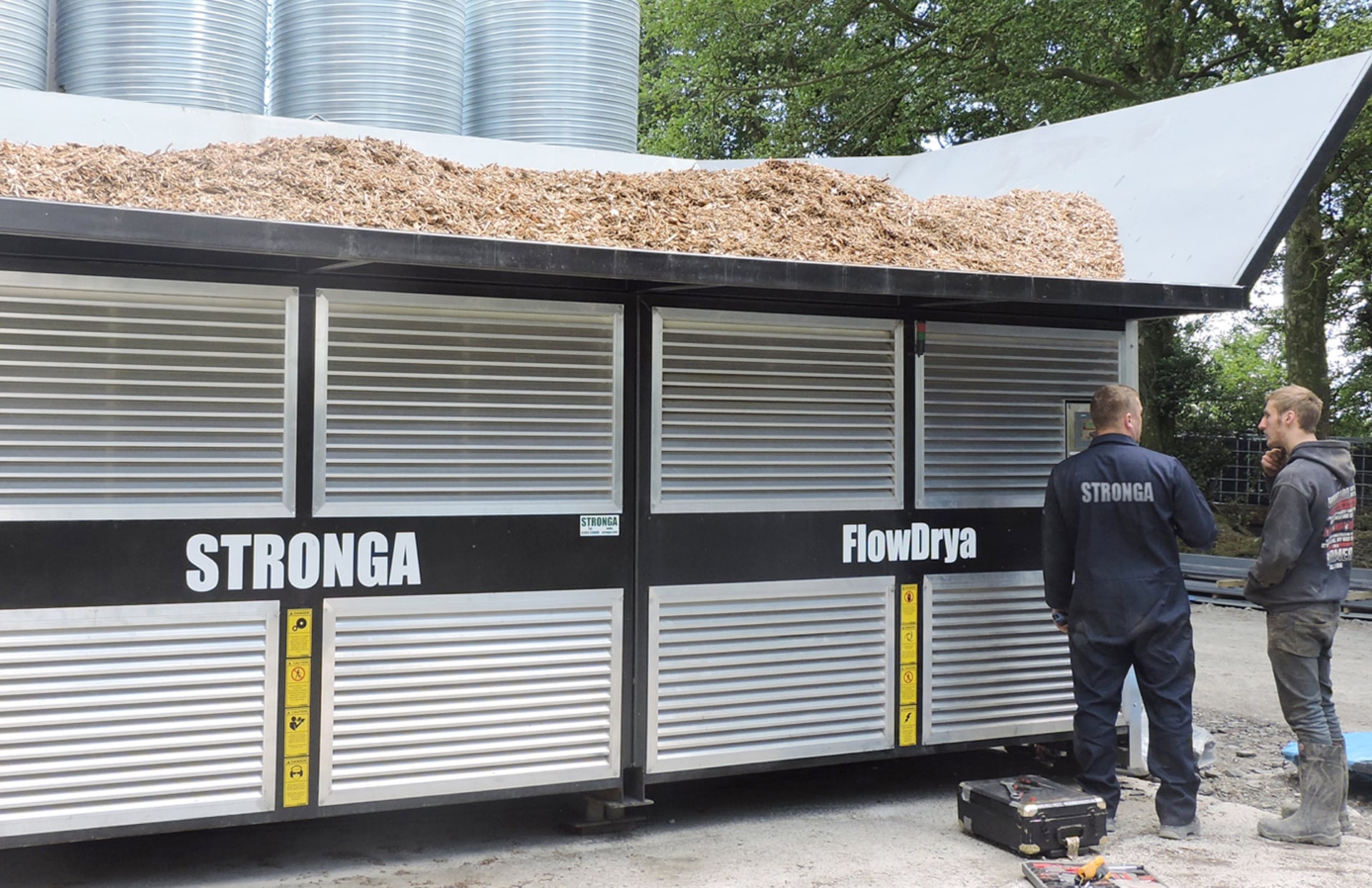
Harnessing thermal process energy
Our experience has taught us that there are many wasted heat sources from flue gases to process heat and CHP cooling. We believe that wasted heat should be fully utilised for both financial and environmental benefit. To make the most of your spare heat, you need a dryer that leads the way in versatility, durability and ease of operation. The following wasted residual heat sources can be harnessed by diverting spare heat via heat exchange into FlowDrya, adding value by drying available wet material:
• Gas engine thermal output from landfill sites and AD plants
• Industrial process heat from cement production & more
• Residual heat from Organic Rankine Cycle (ORC) units
• Residual heat load from steam turbines & more
• Other hot exit air and flue gas sources
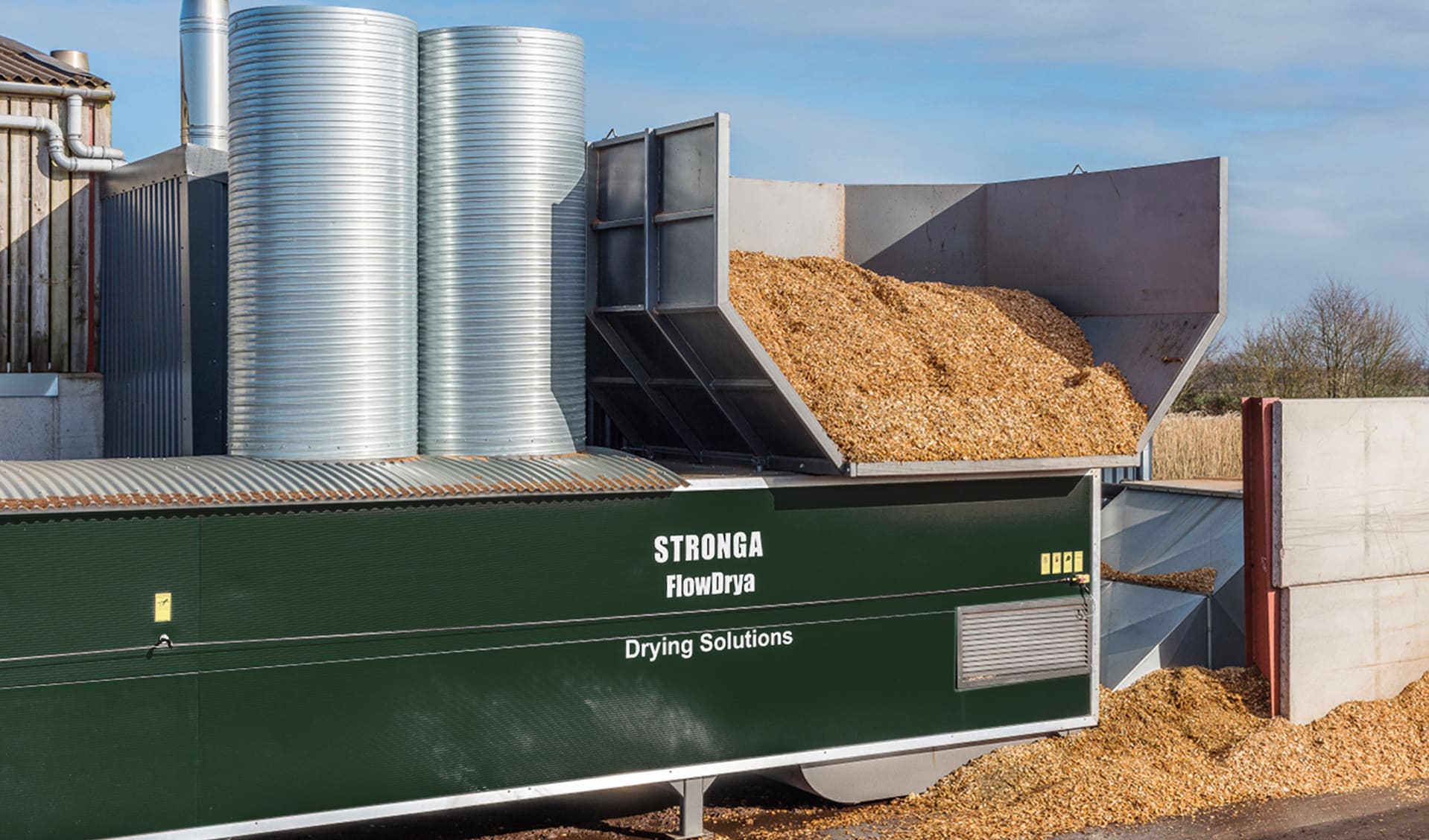